Warehouse Management System vs. Returns Management System
With online shopping being an easy option for both customers and brands, still there are instances of unfulfillment that are outsourced by brands like - delivery management, efficient warehouse, returns management, and others.
These features act as a critical component for businesses striving to meet customer expectations and stay in the competitive market.
Two essential tools for achieving these goals are Warehouse Management Systems (WMS) and Returns Management Systems (RMS).
In this blog, we will dive into the key differences between WMS and RMS, explore their features, and weigh the pros and cons of each to help you make an informed decision about which one is right for your business.
But first things first, what is Warehouse Management System and Returns Management System
What is Warehouse Management System and Returns Management System
A Warehouse Management System (WMS) and a Returns Management System (RMS) are both software solutions used in supply chain and logistics management, but they serve different purposes within the broader context of inventory and order management.
A WMS is a software application or platform designed to optimise and manage various aspects of warehouse operations. Its primary goal is to enhance the efficiency and productivity of a warehouse or distribution centre while integrating with Return Management D2C India
A RMS on the other hand, is a specialized software solution focused on managing the process of returns or product returns within a business. Its primary purpose is to streamline and optimize the return process to improve customer satisfaction and operational efficiency. Implementing a robust Return Management Strategy for Ecommerce can significantly benefit businesses in handling returns more efficiently.
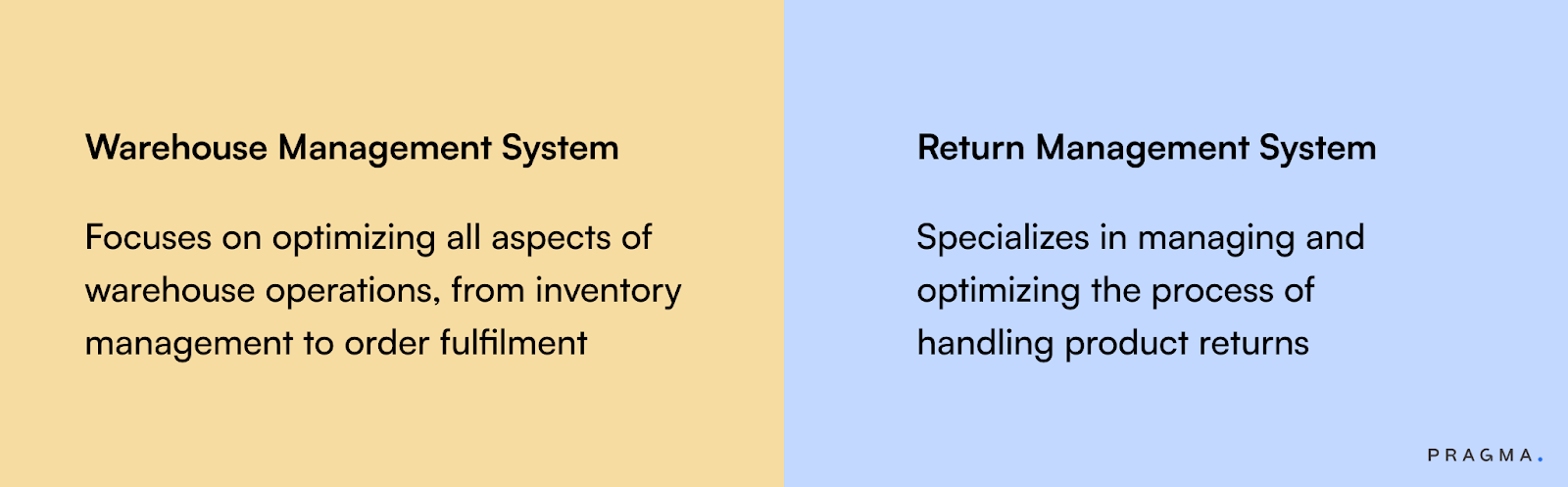
With these being the basics, let’s now understand WMS and RMS in detail below.
Key Features of a Warehouse Management System
Inventory Management
WMS is primarily designed to optimise the movement and tracking of inventory within a warehouse.
They provide real-time visibility into stock levels, enabling businesses to make informed decisions regarding stock replenishment, storage allocation, and order fulfilment.
Warehouse Location Management
It even assists in designing and managing the layout of a warehouse, optimising space utilisation, and minimising travel times for workers. It also helps with slotting, which involves assigning optimal storage locations to products.
Goods In Processes:
A WMS transforms the often chaotic receiving process into a smooth operation. It facilitates tasks like:
- Automated Receiving: Scan barcodes on incoming shipments to automatically update inventory levels and generate put-away instructions.
- Quality Control: Flag damaged or incorrect items for inspection and manage dispositions.
- Directed Putaway: Optimise storage based on item size, weight, and future retrieval needs.
Order Management
WMS solutions enhance order fulfilment processes by optimising order picking, packing, and shipping. They often include algorithms for efficient order routing and batch picking, resulting in reduced order processing times and improved order accuracy.
Shipping Management:
A WMS ensures efficient order fulfillment. It handles tasks like:
- Wave Picking: Group multiple orders for efficient picking by location.
- Pick List Generation: Optimise pick paths and minimise travel time within the warehouse.
- Packing Optimisation: Choose the right packaging materials to minimise costs and ensure damage-free delivery.
- Real-time Shipment Tracking: Provide customers with accurate shipment updates and estimated delivery times.
Order Picking and Packing:
A WMS goes beyond basic picking to optimise the process. It allows for:
1. Pick-to-Light Technology: Light-guided picking directs workers to the exact location of each item, minimising picking errors.
2. Voice Picking: Free hands for carrying orders by using voice commands to confirm selections.
3. Packing Optimisation: Recommend the most efficient box size for each order, reducing costs and waste.
4. Multi-order Picking: Combine picking for multiple orders to minimise travel time and speed up fulfillment.
Returns Management:
A WMS simplifies the often complex returns process. It assists with:
- Return Authorisation and Tracking: Generate return labels, track incoming returns, and notify customers of the process status.
- Inspection and Repackaging: Assess returned items for damage or defects and manage restocking or refunds as needed.
- Data Analysis: Identify trends in returns to understand customer behavior and improve product quality or shipping practices.
Integrations and Mobile Functionality:
These features enhance WMS functionality and user experience:
Integrations: Connect the WMS with other business systems like accounting software for automatic invoicing or sales platforms for real-time inventory updates.
Mobile Functionality:
Empower warehouse staff with smartphones or tablets to access real-time inventory data, scan barcodes, manage tasks, and update order statuses on the go. This increases efficiency and flexibility within the warehouse environment.
Reporting and Analytics
Brands typically need robust reporting and analytics tools that allow businesses to monitor KPIs. A WMS provides this data-driven approach helps identify areas for improvement and supports strategic decision-making.
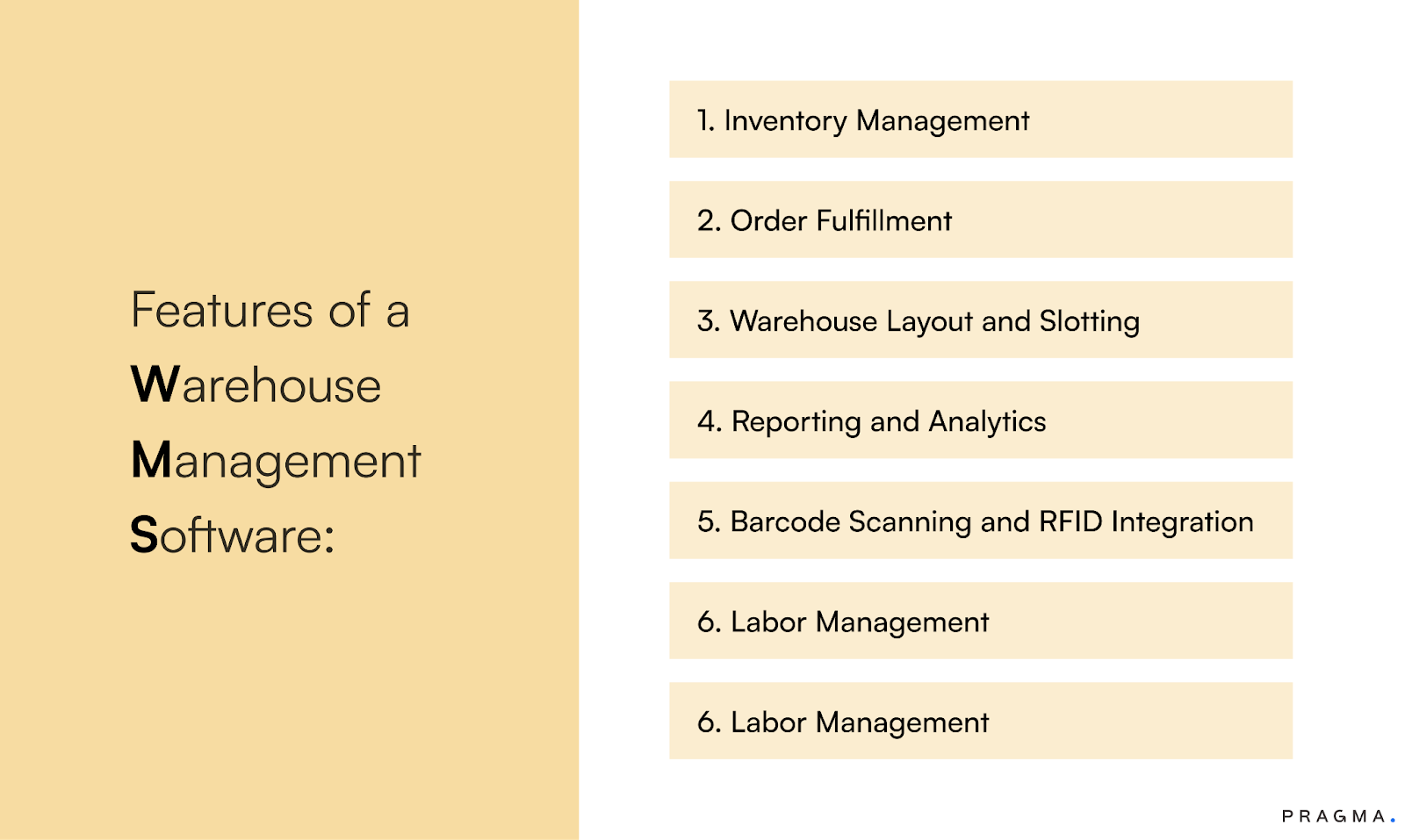
Returns Management Software Features
An RMS is a software that handles the product return cycle - from initiation to ticket closure with the Best Return Management Software.
It’s wrong to say that an RMS competes with WMS, rather RMS fills a gap that was later realised - fulfilment of returned products.
Let’s understand its key features below:
Simplifies the Return Authorization process
RMS focuses on simplifying and streamlining the returns process. They automate the returns authorization process, making it easier for customers to request returns and for businesses to approve or deny them based on predefined criteria.
Routing and Disposition of returned items
RMS software helps determine the most appropriate routing and disposition of returned items. It can automatically route items to specific locations, such as restocking inventory, sending them to a quality control department, or disposing of damaged goods.
This ensures that returned items are processed quickly and effectively.
Automates Refund Processing
For e-commerce businesses, processing refunds promptly is essential for customer satisfaction. RMS solutions often include features for automating the refund process, ensuring that customers receive their refunds in a timely manner.
Builds strategies backed on Data
Returns Management Systems provide valuable insights into the reasons for returns and the overall return trends.
Pragma RMS can provide In-depth analytics on product performance, and pincode performance. This data can then be used to identify product quality issues, improve product descriptions and images, and reduce the rate of returns over time.
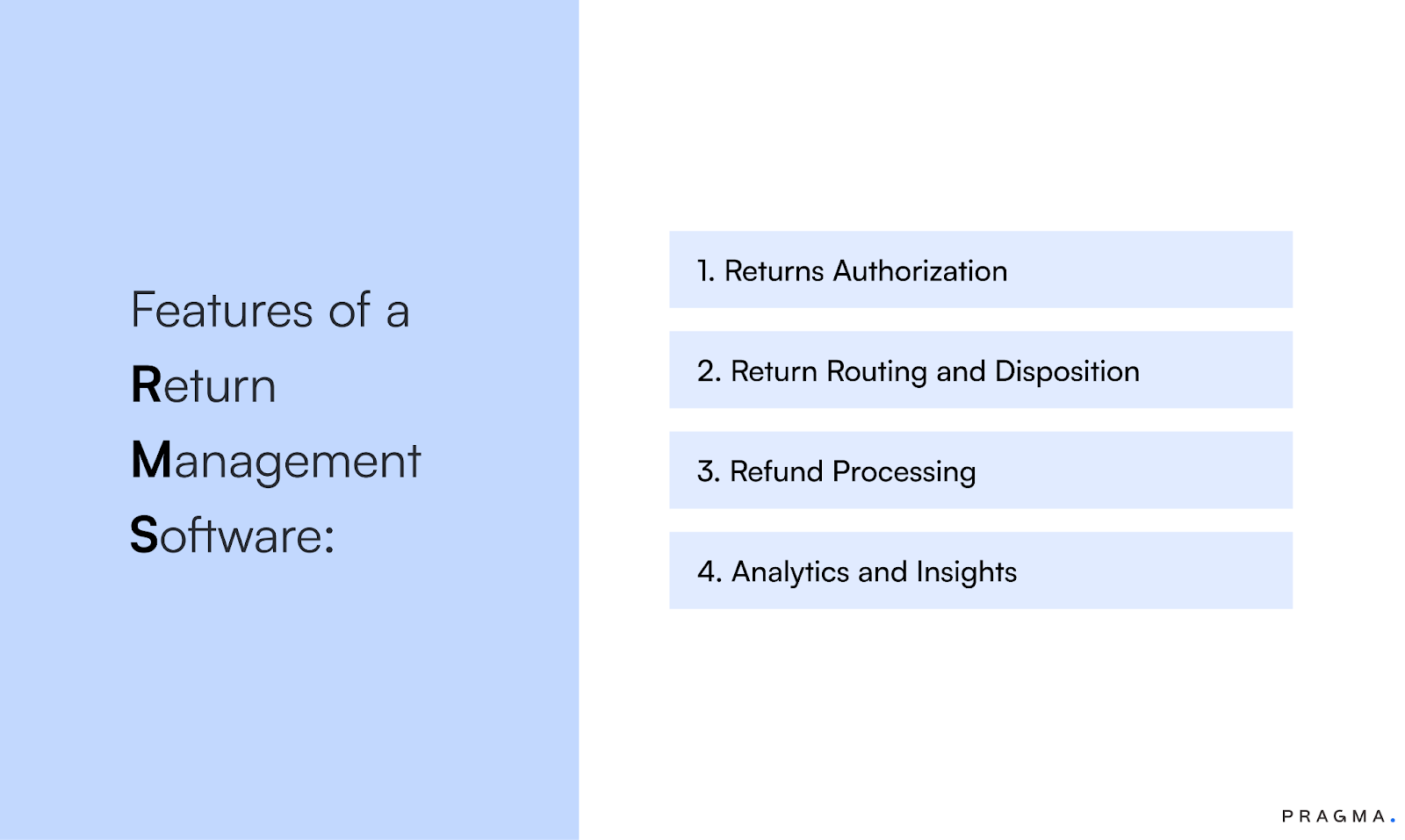
WMS vs. RMS for Returns: Pros, Cons, & Which Is Right for You
With those being the features of WMS and RMS, let’s now head to a comparative study of these two.
Let’s check the Pros and Cons of both of these tools:
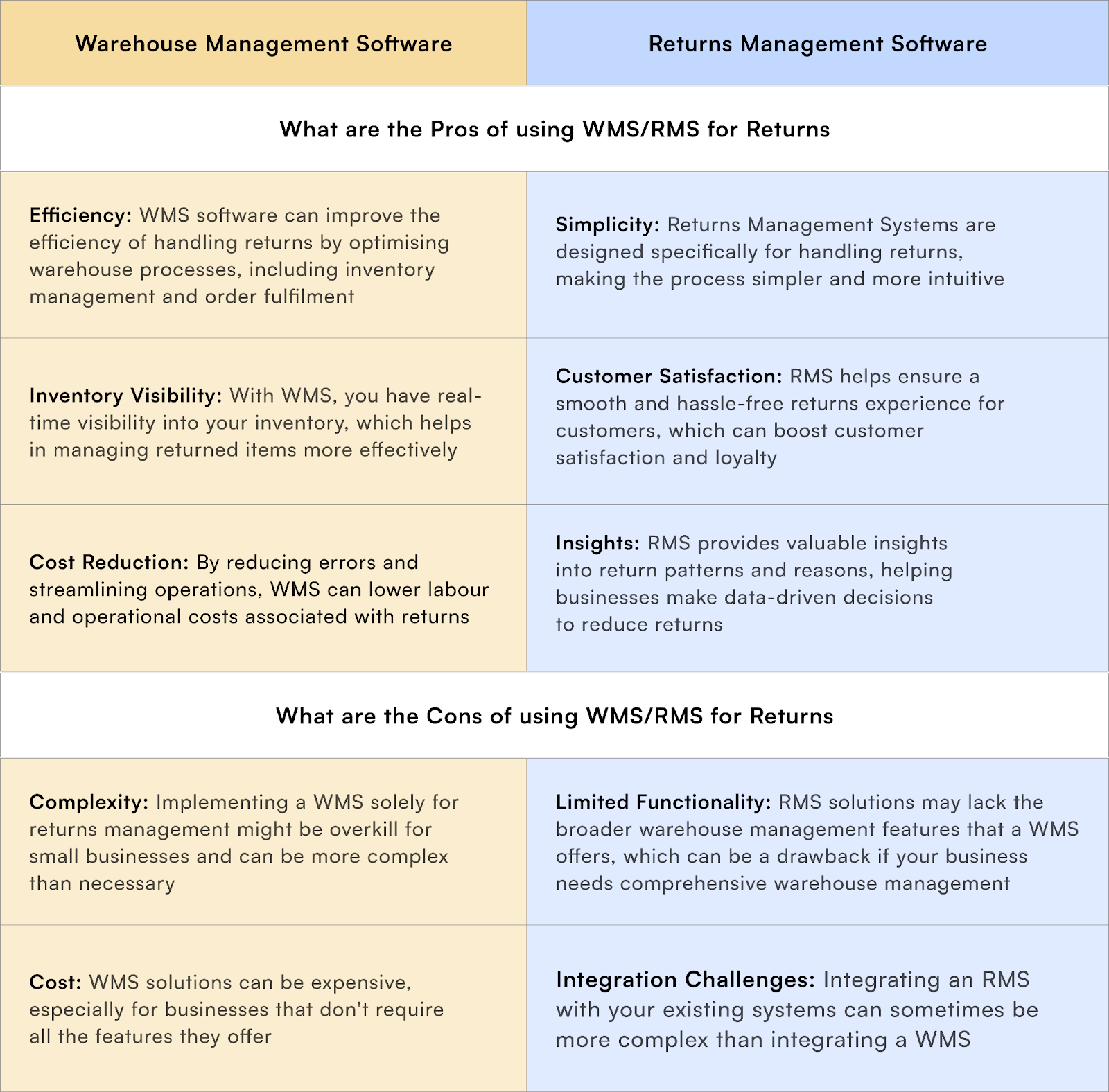
Difference between Inventory Management and Warehouse Management
Inventory management and warehouse management are both crucial aspects of supply chain management, especially in the direct-to-consumer (D2C) industry. While they are related and often overlap, they focus on different stages and aspects of the supply chain process.
- Inventory Management:
- Definition: Inventory management involves overseeing the flow of goods from manufacturers to warehouses and ultimately to retailers or directly to consumers. It encompasses the processes and systems used to track and manage stocked goods effectively.
- Key Functions:
- Demand Forecasting: Predicting customer demand to optimize stock levels and prevent stockouts or overstocking.
- Stock Replenishment: Ordering, receiving, and stocking products based on demand forecasts and inventory levels.
- Inventory Tracking: Monitoring the movement of goods in real-time, including stock levels, location, and status.
- Inventory Optimization: Balancing inventory levels to minimize carrying costs while ensuring sufficient stock availability.
- Inventory Valuation: Assigning value to inventory for financial reporting purposes and assessing profitability.
- Goal: The primary goal of inventory management is to ensure that the right products are available in the right quantities, at the right locations, and at the right time to meet customer demand while minimizing holding costs.
- Warehouse Management:
- Definition: Warehouse management involves the physical storage and movement of goods within a warehouse or distribution center. It focuses on optimizing warehouse operations to facilitate efficient order fulfillment and inventory management.
- Key Functions:
- Receiving: Unloading incoming shipments, inspecting goods, and transferring them to storage locations.
- Storage: Organizing and storing goods within the warehouse based on factors like size, weight, and demand.
- Order Picking: Retrieving items from storage to fulfill customer orders accurately and efficiently.
- Packing: Packaging products for shipment, including labeling and documentation.
- Shipping: Preparing shipments for delivery to customers or other destinations.
- Inventory Control: Conducting regular audits and cycle counts to maintain accurate inventory records.
- Goal: The primary goal of warehouse management is to optimize warehouse operations to ensure timely and accurate order fulfillment while minimizing handling and storage costs.
Choosing your Warehouse Management System
When deciding between a Warehouse Management System (WMS) and a Returns Management System (RMS) for returns management, consider the following factors:
- Business Size
- Integration
- Budget
- Customer Experience
- Data Insights
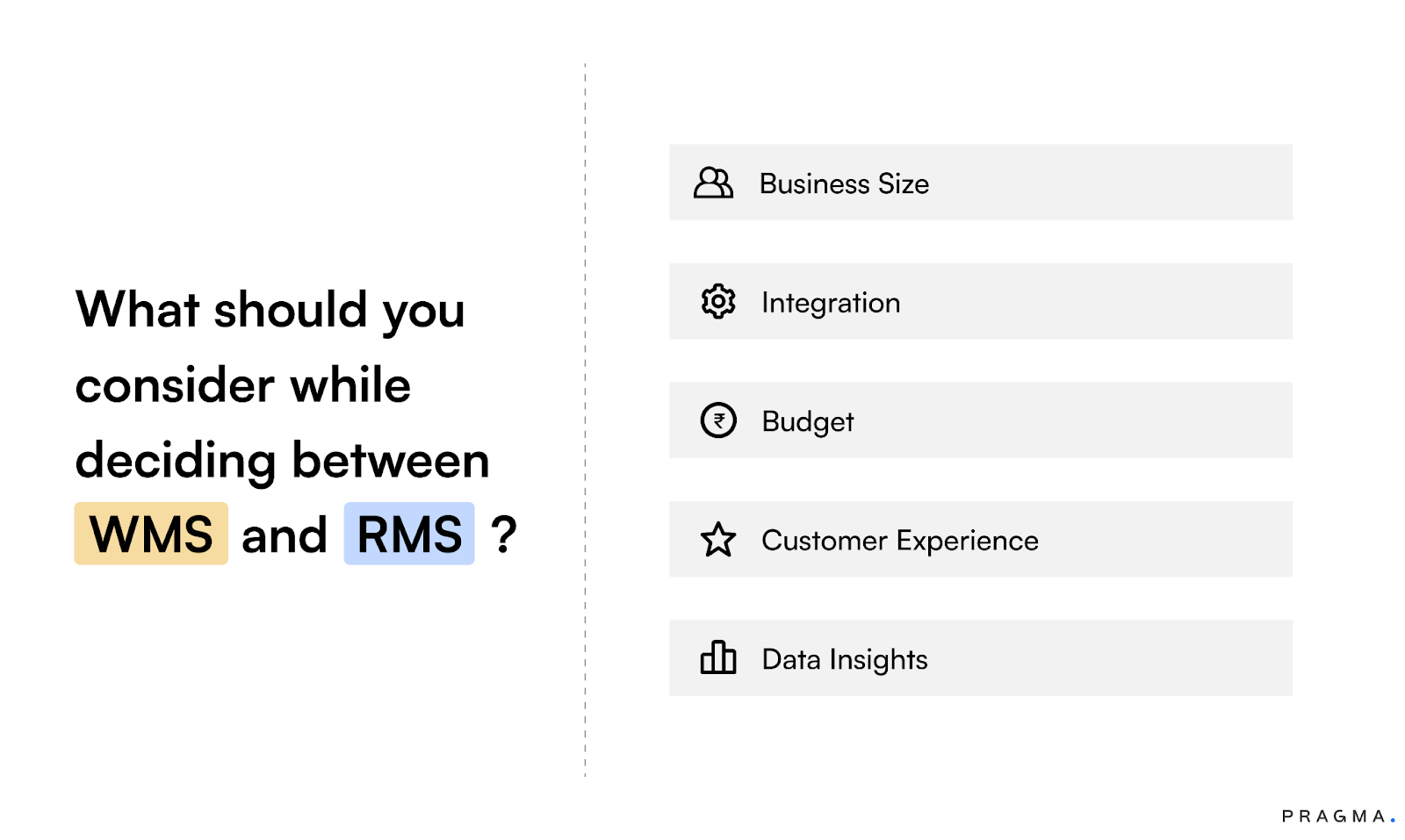
We’re analysing millions of return orders. Right from cosmetic brands to apparel, but one thing we recognised is that a product that gets a 5-star rating from a customer might get a 1-star rating from another.
With that being said, it even becomes important for you to flag inappropriate users, or return queries that might be fraudulent in nature. Trust us, you can’t manually do this process as once your platform scales and you’re getting hundreds of return requests each day, it’s tough.
With this, we’re towards the end of this exhaustive guide that explains everything about what features you should consider while opting for an RMS for your platform.
With Pragma leading the race in terms of
- Access to Live data to build strategies on the go
- One-click return/exchange request for users
- Perform QC, Generate payment links in a single place
- Flagging of risky users during order placement/return
- 100% support during onboarding, setup and any time after
It’s time for you to try out Pragma and help you increase your revenue and reduce return order rates.
FAQs
1. What's the main difference between a WMS and an RMS?
A Warehouse Management System (WMS) focuses on the efficient flow of inbound goods, from receiving and storage to picking and shipping orders. A Returns Management System (RMS) specialises in handling outbound goods, tracking returns, processing them upon arrival (inspection, restocking, or refunds), and providing data insights.
2. Can a WMS handle returns?
Some WMS offer basic return functionalities like receiving and tracking returned items. However, a dedicated RMS offers more robust features, like automating return workflows, managing complex return rules, and providing in-depth analytics to optimise return processes.
3. When do I need an RMS in addition to a WMS?
If you experience a high volume of returns, have complex return policies, or require detailed return data analysis, an RMS complements your WMS by streamlining return operations and providing valuable insights for improvement.
4. What are some benefits of integrating a WMS with an RMS?
By integrating these systems, you gain real-time visibility into both inbound and outbound goods. This allows for smoother inventory management, faster refund processing, and improved overall customer satisfaction with the returns experience.
5. What are some key features to look for in an RMS?
Look for features like:
- Automated return workflows and RMA (Return Merchandise Authorization) generation
- Ability to manage multiple return channels (online, in-store)
- Detailed return tracking and analytics dashboards
- Integration capabilities with your existing WMS and other business systems
- Support for multiple return scenarios (restocking, refunds, exchanges)
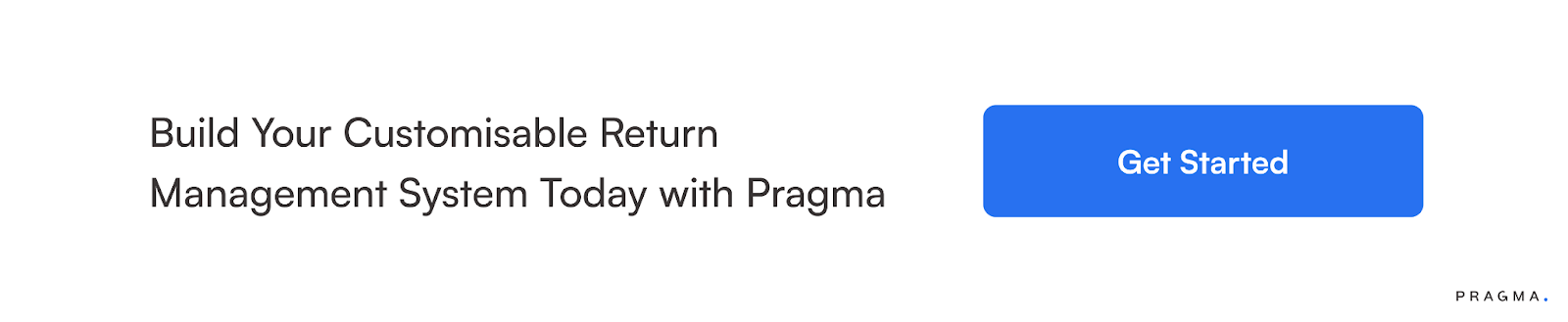
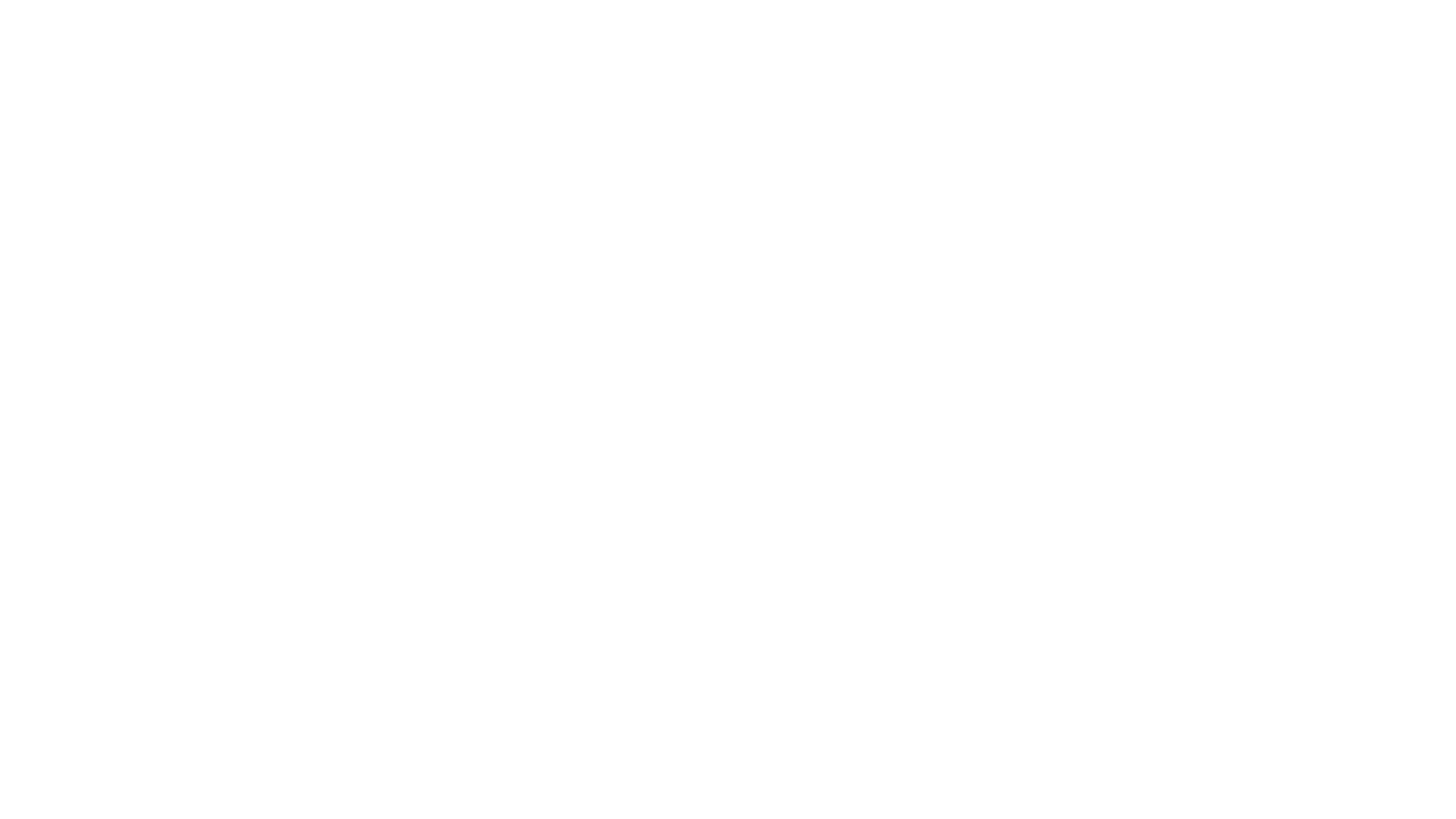
Talk to our experts for a customised solution that can maximise your sales funnel
Book a demo