Picture this, your warehouse is processing 500+ orders daily, but stockouts are increasing, shipments are delayed, and customer complaints are piling up.
Sound familiar? For growing D2C brands, these warehouse headaches can quickly become roadblocks to scaling.
This is where a warehouse management system (WMS) solves this chaos into smooth, efficient operations.
It automates and optimises your entire warehouse workflow—from receiving and storage to picking, packing, and shipping. It means fewer errors, faster fulfilment, and happier customers.
In this guide, you’ll learn how to
- Select a WMS that fits your unique business needs
- Roll out the system without disrupting daily operations
- Use data insights to continuously improve warehouse performance
- Solve common warehouse bottlenecks
- Build operations that can handle 10x growth
We'll walk through everything from system types and core features to implementation steps and industry best practices.
What is a Warehouse Management System (WMS)?
A warehouse management system (WMS) is software that helps you control and manage daily warehouse operations.
From the moment goods enter your warehouse until they leave, a WMS tracks and controls every movement and storage operation.
It acts as your warehouse's central nervous system—which coordinates all activities including
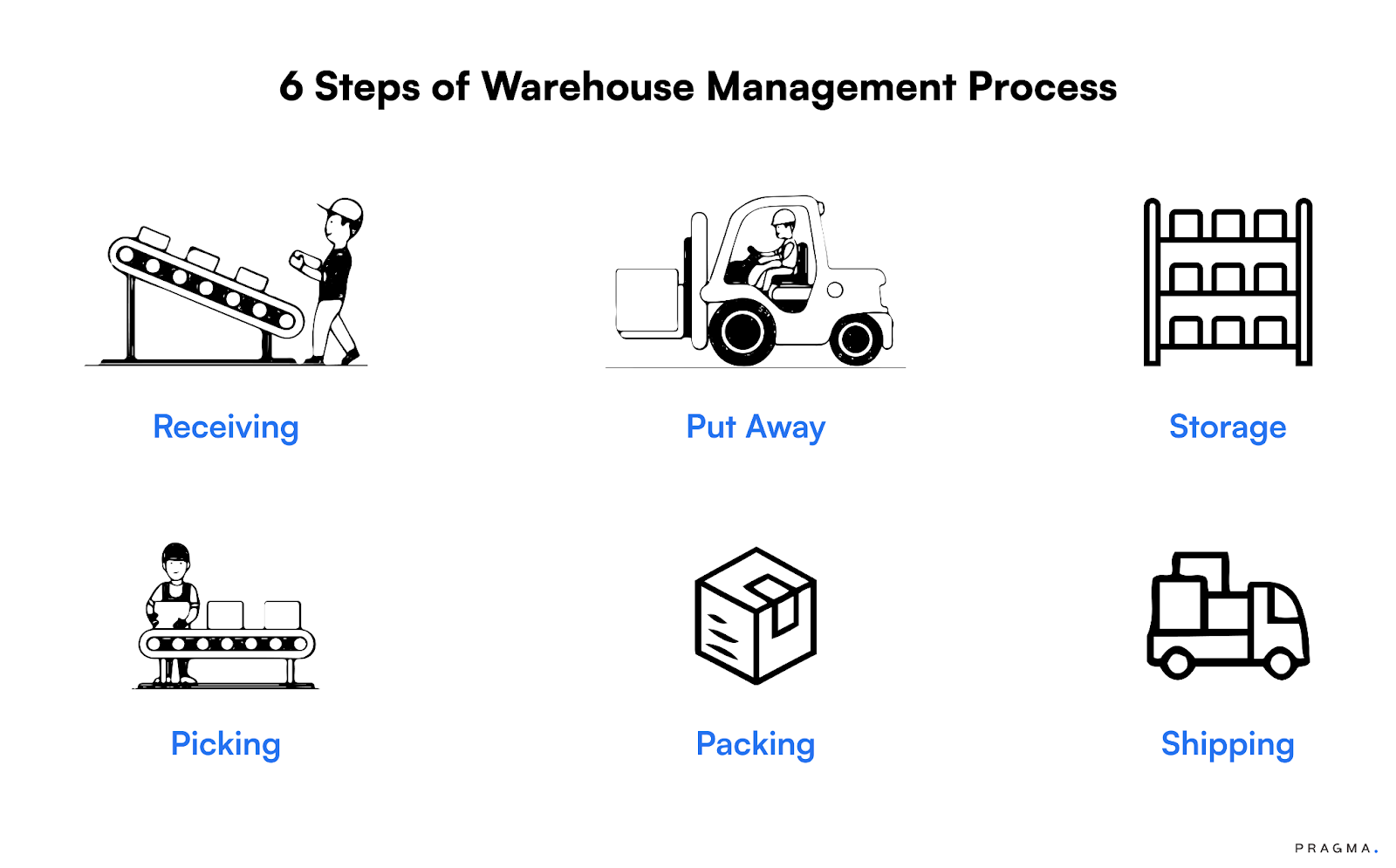
6 Step of the Warehouse Management Processes
- Receiving
- Put-away
- Storage
- Picking
- Packing
- Shipping
And maintains accurate inventory records.
Apart from tracking where items are stored, it optimises your entire warehousing process through intelligent storage suggestions, picking routes, and real-time inventory updates.
But inventory movement isn't just about outgoing orders—returns add another layer of complexity.
This is why many brands use both warehouse management systems and returns management systems to handle the complete cycle of product movement.
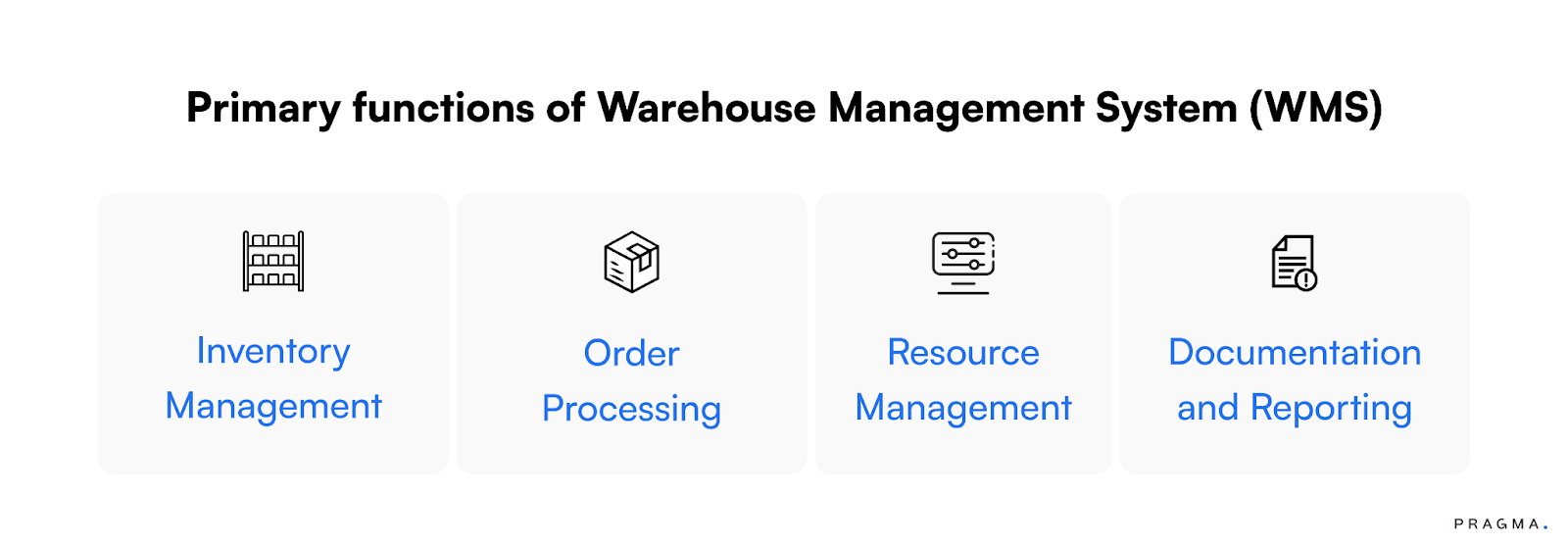
Warehouse Management System Function
- Inventory Management
- Real-time tracking of stock levels
- Monitoring product locations and movements
- Managing multiple storage locations
- Stock rotation and ageing management
- Order Processing
- Order receipt and validation
- Pick list generation
- Packing and shipping coordination
- Order status tracking
- Resource Management
- Labour planning and task assignment
- Equipment utilisation tracking
- Performance monitoring
- Workload distribution
- Documentation and Reporting
- Automated documentation generation
- Real-time analytics and reporting
- Performance metrics tracking
- Compliance documentation
A WMS integrates with your other systems like Enterprise Resource Planning (ERP) software, Transportation Management Systems (TMS), and accounting software to provide better data flow across operations.
Helping all your departments work with the same accurate, up-to-date information.
Types of Warehouse Management Systems
Warehouse management systems come in different types to suit various business needs and budgets.
Whether you manage your own warehouse or partner with third-party logistics providers, understanding these options helps you pick the right solution.
Here are five commonly used WMS

- Standalone WMS
A standalone warehouse management system is independent software focused solely on warehouse operations.
It works well for businesses that need specialised warehouse management without integration with other business systems.
Key characteristics
- Quick implementation
- Lower initial costs
- Focused functionality
- Easier to learn and use
- Suitable for small to medium warehouses
- Cloud-based WMS
Cloud-based or Software-as-a-Service (SaaS) warehouse management systems run on remote servers and are accessed through the Internet without heavy infrastructure investment.
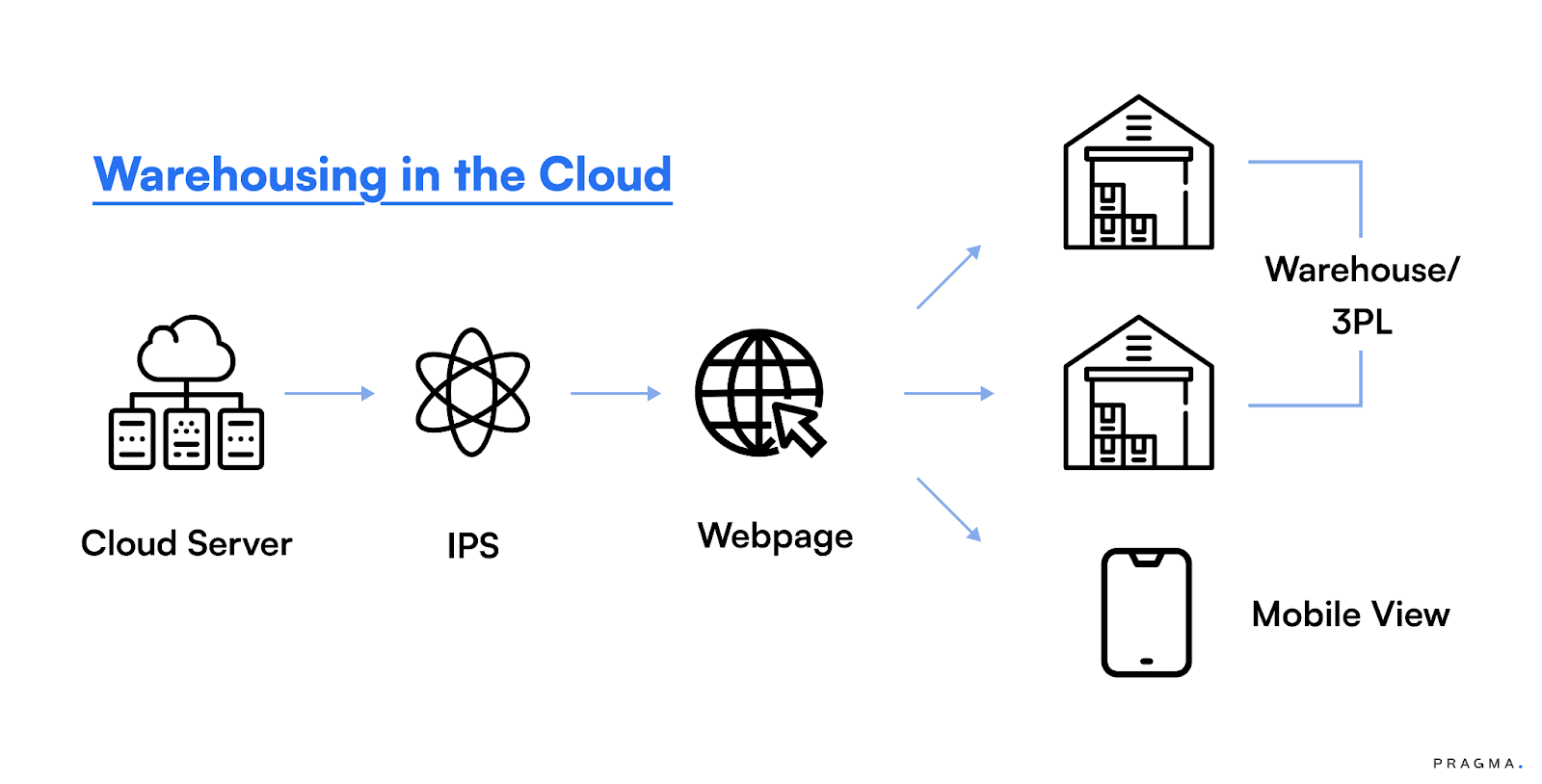
Advantages
- Minimum IT infrastructure costs
- Automatic updates and maintenance
- Access from anywhere
- Pay-as-you-go pricing
- Quick deployment
- Easy scaling as scale grows
They also integrate customer communications directly into order management.
For example, platforms like Pragma offer WhatsApp Business Suite integration, to help you convert more sales and retain customers through a messaging platform they already use daily.
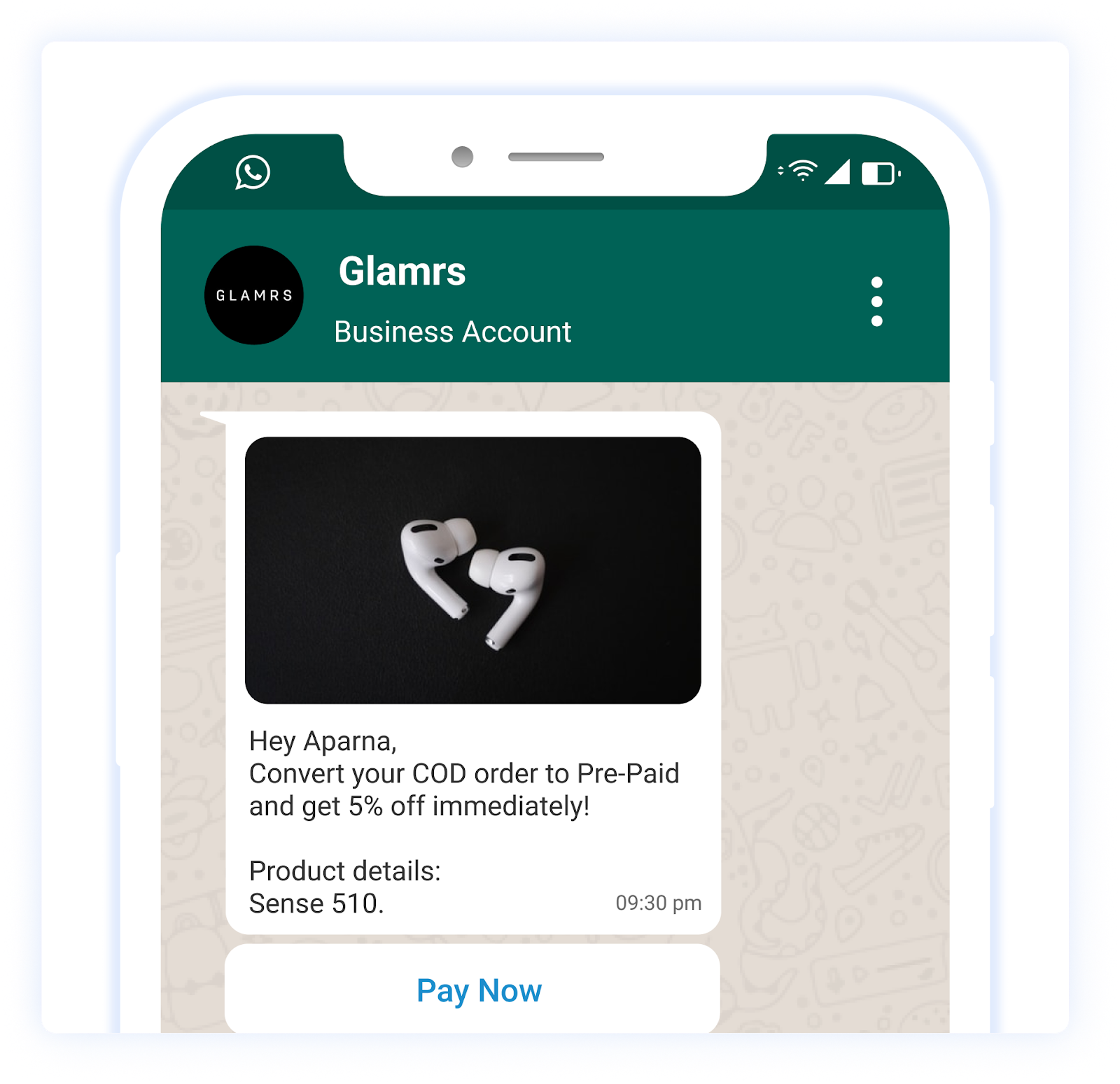
Making it easy for you to
- Let customers browse products and place orders through WhatsApp
- Send automatic order confirmation and tracking updates
- Reduce cart abandonment through timely reminder messages
- Provide instant responses to order and product queries
- Manage customer support through a single dashboard
This direct channel turns the WMS into a complete order management platform, making it convenient for customers to shop and track orders.
- Supply Chain Module WMS
These systems are part of larger supply chain management solutions.
They integrate your warehouse activities with other supply chain functions like transportation, procurement, and demand planning.
Features
- End-to-end supply chain visibility
- Integrated planning and execution
- Shared data across the supply chain
- Better coordination between departments
- Advanced analytics capabilities
- ERP-based WMS
ERP-based warehouse management systems are modules within Enterprise Resource Planning software.
They're ideal for businesses that want tight integration between warehouse operations and other functions.
Benefits
- Improved data flow between teams
- Single database for all operations
- Unified interface across modules
- Real-time financial impact tracking
- Better reporting
- Open Source WMS
Open-source warehouse management systems provide basic functionality with the ability to customise the code according to specific needs.
Characteristics
- No licensing costs
- Customisable code
- Community support
- Suitable for tech-savvy teams
- Requires development expertise
Benefits of a Warehouse Management System
Five major benefits that make WMS invaluable for your growing brands.
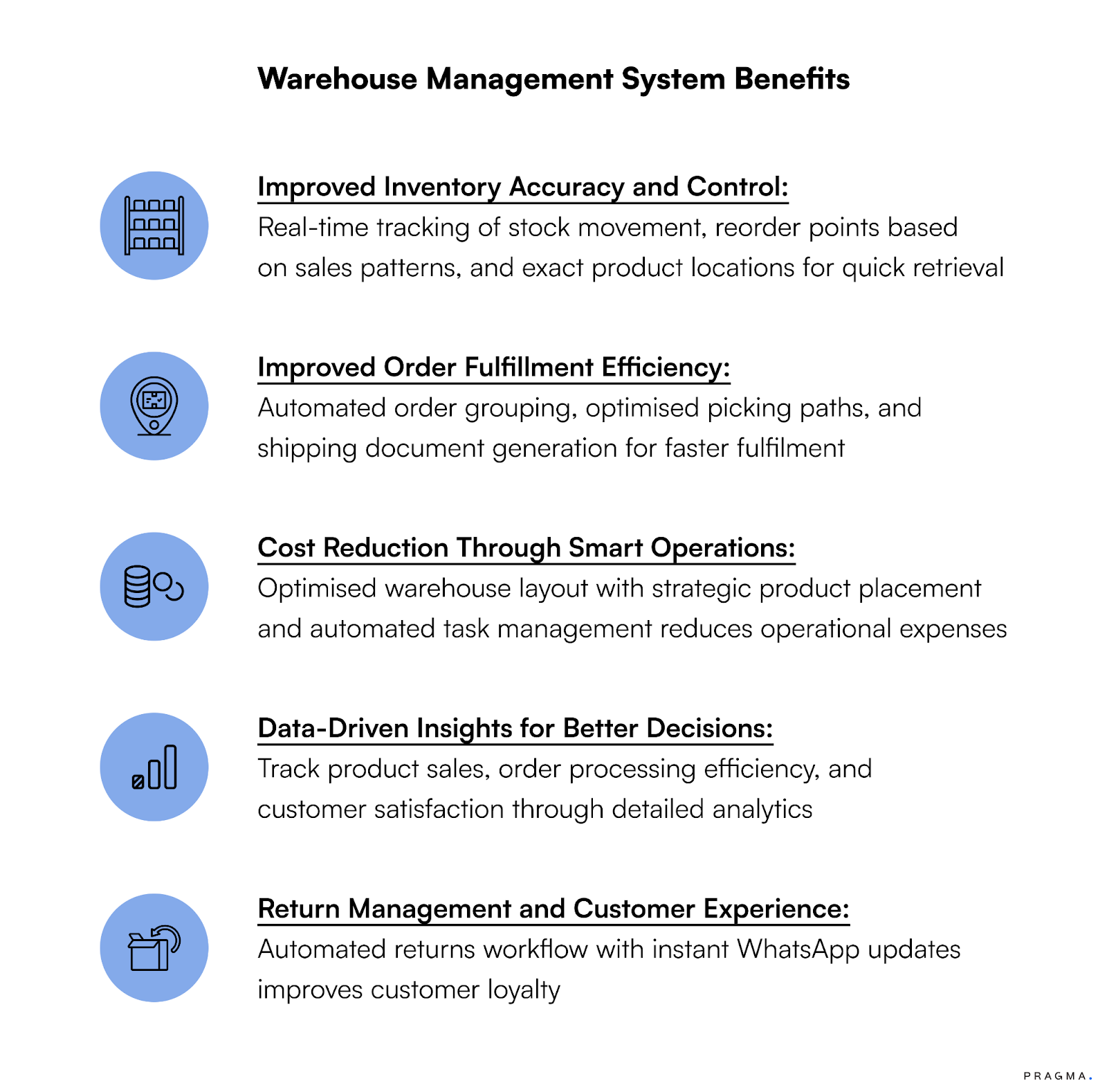
Improved Inventory Accuracy and Control
When you implement a WMS, you gain precise control over your inventory.
The system maintains accurate, real-time stock levels by tracking every product movement within your warehouse to help prevent stockouts that could cost you sales and avoid excess inventory holding.
A WMS automatically monitors stock levels and can suggest optimal reorder points based on your sales patterns and lead times.
It also tracks product locations precisely, making it simple for your staff to find and retrieve items quickly.
This location tracking combined with batch and lot tracking ensures proper stock rotation, reducing losses from expired or obsolete inventory.
Improved Order Fulfillment Efficiency
A WMS makes order fulfilment more efficient by processing incoming orders and creating optimal picking sequences that reduce the walking distance for warehouse workers and the time spent on each order.
And if you sell through multi-channel, the WMS will prioritise orders based on shipping deadlines and order values.
When orders arrive, the system
- Creates efficient picking paths
- Groups similar orders to save time
- Validates picked items against orders
- Generates accurate shipping documentation
Helping you avoid errors and speeds up order processing, so you can handle more orders without adding more people.
Cost Reduction Through Smart Operations
A WMS optimises your warehouse layout to make the best use of available space.
Fast-moving items are placed in easily accessible locations, while slow-moving stock is stored in less prime areas.
Allowing your team to spend less time searching for products and maximise storage density.
Labour costs decrease as workers become more productive because the system assigns tasks efficiently and eliminates time wasted on paper-based processes.
Inventory holding costs drop as it helps you maintain optimal stock levels. So you order only what you need when you need it.
Data-Driven Insights for Better Decisions
The reporting capabilities of a WMS help you analyse
- Which products sell quickly, which ones sit on shelves, and how inventory turns vary by season helps you make smarter purchasing decisions.
- Detailed data about order processing times, picking accuracy, and labour productivity to spot bottlenecks and improve processes.
- Customer satisfaction drivers by tracking order accuracy, shipping times, and returns.
Return Management and Customer Experience
A warehouse management system improves returns processing, making it less of a burden on your operations.
It tracks returned items, manages their inspection, and updates inventory records automatically to help you process refunds faster and identify quality issues before they affect more customers.
For instance, Pragma's return management software automates the entire returns workflow—from customer initiation to refund processing, while maintaining real-time visibility through WhatsApp notifications.
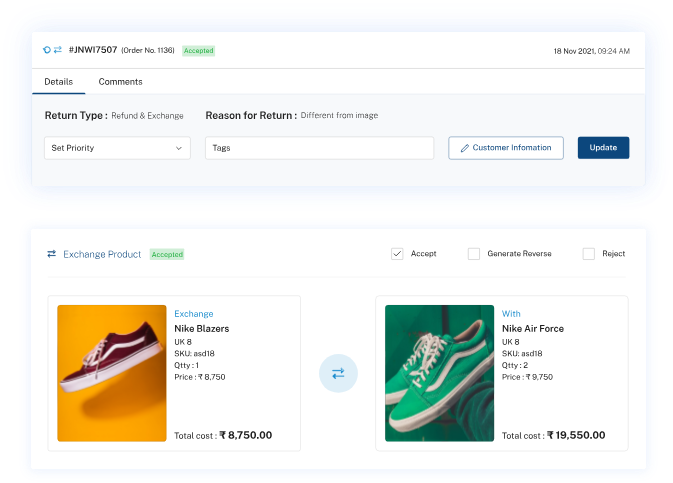
The improved accuracy in order fulfilment, faster processing times, and efficient returns handling result in happier customers.
When customers consistently receive the right products on time, they're more likely to order again and recommend your brand to others.
Key Features of a Warehouse Management System
Five main features that make these WMS valuable for your growing brand.
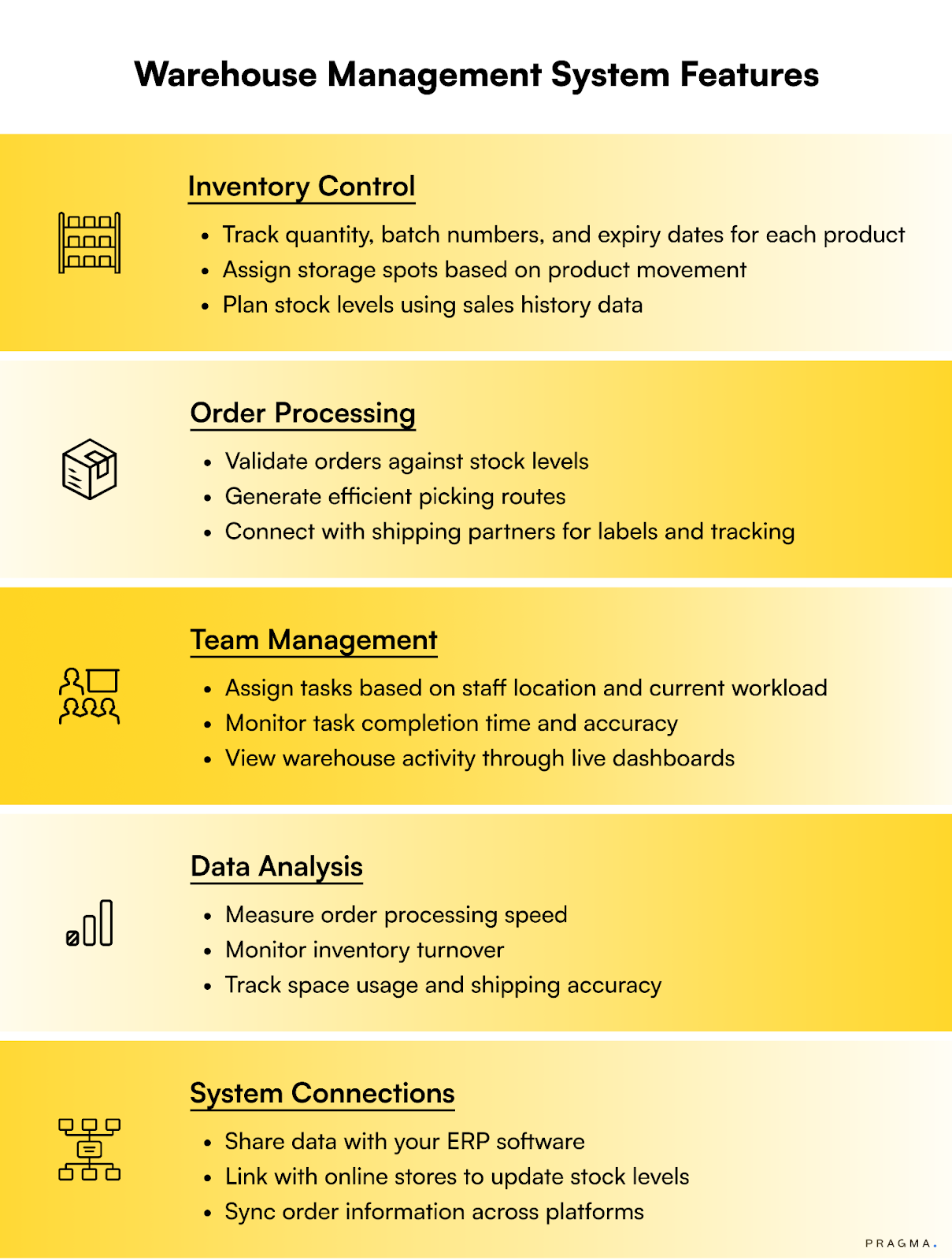
Inventory Management and Tracking
The core strength of a WMS is in its inventory management as it helps you maintain accurate records of
- Stock Levels and Movement: Every product entering or leaving your warehouse gets tracked with specifics like quantity, batch numbers, and expiry dates. The system updates these records automatically as items move through different stages.
- Location Management: The WMS assigns and tracks storage locations based on product characteristics and movement patterns. So your team can find items and stock counting easily.
- Demand Forecasting: Using historical data, the system helps predict future inventory needs, suggesting optimal order quantities and timing to maintain sufficient stock levels.
Order Management
A WMS handles the complete order lifecycle
- Order Processing: When orders arrive, the system validates them against available stock and creates picking lists. It groups orders efficiently to speed up processing while maintaining accuracy.
- Pick Path Optimisation: It creates the most efficient routes for picking items, making order fulfilment faster and less tiring for workers.
- Shipping Integration: The WMS automatically connects with shipping carriers to generate labels, track shipments, and update order status.
Labour Management
WMS assigns tasks to your staff based on their location and workload. It tracks completion times and accuracy, helping managers identify training needs.
And allows managers to see real-time updates on order processing status, worker productivity, and overall warehouse activities through dashboards and reports.
Reporting and Analytics
The WMS gathers data about every warehouse operation, from receiving to shipping, and creates a detailed record of your operations, such as
- Order processing speed
- Inventory turnover rates
- Worker productivity
- Space utilisation
- Shipping accuracy
Integration Capabilities
The warehouse management system works with your ERP system to share data about orders, inventory, and financials. Keeping all your business systems updated with accurate information.
For online sellers, it connects with your e-commerce platforms to receive orders and automatically update inventory levels.
The Workflow of a Warehouse Management System
A WMS manages and directs the flow of goods from arrival to dispatch.
Here is what the workflow looks like
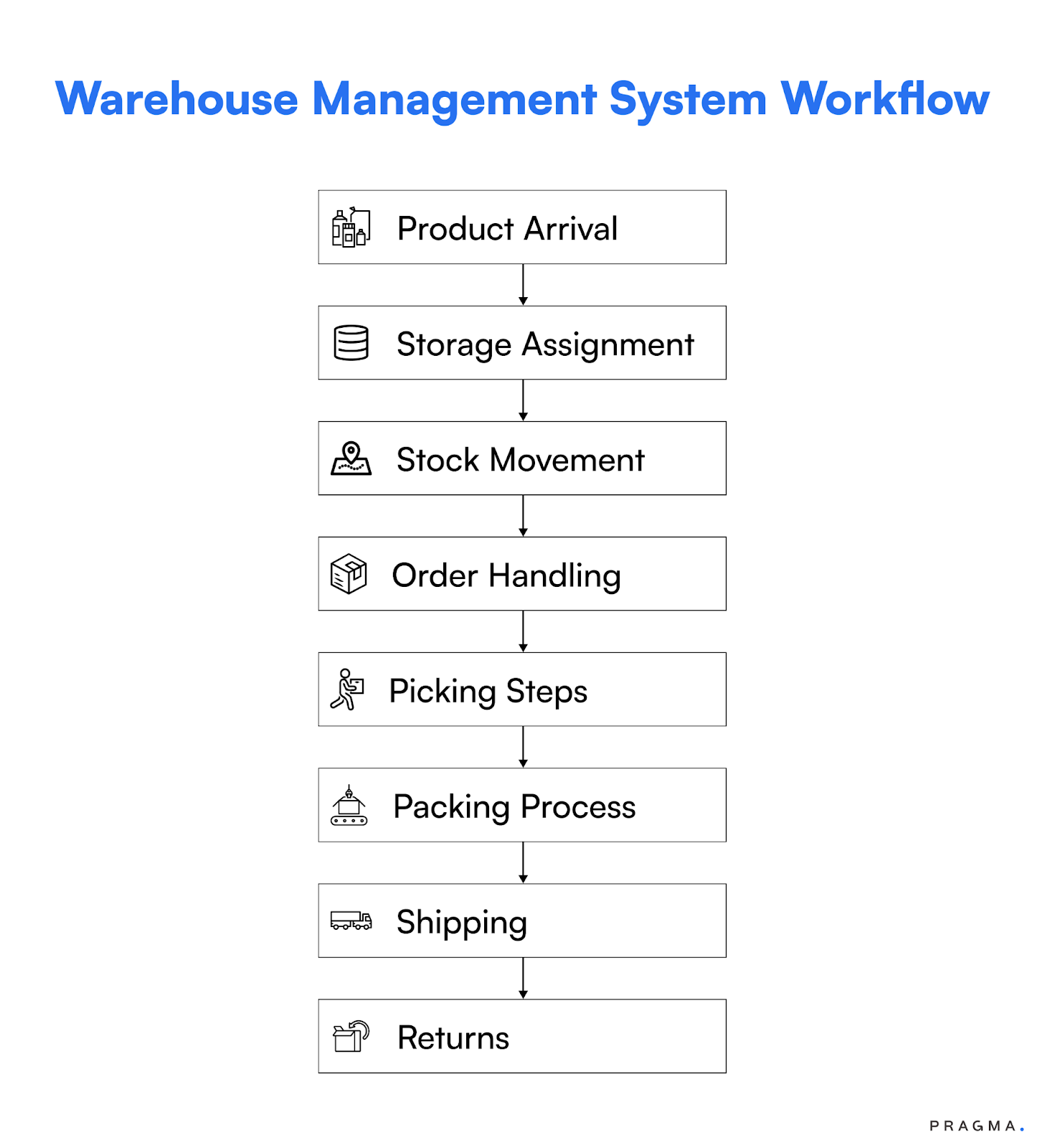
Product Arrival
- Generate receiving tasks from purchase orders
- Scan and verify product quantity and quality
- Record batch numbers and expiry dates
Storage Assignment System allocates storage spots based on:
- Product size and storage needs
- Sales frequency
- Space availability
- Layout efficiency
Stock Movement
- Move products from bulk storage to picking areas
- Schedule regular stock counts
- Match physical stock with system records
Order Handling Group orders by:
- Priority level
- Delivery needs
- Item location
- Staff availability
Picking Steps
- Assign picking lists to staff
- Show step-by-step mobile instructions
- Scan items for accuracy
- Monitor progress live
Packing Process
- Move items to the packing area
- Check order completeness
- Print packing slips and labels
- Update stock numbers
Shipping
- Connect with delivery partners
- Create shipping documents
- Update tracking details
- Send customer updates
Returns
- Log incoming returns
- Check product condition
- Update inventory
- Process refunds/replacements
- Monitor return trends
Inbound Process
It begins when inventory arrives at your facility
Receiving
- The WMS generates receiving tasks based on purchase orders
- Staff scan arriving products, confirming quantities and condition
- The system records batch numbers, expiry dates, and other product details
Put-away
The WMS directs products to specific storage locations based on
- Product characteristics (size, weight, storage requirements)
- Sales velocity (how quickly items sell)
- Available space
- Warehouse layout
It automatically updates inventory counts once items reach their assigned locations.
Internal Movement Management
Once products are stored, the WMS handles stock movement and organisation including
- Stock Replenishment: When picking locations run low, the WMS creates replenishment tasks to move products from bulk storage to picking areas.
- Inventory Counting: It also schedules and guides cycle counts, comparing physical stock against system records to maintain accuracy.
Order Processing Workflow
When customer orders arrive, the WMS initiates a series of coordinated tasks, such as
Order Grouping based on
- Order priority
- Shipping requirements
- Product location
- Available resources
Picking Process
- WMS assigns pick lists to the warehouse people
- Workers receive step-by-step instructions on mobile devices
- Each item scan confirms the correct product selection
- The system tracks progress in real-time
Order Consolidation
- Picked items move to packing stations
- WMS verifies order completeness
- The system generates packing lists and shipping labels
- Inventory records update automatically
This is where you should consider tools like Pragma that offer an automated order verification system to help you validate orders against set parameters, potentially stopping 10-15% of problematic orders before they enter the fulfilment cycle.
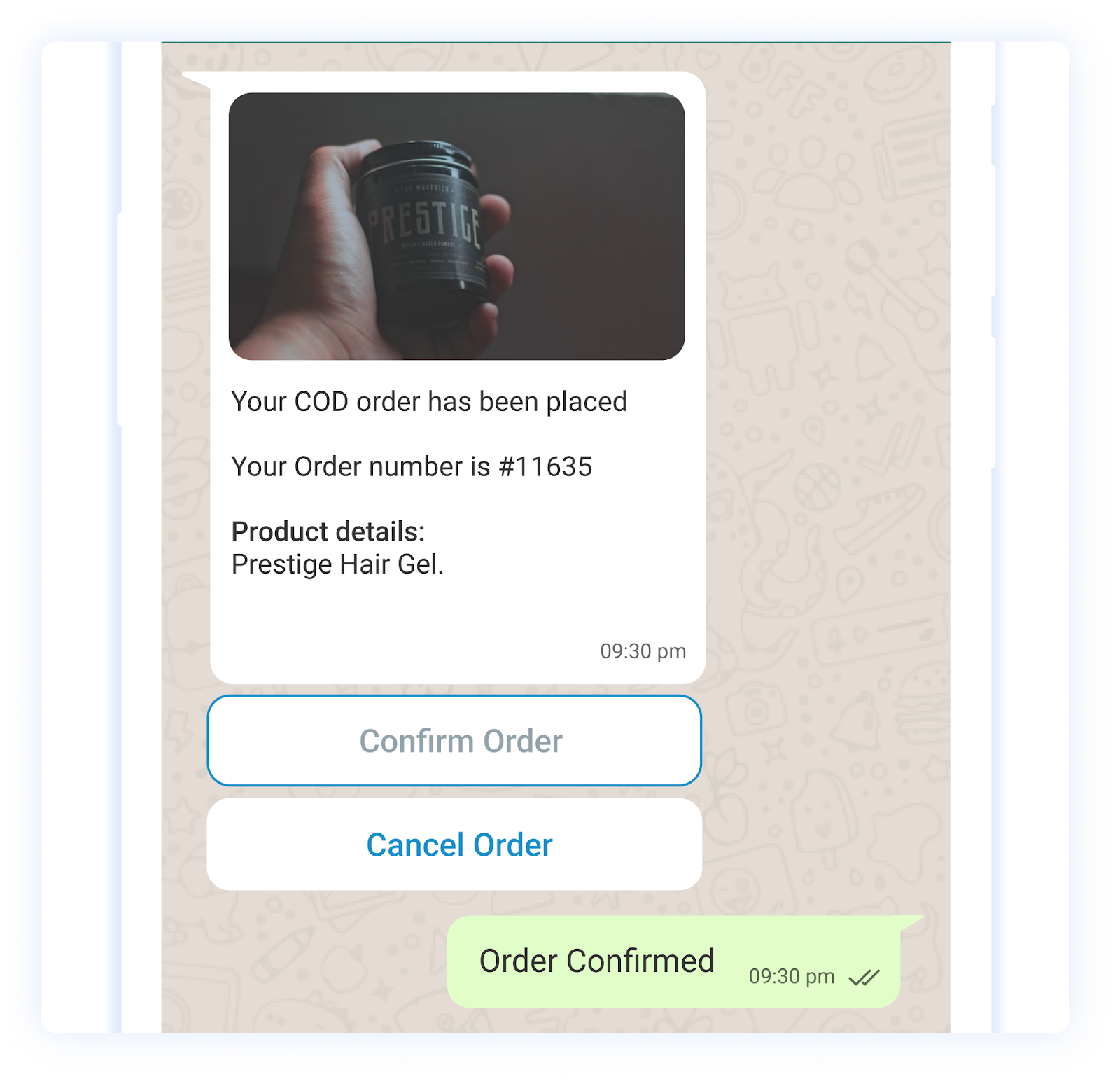
Outbound Logistics
The final stage focuses on getting orders ready for shipping
Quality Control
- The system prompts verification of order contents
- Records any discrepancies
- Updates order status
Dispatch Management
- WMS assigns orders to shipping carriers
- Generates required documentation
- Updates order tracking information
- Sends notifications to customers
Returns Processing
The WMS also manages product returns
- Registers incoming returns
- Guides inspection process
- Updates inventory based on product condition
- Manages replacement orders or refunds
- Tracks return patterns for quality control
Challenges and Solutions in Warehouse Management Systems
Running a warehouse isn't simple—from managing inventory accuracy to coordinating staff and maintaining efficient operations, managers face numerous obstacles.
Here are five main challenges in warehouse management systems and practical solutions to address them.
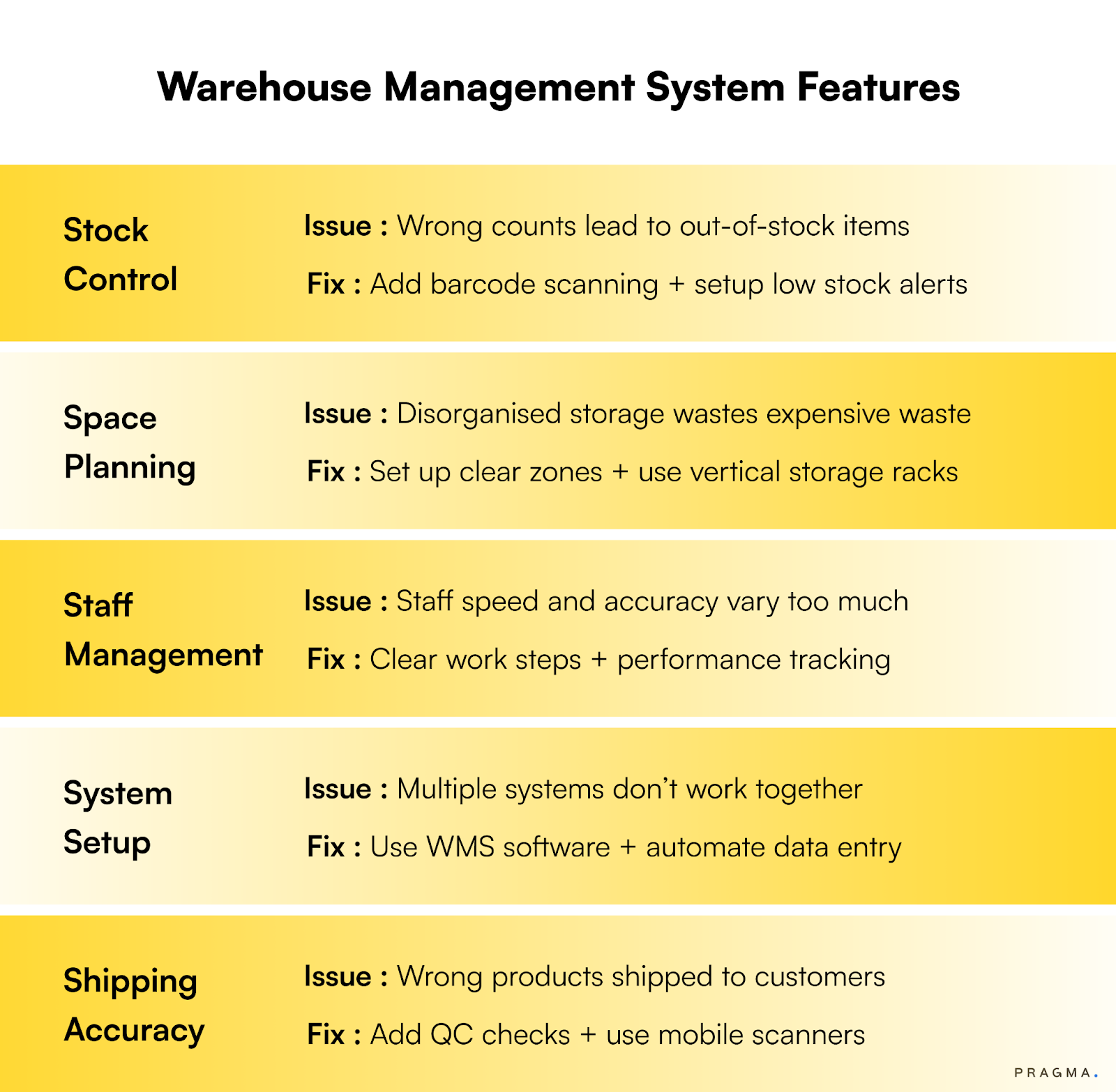
1. Inventory Accuracy and Visibility
Challenge: Poor inventory tracking leads to stockouts, overstocking, and incorrect order fulfilment.
Many warehouses struggle with real-time visibility into their stock levels and locations.
Solutions:
- Implement barcode scanning and RFID technology to track products through receiving, putaway, picking, and shipping
- Use cycle counting programs instead of relying only on annual physical counts
- Create alerts for low reorder points and stock levels
- Configure your warehouse management system to provide real-time inventory updates across locations
- Train staff on proper scanning and inventory management procedures
2. Space Optimisation and Storage
Challenge: Warehouse space is expensive, and poor utilisation increases costs.
Here’s what a typical warehouse looks like.
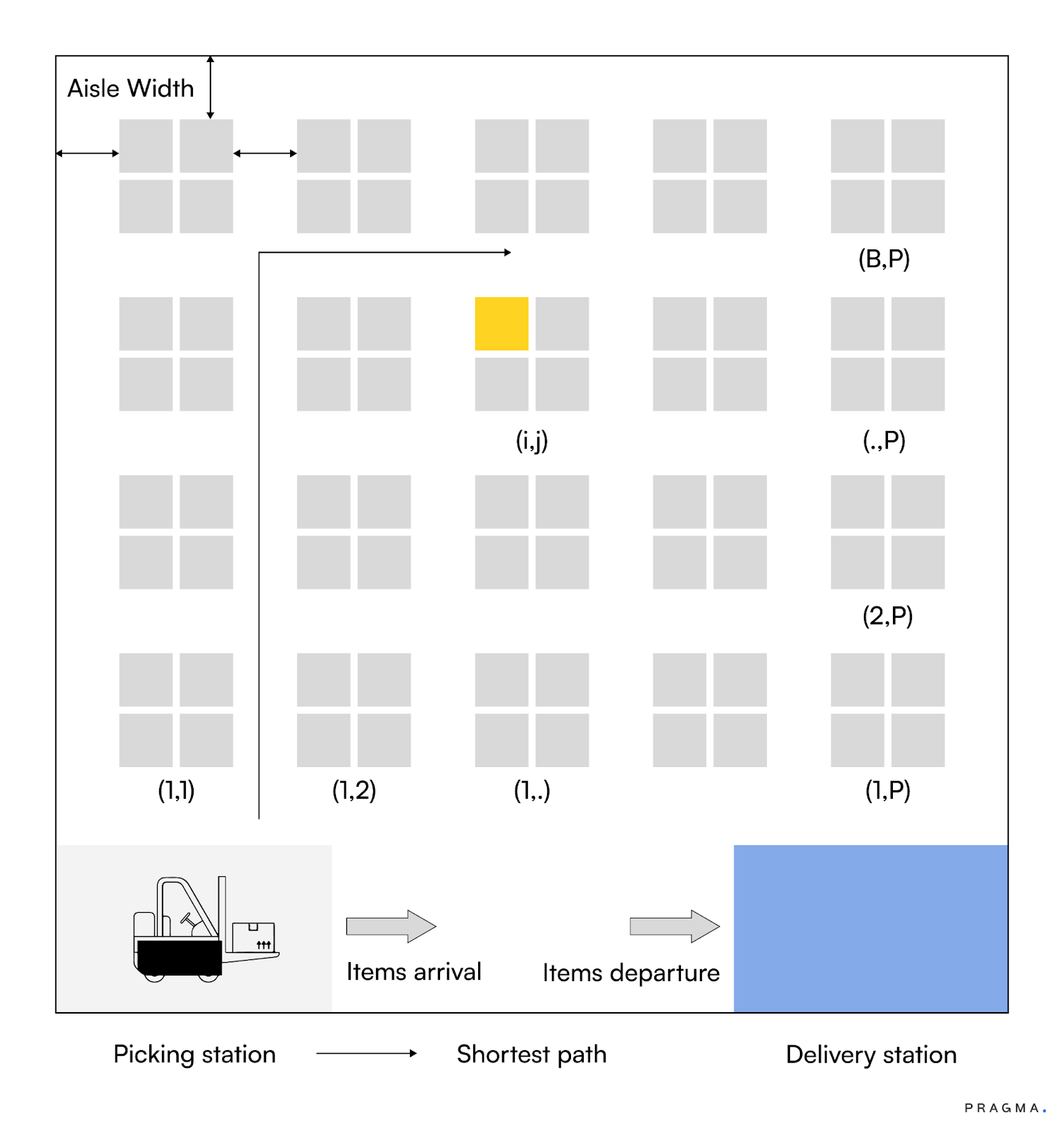
Many facilities struggle with
- Disorganised storage areas
- Inefficient use of vertical space
- Difficulty locating specific items
- Congested aisles and picking paths
Solutions:
- Analyse product dimensions, weights, and movement patterns
- Use appropriate storage systems (pallet racks, shelving, bins) based on product characteristics
- Implement dynamic slotting to position fast-moving items in easily accessible locations
- Create designated areas for different product categories
- Use vertical space efficiently with the right material-handling equipment
- Optimise storage layout based on seasonal changes
3. Labour Management and Productivity
Challenge: Managing warehouse worker's productivity while maintaining accuracy is complex. Common Issues include
- Inconsistent performance levels
- High training costs for new employees
- Difficulty tracking individual productivity
- Managing peak season labour needs
Solutions:
The right warehouse management system can help address these through
- Labour management modules that track individual performance metrics
- Mobile devices and voice-picking systems to improve accuracy
- Clear standard operating procedures (SOPs) for all warehouse tasks
- Cross-training programs to build a flexible workforce
- Data-driven staffing plans based on historical patterns
4. Technology Integration and Data Management
Challenge: Often warehouses struggle with
- Multiple disconnected systems
- Manual data entry and reconciliation
- Lack of real-time information
- Integration issues between WMS and other tools
Solutions:
To overcome these technological hurdles
- Choose a WMS that offers standard APIs and integration capabilities
- Implement automated data collection through barcode/RFID scanning
- Use mobile devices for real-time data capture and validation
- Regular system audits and data cleanup procedures
- Invest in proper training for system users
- Partner with IT providers who understand warehouse operations
5. Order Fulfillment Accuracy
Challenge: Shipping errors lead to returns, customer dissatisfaction, and increased costs. Common issues include
- Picking the wrong items or quantities
- Missing order deadlines
- Incomplete verification procedures
- Poor packaging practices
Solutions:
WMS offer several features to improve accuracy, for example
- Implement pick-to-light or voice-picking systems
- Use mobile scanning devices to verify picks
- Set up quality control checkpoints
- Configure system-directed picking paths
- Use batch picking for improved efficiency
How to Choose the Right Warehouse Management System for Your Business
Here’s how to choose the right WMS that fits your unique requirements and budget.
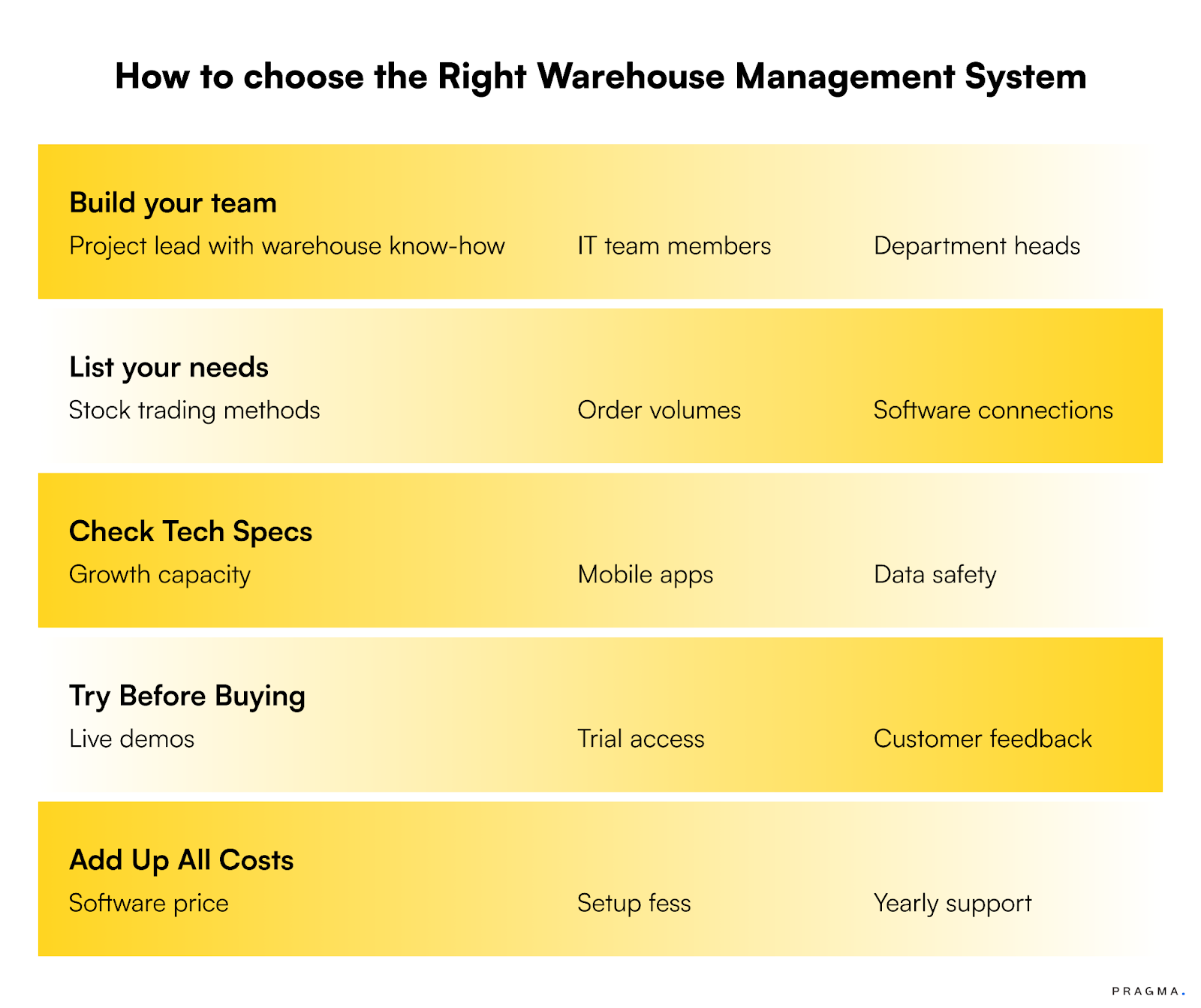
Form Your Selection Team
Start by building an internal team to lead the WMS selection process.
Consider Involving
- A project manager with warehouse operations knowledge
- Key stakeholders from different departments
- Management sponsor to support decision-making
- IT team members who understand your current systems
They will bring diverse perspectives and ensure all business needs are covered during selection.
PinPoint Your Requirements
Begin with an in-depth analysis of your existing warehouse operations.
Document
Inventory Management Needs
- Current inventory tracking methods
- Stock categorisation systems used
- Storage and retrieval processes
- Batch/lot tracking requirements
Order Processing Requirements
- Order volumes and patterns
- Picking and packing workflows
- Quality control procedures
- Shipping carrier integrations
System Integration Needs
Map out which existing systems your WMS needs to work with
- E-commerce platform
- Order management system
- Accounting software
- Shipping carriers
- Any automation equipment
Understanding these requirements will help you create a detailed evaluation checklist for comparing different WMS options.
Evaluate Technical Specifications
Focus on these key technical aspects
- Scalability: The WMS should handle increased order volumes and new sales channels without requiring replacement. Factor in your 3-5 year growth plans when evaluating system capabilities.
- Mobile Support: Check if the WMS offers mobile apps and handheld device support for warehouse people.
- Data Security: Review the security features
- Access control systems
- Data encryption methods
- Backup procedures
- Audit trail capabilities
- Request Demos and References: Don't rely solely on vendor presentations. Ask for
- Live system demonstrations
- Trial access when possible
- Customer references in your industry
- Site visits to see the WMS in action
Assess Total Cost of Ownership
Calculate all costs involved
Direct Costs
- Software licenses/subscriptions
- Implementation services
- Hardware requirements
- Team training
Ongoing Expenses
- Annual maintenance fees
- System upgrades
- Technical support
- Additional user licenses
Get detailed quotes from vendors and watch for hidden costs in the fine print.
Review Support Services
Examine the vendor's support offerings
- Support availability hours
- Response time guarantees
- Training programs
- Implementation assistance
Strong vendor support ensures smooth operations after implementation.
Modern Trends in Warehouse Management Systems
Here's what's shaping the future of WMS technology and how it can help your business grow.
AI and Machine Learning Integration
AI helps automate routine decisions and optimise warehouse operations in several ways
- Demand Planning: The system learns from your historical sales data, seasonal patterns, and market conditions to suggest optimal stock levels to prevent possible stockouts during peak seasons.
- Picking Optimisation: AI analyses order patterns and warehouse layouts to create the most efficient picking sequences for faster order processing.
- Equipment Maintenance: The system monitors your equipment performance and suggests preventive maintenance schedules based on actual usage patterns rather than fixed schedules.
Internet of Things (IoT) Applications
IoT devices give you real-time information about your warehouse operations
Environmental Monitoring Sensors track temperature, humidity, and other conditions.
It helps maintain product quality, especially for items like cosmetics or food products that need specific storage conditions.
Mobile-First Solutions
Mobile technology makes operations more flexible for your team through
- Voice-Directed Work: Staff can receive instructions through headsets while keeping their hands free for picking and packing.
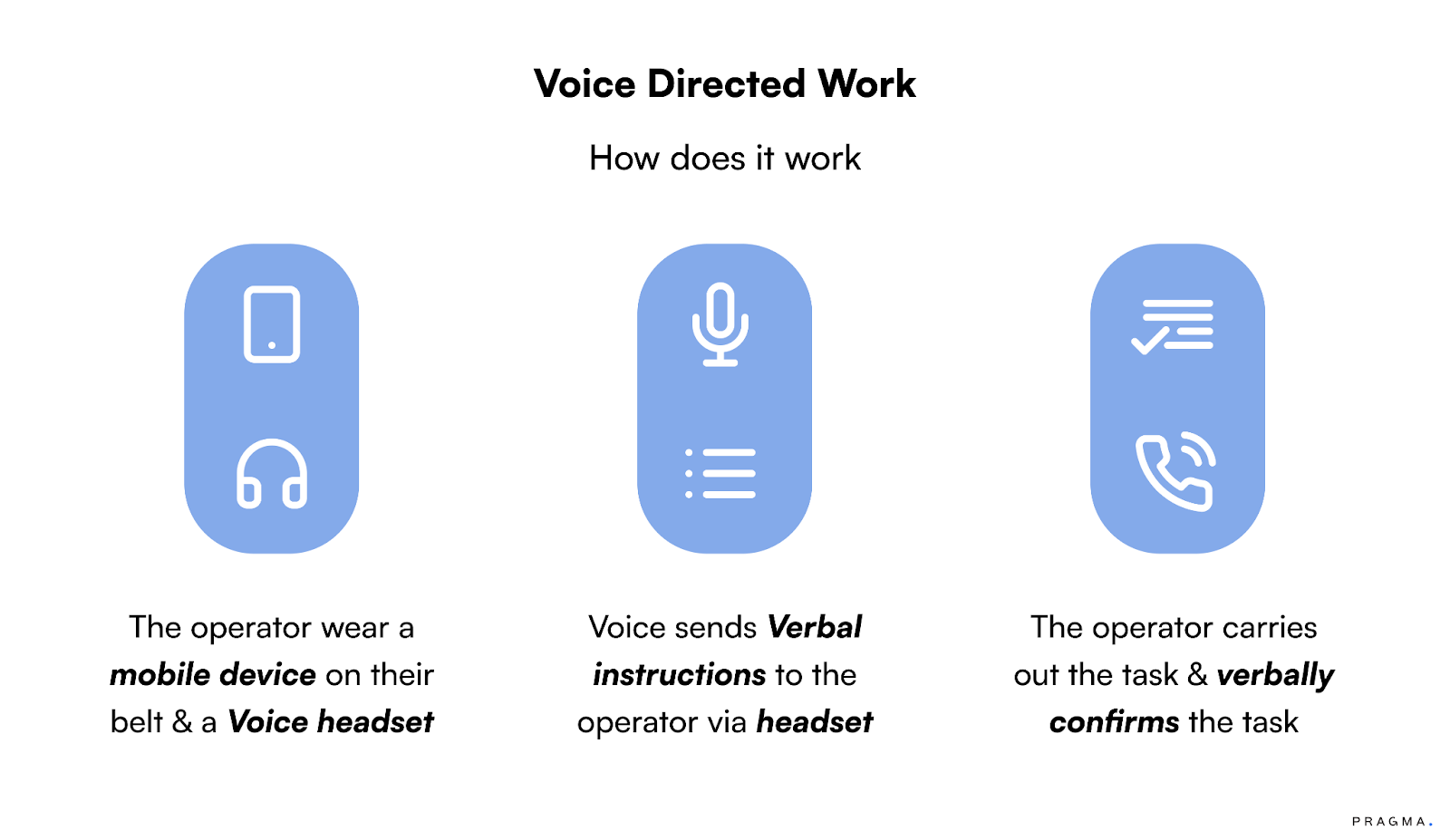
- Remote Access: Check inventory levels, view performance metrics, and manage operations from anywhere via mobile apps.
Automation Options
Physical automation helps scale operations efficiently:
Collaborative Systems Modern robots work alongside your staff to:
- Transport items between zones
- Support picking operations
- Help with repetitive packing tasks
The robots handle routine work while your team focuses on quality control and customer service.
Green Warehouse Features
Future systems will help control environmental impact while saving costs using
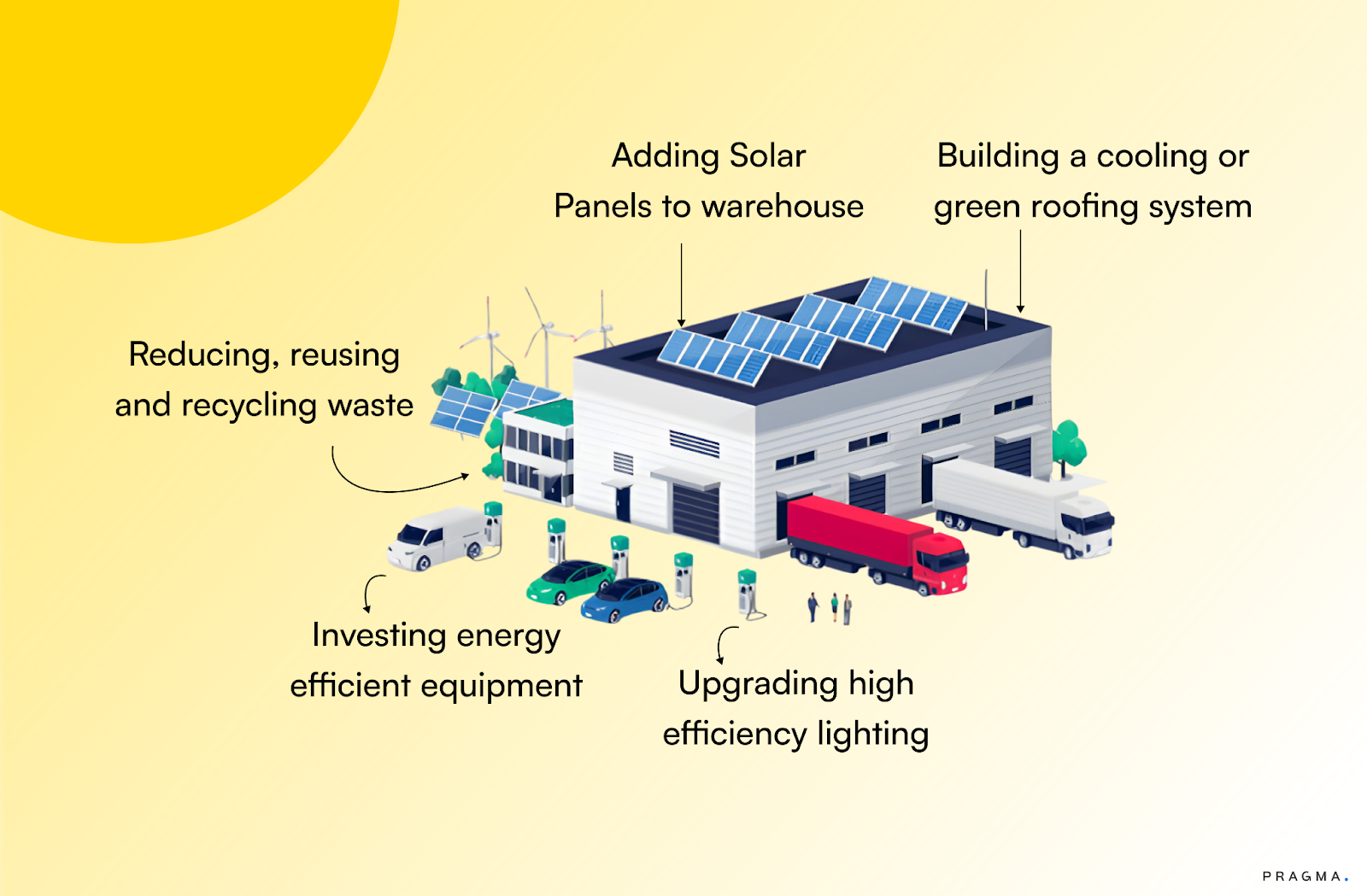
- Smart Controls: Automated lighting and temperature management lower power bills while maintaining proper storage conditions.
- Inventory Optimisation: Better stock management means less product wastage and careful use of space and resources.
Implementation Considerations for a Warehouse Management System
A successful WMS implementation requires the following considerations.
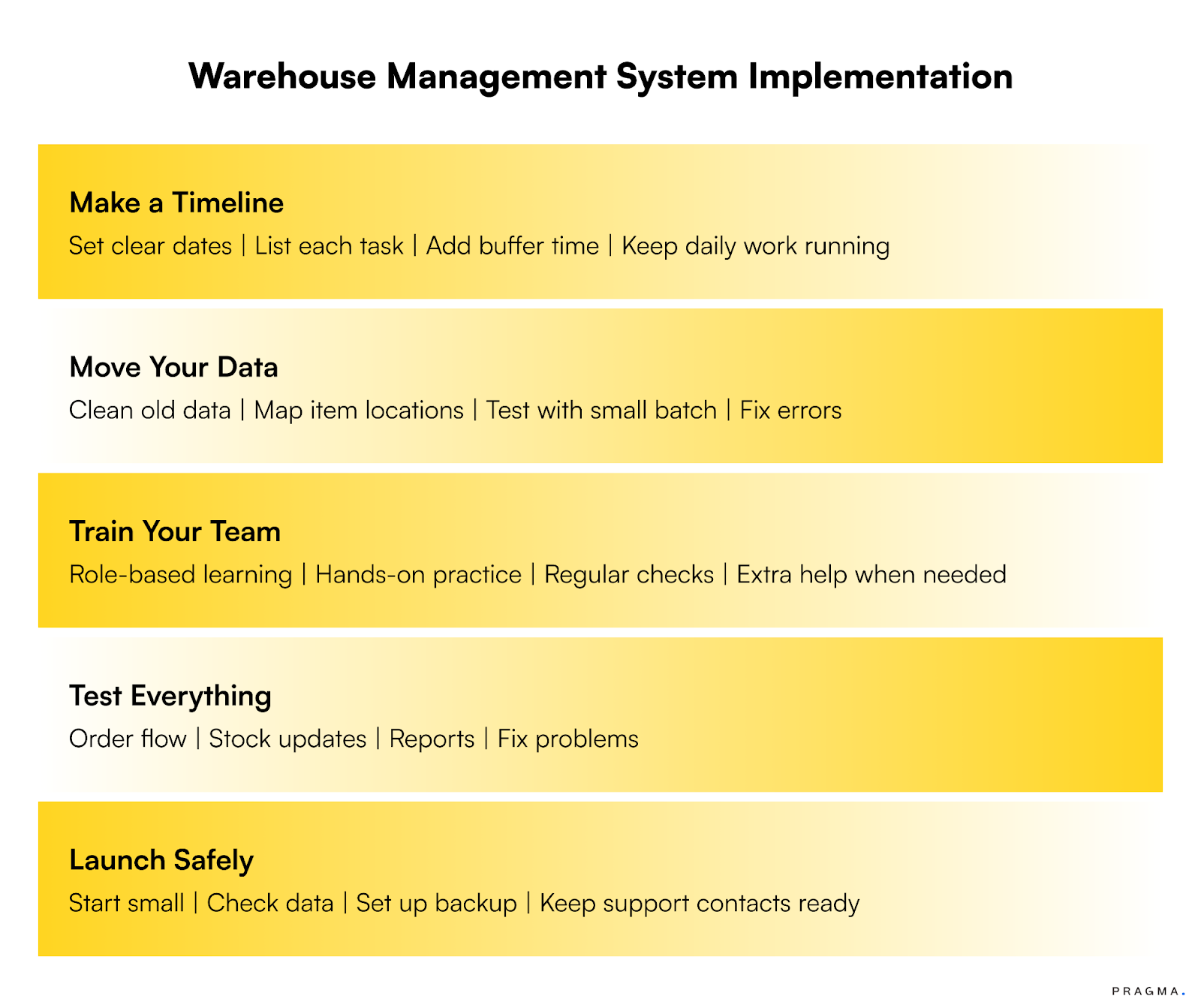
Project Planning and Timeline
Create a realistic implementation schedule that accounts for all necessary steps.
Your timeline should include system setup, data migration, testing, and staff training.
Allow extra time for unexpected issues and ensure the schedule doesn't disrupt your daily operations.
Work with your vendor to create detailed project milestones. Each milestone should have clear deliverables and success criteria, to help you track progress and identify potential delays early.
Data Migration Strategy
Start by reviewing your current data quality. Clean up any inconsistencies in product information, location assignments, and inventory records before migration.
Create a detailed map of how your existing data will transfer to the new system.
Test the migration process with a small data set first to identify and fix any issues before moving all your data.
Staff Training Program
Develop a comprehensive training plan for your team. Different staff members will need different levels of training based on their roles.
Warehouse operators need hands-on practice with scanning and picking processes, while supervisors need training on reporting and monitoring tools.
Include regular check-ins during the training period to identify areas where they need additional support.
System Testing
Set up a thorough testing process before going live. Test all major functions, such as
- Order processing from receipt to shipping
- Inventory movements and updates
- Integration with other systems
- Reporting and analytics
Document any issues found during testing and work with your vendor to resolve them.
Only move forward with implementation when all critical functions work correctly.
Go-Live Strategy
Plan your system launch carefully. Consider starting with a pilot phase in one area of your warehouse or with a subset of your inventory.
So you identify and fix issues without risking your entire operation.
Prepare a detailed go-live checklist that includes
- Final data verification
- System access setup
- Backup procedures
- Support contact information
- Emergency procedures
After launch, monitor system performance closely. Track key metrics to ensure the system meets your expectations and adjust configurations as needed.
To Wrap It Up
Whether you're starting with basic inventory tracking or building advanced automated operations, your warehouse management system should adapt and grow with your brand.
Focus on selecting and implementing a solution that balances your current needs with future scalability plans.
By following the frameworks and considerations outlined in this guide, you’ll be able to build warehouse operations that support consistent growth while maintaining accuracy and customer satisfaction.
The right WMS isn't just about managing inventory—it's about creating a long-lasting base for sustainable future expansion.
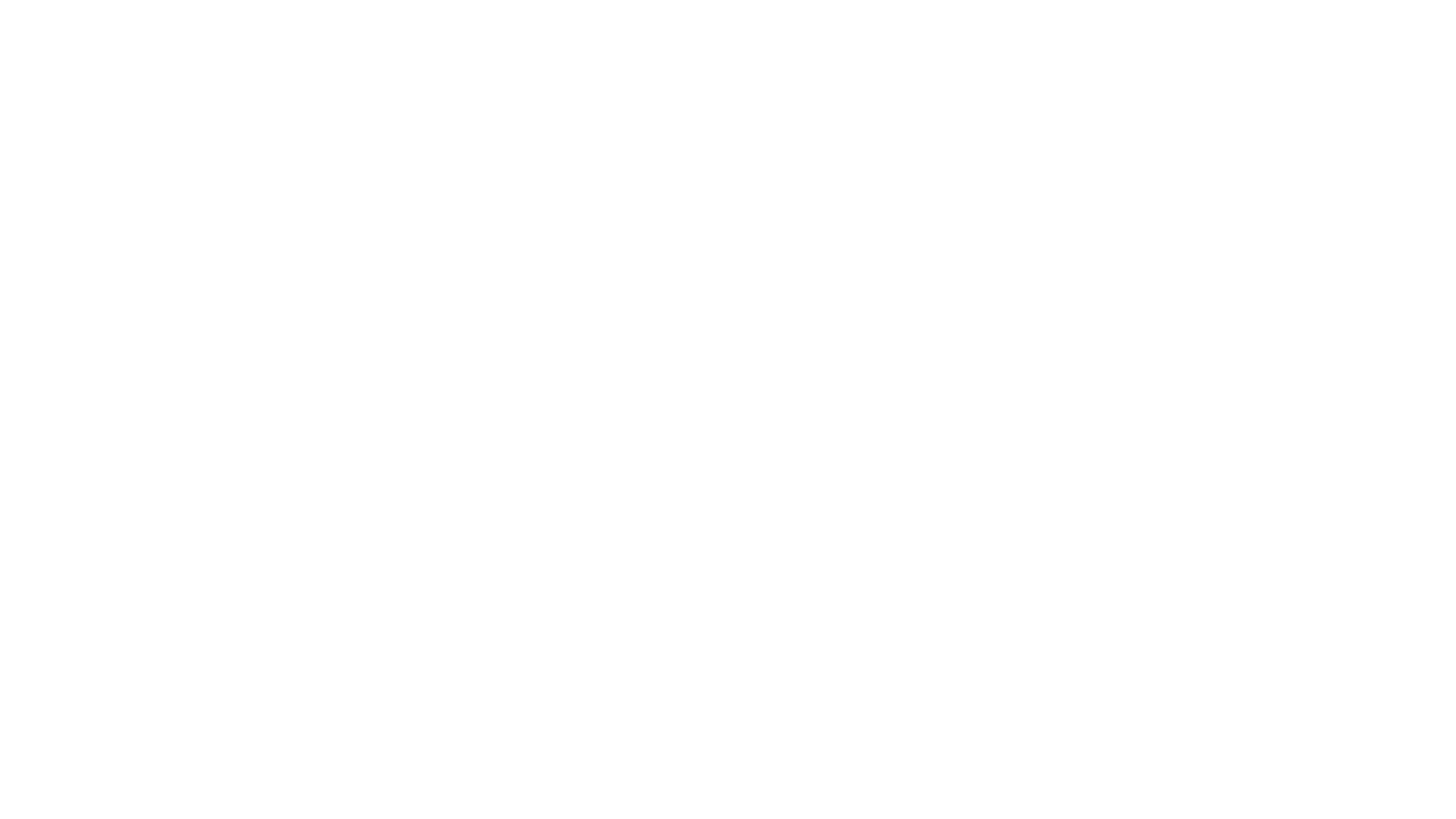
FAQs (Frequently Asked Questions On Warehouse Management System)
What is the function of WMS?
A warehouse management system (WMS) automates and controls daily warehouse operations—from receiving and storage to picking, packing, and shipping. It provides real-time inventory tracking, optimises space usage, and improves order fulfilment processes.
What are the key elements of WMS?
A WMS integrates five essential components: real-time inventory control and location tracking, intelligent order management, resource allocation for staff and equipment, automated documentation, and data analytics for performance insights.
Function of warehouse management system in logistics.
In e-commerce logistics, a WMS coordinates product movement through the supply chain by managing
- Inbound receiving and putaway
- Storage optimisation and inventory control
- Order picking and shipping workflows
- Resource allocation and scheduling
- Data collection for operational insights
Talk to our experts for a customised solution that can maximise your sales funnel
Book a demo