Inventory management is a cornerstone of any thriving business in the e-commerce space, irrespective of its scale or the product it sells. It involves tracking and maintaining a company's stock, which helps guarantee the timely availability of various products to fulfil the customers’ requirements.
Today, in this blog, we will talk about What is Inventory Management - its most important aspects, significance, various methods, techniques for better management, challenges, and much more. So, let’s get straight into the basics - What is inventory management?
What is inventory management?
What is inventory management is a general query that shows up across all types of e-commerce brands. Simply put,
“Inventory management is an important part of ensuring an effective supply chain, involving tracking goods from manufacturers to warehouses and then to the point of sale. The main goal is to ensure the right products are available in the right location at the right moment.”
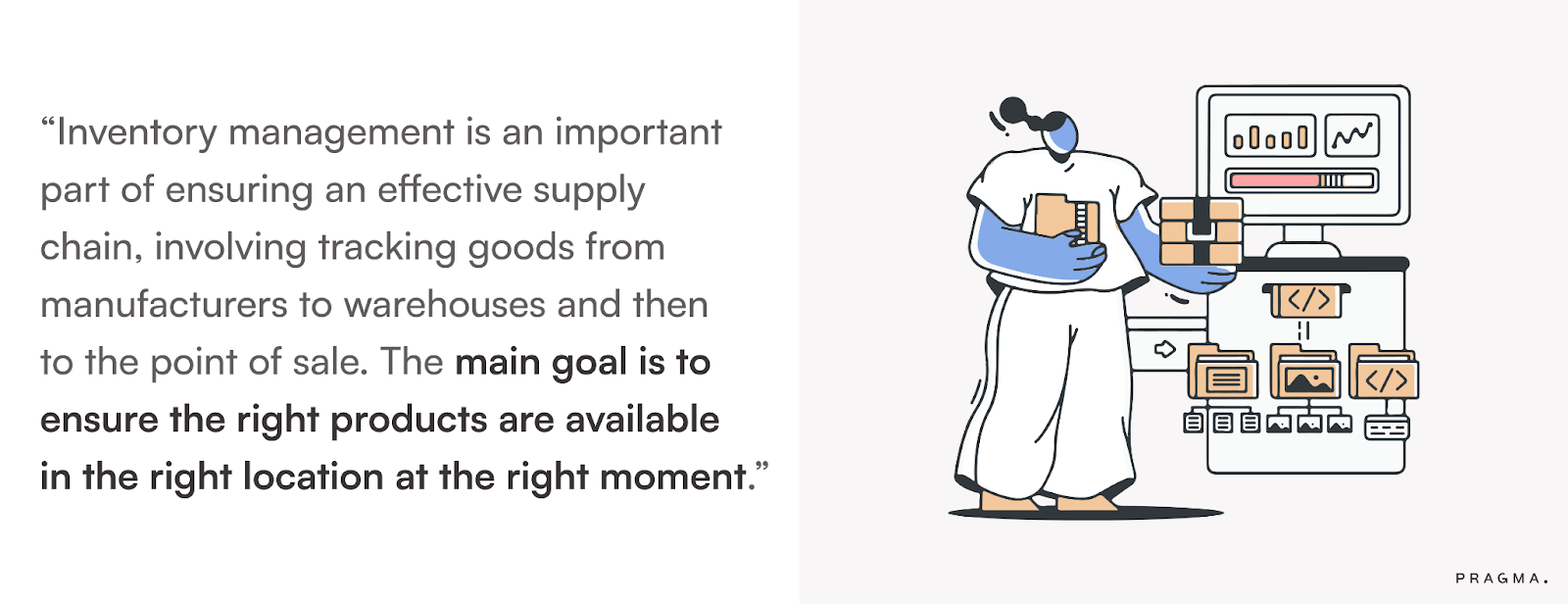
The Importance of Inventory Management
Now that we know “What is inventory management”, it’s time that we dive into the question: why should we invest in inventory management and why is inventory management important in the first place?
Inventory management is largely based on the fact of maintaining a balance between supply and demand and follows a flow like:
- To prevent stockout and overstock conditions - It ensures that brands have the right amount of stock to meet customer demand.
- It also helps in optimising cash flow by minimising the delivery costs for customer orders and excess holding costs.
- Helps identify buying trends and patterns that come in handy in peak seasons like the festive/holiday seasons, etc by making sure to fulfil customer demand.
- Finally, if all is done right, inventory management also seconds in maintaining a great brand and customer relationship by ensuring quick order delivery and fulfilment
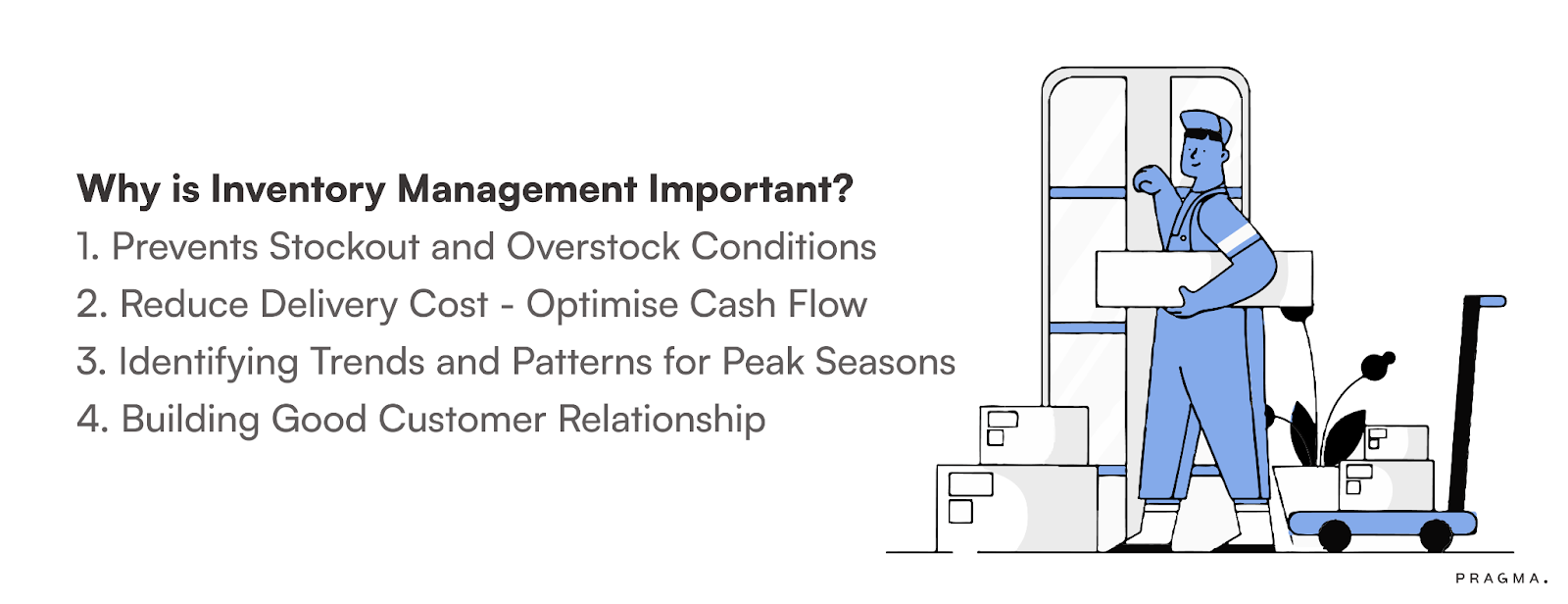
Benefits of Inventory Management
Efficient inventory management has the capability of transforming processes into seamless touchpoints that help in great results like:
- Proves to be cost-effective while reducing operational costs.
- Helps brands minimise overspending on warehouse storage.
- Optimise storage requirements.
- Helps in forecasting sales trends for various seasons like festive, holiday, etc to help the brand maintain adequate stocks.
Most importantly, Inventory management will help you build better customer satisfaction if performed in the right direction.
What are the types of inventory management?
Raw goods: Raw materials are the initial components utilised in manufacturing processes, typically acquired from various suppliers. These materials encompass substances like metal, plastic, fabric, and wood, essential for crafting finished goods.
Work-in-progress (WIP): Work-in-progress (WIP) denotes products in an intermediate stage of completion within the production pipeline. WIP accounts for costs such as labour, raw materials, and equipment, which are later integrated into the overall cost of goods.
Finished goods: Finished goods are fully completed products ready for sale and are held in stock for customer acquisition. Once a WIP reaches completion, it transitions into the inventory of finished goods.
Maintenance, repair, and operations goods (MRO): Maintenance, repair, and operations goods (MRO) encompass materials and equipment essential for production but not incorporated into the final product. Examples include personal protective gear, office supplies, and cleaning materials.
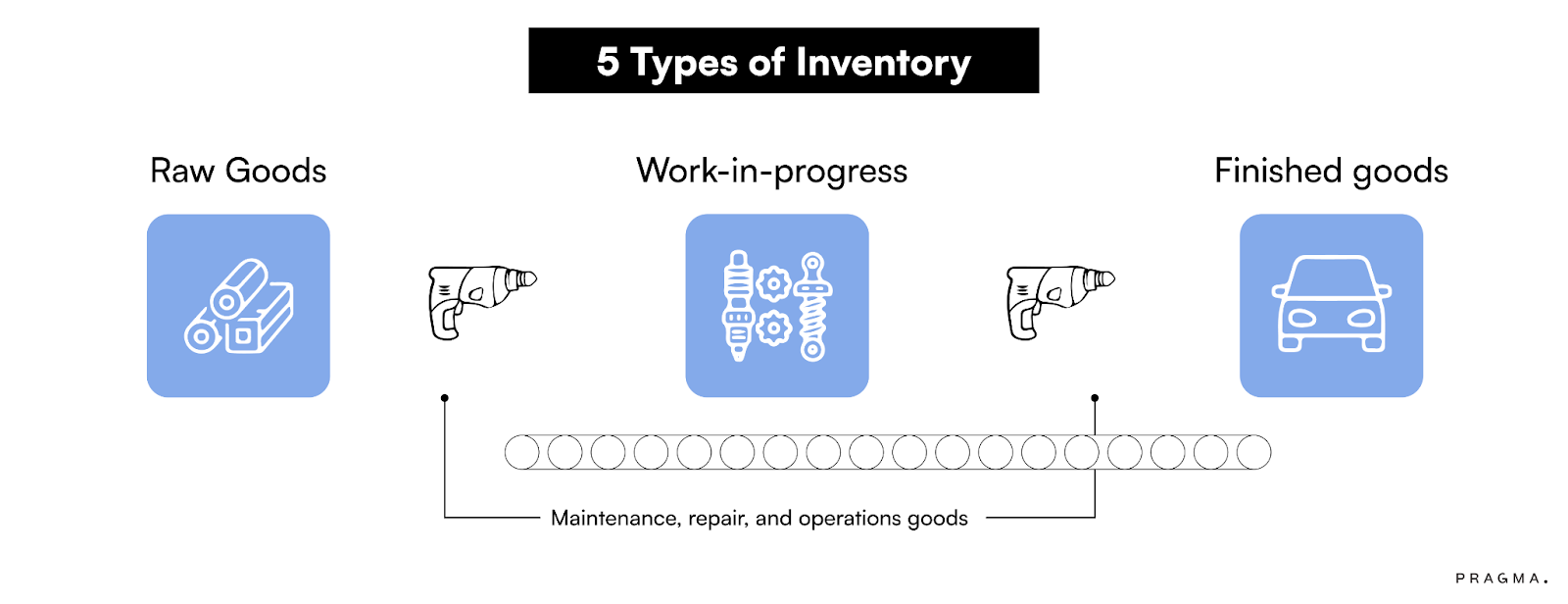
Additional inventory types may include safety stock, packaging materials, cycle inventory, service inventory, transit, theoretical, excess and maintenance, and decoupling inventory. These classifications vary across companies based on their specific inventory management systems.
How Inventory Management Works
Think of the various steps involved in Inventory Management as a system that builds the Supply Chain for your brand. If any step in this chain faces a delay or procurement challenge, your end goal of customer satisfaction will be at stake.
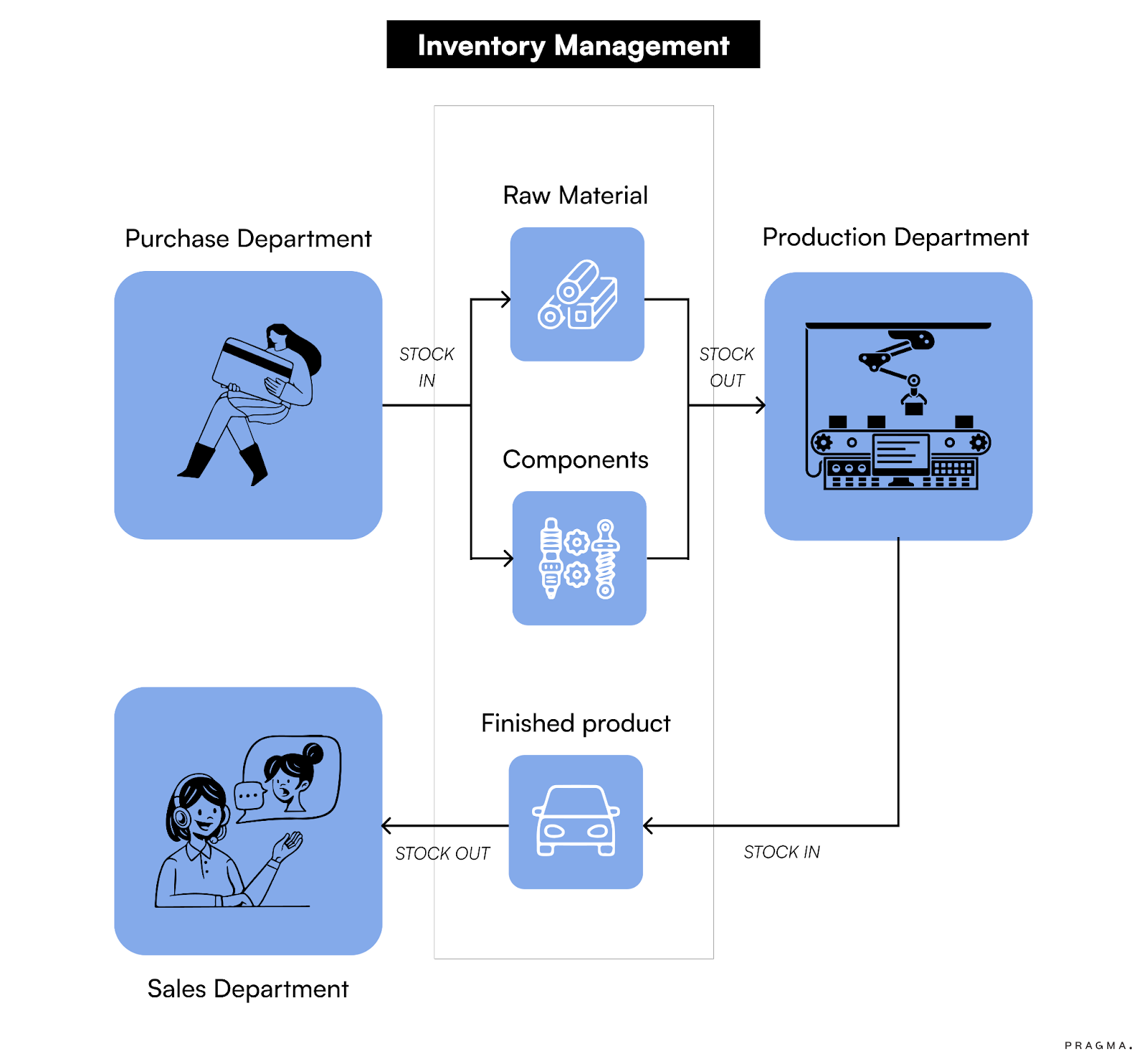
Hence, let us help you with the various yet important steps in Inventory management:
Receiving Manufactured Goods
The initial phase of inventory management begins with receiving the goods from the supplier. This is the first step in your supply chain to operate seamlessly. Upon the arrival of the order, the primary task is to inspect the received products. It is important to verify things such as:
- Product quantity
- Codes, and serial numbers
- Manufacturing dates for perishable items, etc.
Location Distribution - Intelligent Stocking
Following product inspection, the next step is to map these items into your warehouse and record them in your inventory management system.
They provide real-time visibility into stock levels, enabling businesses to make informed decisions regarding stock replenishment, storage allocation, and order fulfilment.
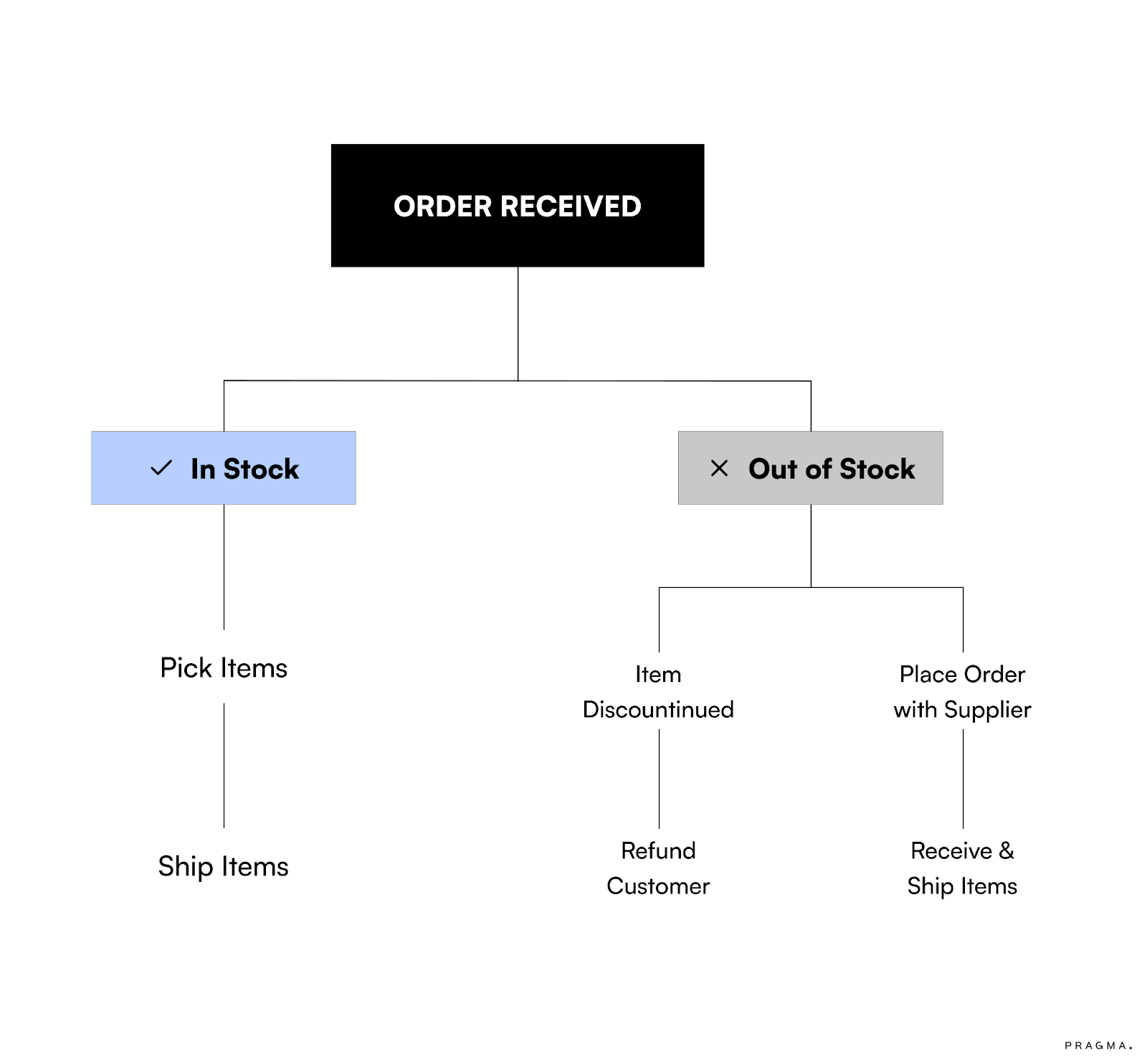
It even assists in designing and managing the layout of a warehouse, optimising space utilisation, and minimising travel times for workers. It also helps with slotting, which involves assigning optimal storage locations to products.
Also, prioritising accessibility by minimising distances to top-selling items enhances efficiency, meaning they are present in warehouses in areas where they are ordered more.
Logistics - Order Fulfilment and tracking
Finally, the last step of the order fulfilment process starts by optimising order picking, packing, and shipping. Let’s understand the major features of fulfilling a customer’s order:
- Real-time Monitoring: A Warehouse Management System (WMS) includes algorithms for efficient order routing and batch picking, resulting in reduced order processing times and improved order accuracy.
- Reporting and Analytics: Brands typically need robust reporting and analytics tools that allow businesses to monitor KPIs. A WMS provides this data-driven approach to help identify areas for improvement and supports strategic decision-making.
- Automated Triggers: The best part about an intelligent Inventory Monitoring System is that it can help you set triggers at every step.
Think about when you would want your warehouse to be restocked.
Ideally, this will happen when you are left with half of the inventory of a particular product or maybe 35%, right?
With Pragma’s Return Management System, you can set triggers that inform your warehouse about lower product stocks. This way your team can take appropriate action of filling the stock again before it replenishes - Think of it as ALERTS!
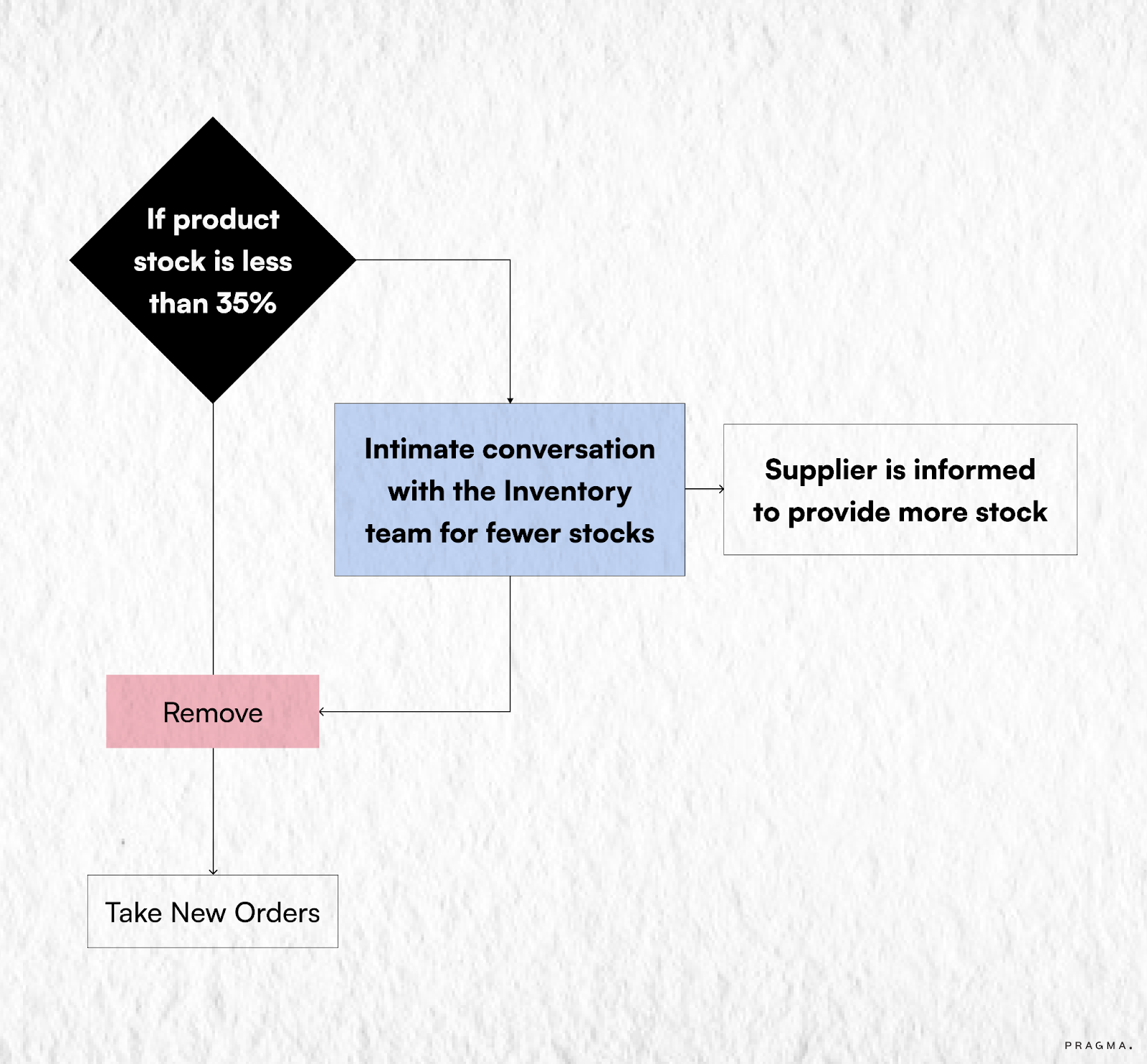
- Bulk Order: What if a customer wants 6 items of a funky shirt, but you have only 4? Will you simply not take their order? Ideally NO!
A smart warehouse management system will immediately look for the product’s stock in nearby warehouses to fulfil the user demand. This way it helps you build a better customer lifetime value.
The future of inventory management
Technological advancements have seen their involvement in almost every industry, right from medical science to automobiles, and now to Inventory Management.
Return Management Systems like Pragma are building themselves to gain deep insights that help in enhancing supply chain performance, optimising costs and performance, and building towards automation can offer substantial scalability advantages.
Some technological advancements present in Pragma’s RMS are:
- Intelligent order management systems that provide advanced analytics and automation to streamline order processing, inventory allocation, and fulfilment.
- Utilising Internet of Things (IoT) data from sensors that will furnish real-time information on inventory location and condition.
- Facilitating connectivity among various parties by establishing a unified and tamper-proof ledger of all transactions using Blockchain technology.
- Involving AI-driven predictive analytics approach that analyses vast datasets and helps in forecasting demand that helps brands optimise replenishment strategies, and automate various inventory-related tasks, mainly during peak seasons
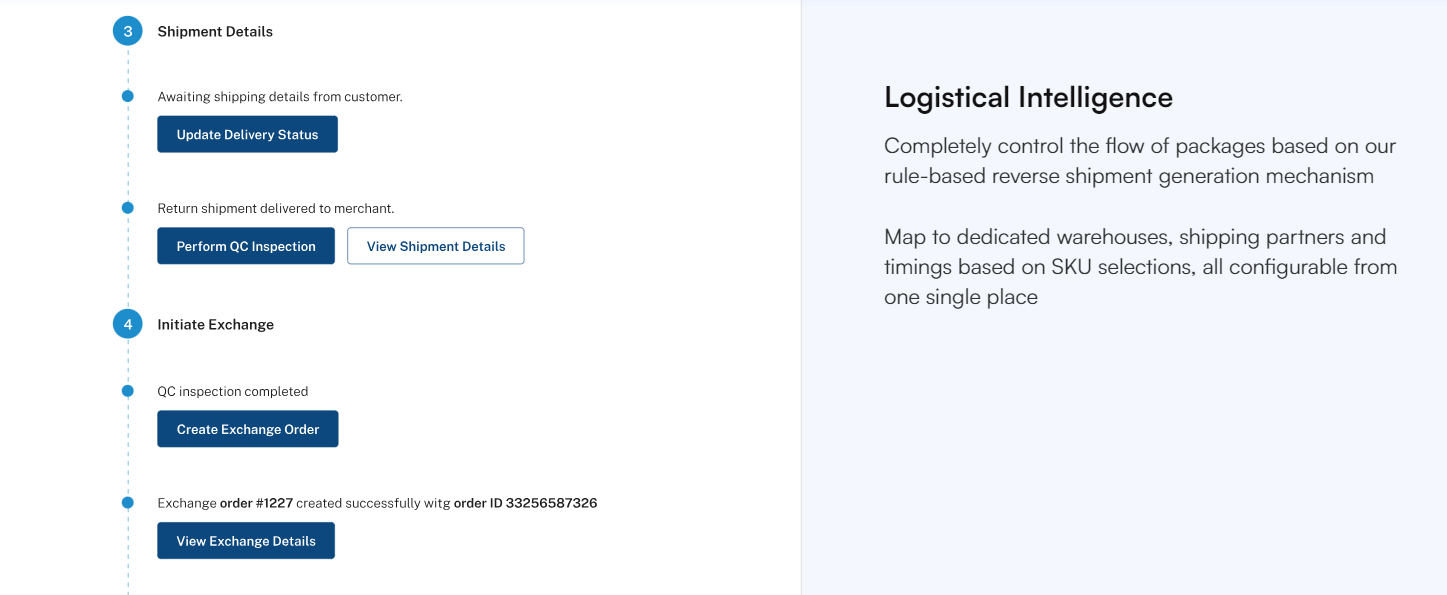
These systems dynamically adjust inventory allocation based on demand, inventory levels, and customer preferences.
How to Choose an Inventory Management System?
When deciding on an Inventory Management System for returns management, consider the following factors:
- Business Size
- Integration
- Budget
- Customer Experience
- Data Insights
We’re analysing millions of return orders. Right from cosmetic brands to apparel, but one thing we recognised is that a product that gets a 5-star rating from a customer might get a 1-star rating from another.
With that being said, it even becomes important for you to maintain an inventory that can identify and solve any unexpected query like stockouts, overstocks, or maybe flag inappropriate users, or return queries that might be fraudulent in nature. Trust us, you can’t manually do this process as once your platform scales and you’re getting hundreds of return requests each day, it’s tough.
With this, we’re towards the end of this exhaustive guide that explains everything about what features you should consider while opting for an RMS for your platform.
With Pragma leading the race in terms of
- Access to Live data to build strategies on the go
- One-click return/exchange request for users
- Perform QC, Generate payment links in a single place
- Flagging of risky users during order placement/return
- 100% support during onboarding, setup and any time after
It’s time for you to try out Pragma and help you increase your revenue and reduce return order rates.
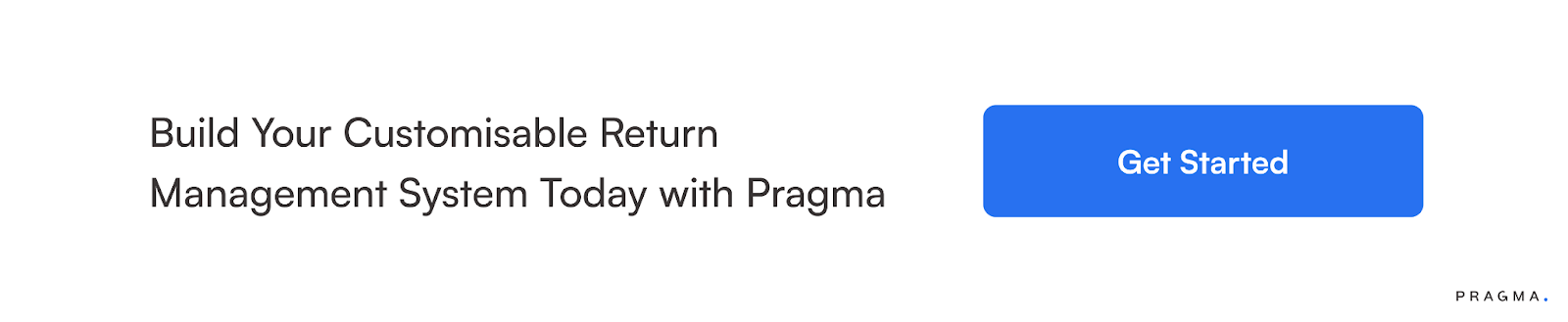
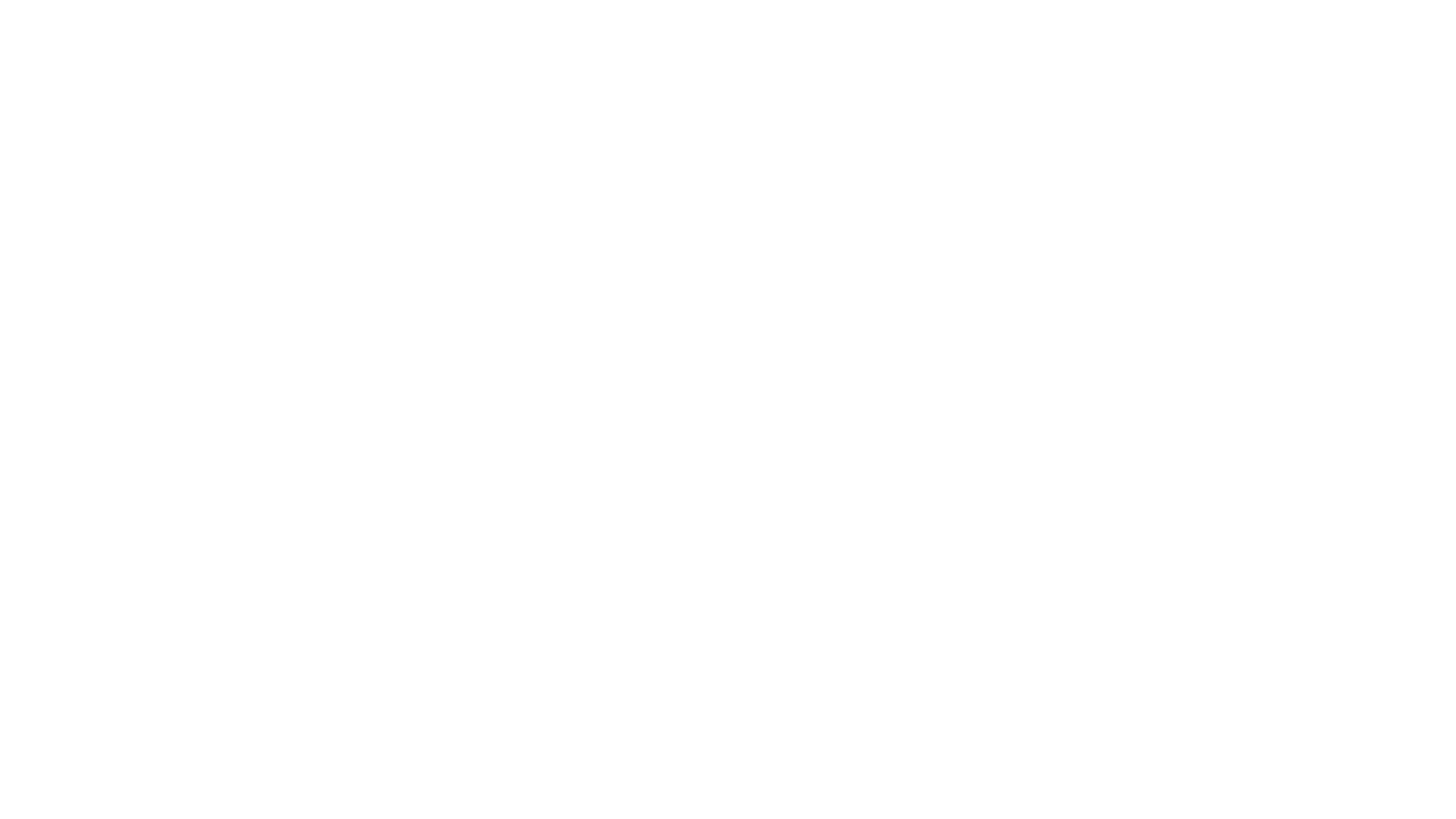
Talk to our experts for a customised solution that can maximise your sales funnel
Book a demo