Running an e-commerce or D2C brand in India means you're constantly balancing inventory decisions that affect your cash flow, operations, and customer satisfaction.
As online sales channels multiply and customer expectations evolve, simple stock tracking no longer suffices.
The question isn't just about what inventory control is—it's about building systems that help you
- Make data-backed purchasing decisions based on real demand patterns
- Reduce working capital blockage without risking stockouts
- Maintain consistent delivery promises across sales channels
- Scale operations efficiently as your brand grows
For brands selling through marketplaces, social commerce, and their websites, poor inventory management often leads to problems like overselling, delayed shipments, and wasted warehouse space.
Getting it right means understanding both the fundamentals and methods discussed in this guide.
So let's start by examining why proper inventory control matters and how it impacts different aspects of your operations.
Introduction to Inventory Control
Inventory control is the complete system of managing stock—from receiving products to storing them and finally delivering them to customers.
For E-commerce businesses, it involves understanding seasonal demands, managing multiple SKUs, and ensuring you never disappoint customers with "out of stock" messages without overstocking products.
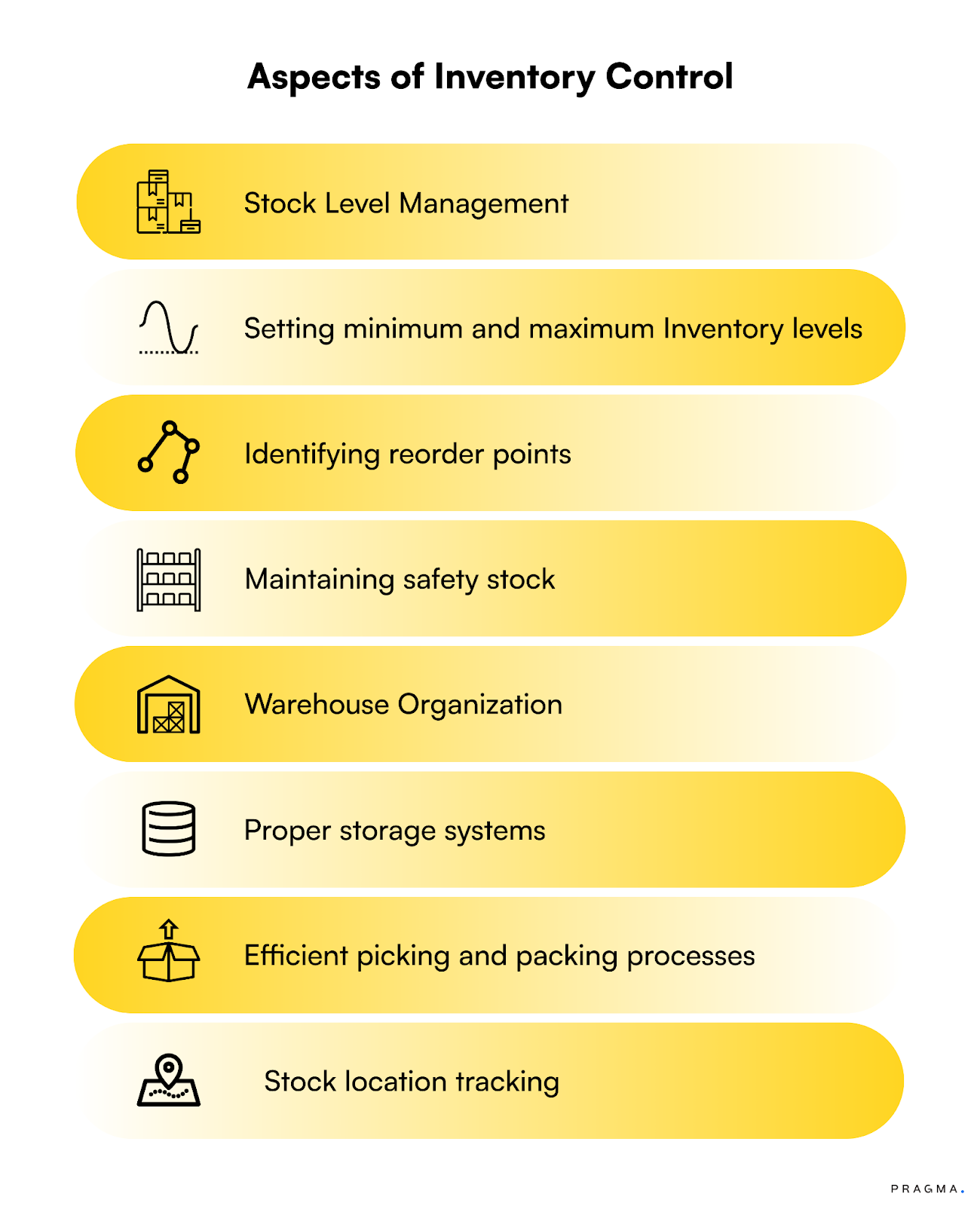
Consider a fashion D2C brand selling both seasonal and evergreen products…
Their inventory control system needs to account for
- Fast-moving basic items like black t-shirts that need constant replenishment
- Seasonal products like winter wear require different stocking strategies
- Limited edition items that need careful stock allocation
While traditional methods rely on manual counting and paper records, contemporary systems use
Software Solutions: These help track stock movements automatically and generate real-time reports.
Automated Reordering: Systems that trigger purchase orders when the stock reaches predetermined levels.
Data Analytics: Tools that analyse sales patterns and help predict future inventory needs.
For small and medium brands, inventory control might start with basic spreadsheets but should evolve as the business grows. So choose a system that
- Match your business scale
- Integrate with your existing platforms
- Provide room for growth
- Offer local support and understanding
Why Inventory Control Matters in Business Operations
Here’s how inventory control impacts different aspects of your business
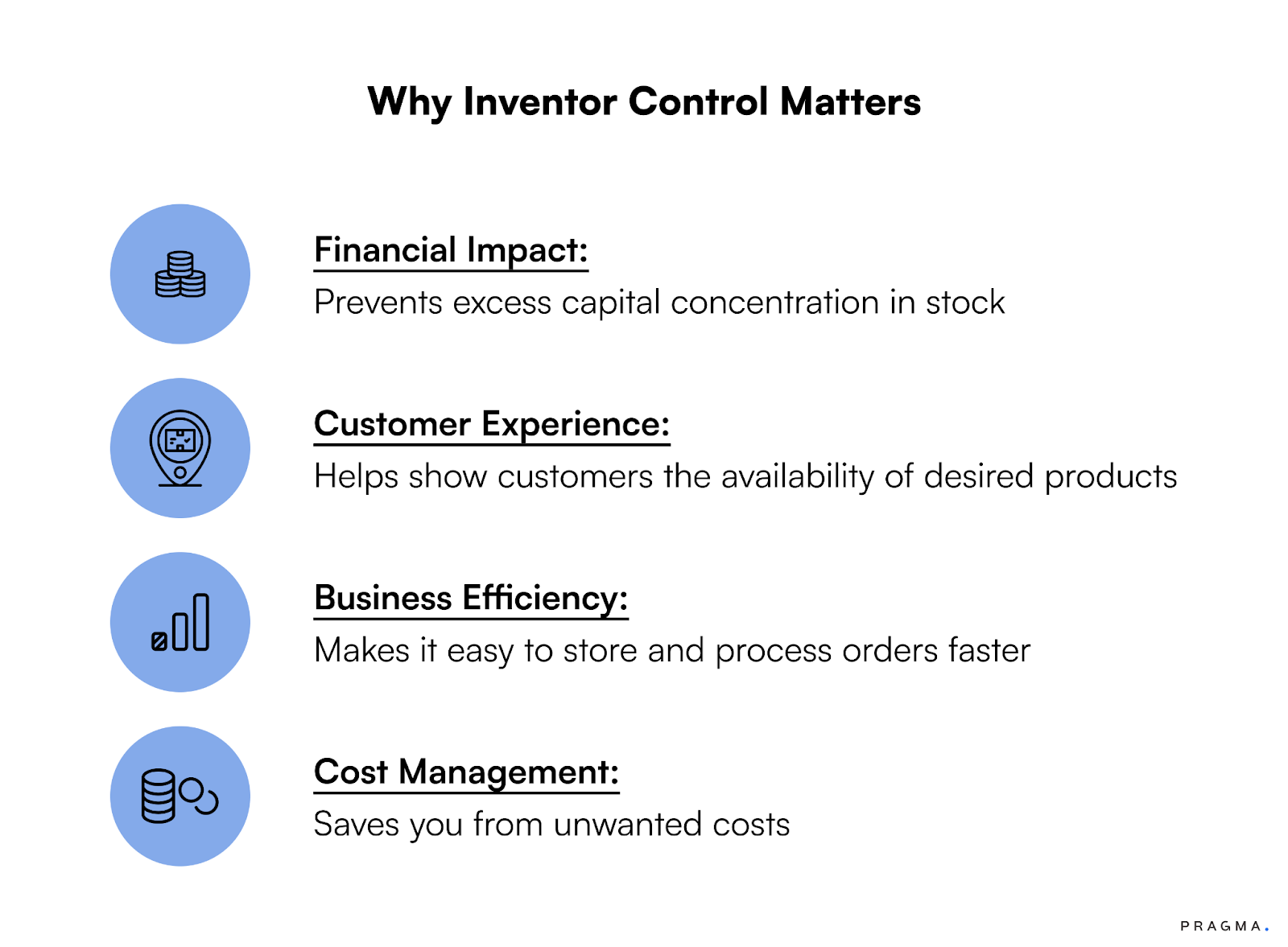
Financial Impact
Poor inventory management often leads to tied-up capital in excess stock or lost sales from stockouts. Good inventory control helps you
- Reduce storage costs
- Free up working capital
- Lower insurance expenses
Customer Experience
Your inventory control system affects how quickly and reliably you can fulfil customer orders. With proper controls in place, you can
- Maintain consistent delivery times
- Avoid order cancellations
- Build customer trust through reliable service
- Handle returns efficiently
Business Efficiency
Well-managed inventory speeds up your daily operations by
- Reducing time spent on stock counts
- Minimising errors in order fulfilment
- Improving warehouse space utilisation
- Supporting accurate demand forecasting
Cost Management
To save you from unnecessary costs such as
- Product damage or obsolescence
- Emergency shipping fees
- Labour costs for handling excess stock
Inventory Control vs. Inventory Management: Key Differences
While these terms are often used interchangeably, they serve different purposes in e-commerce.
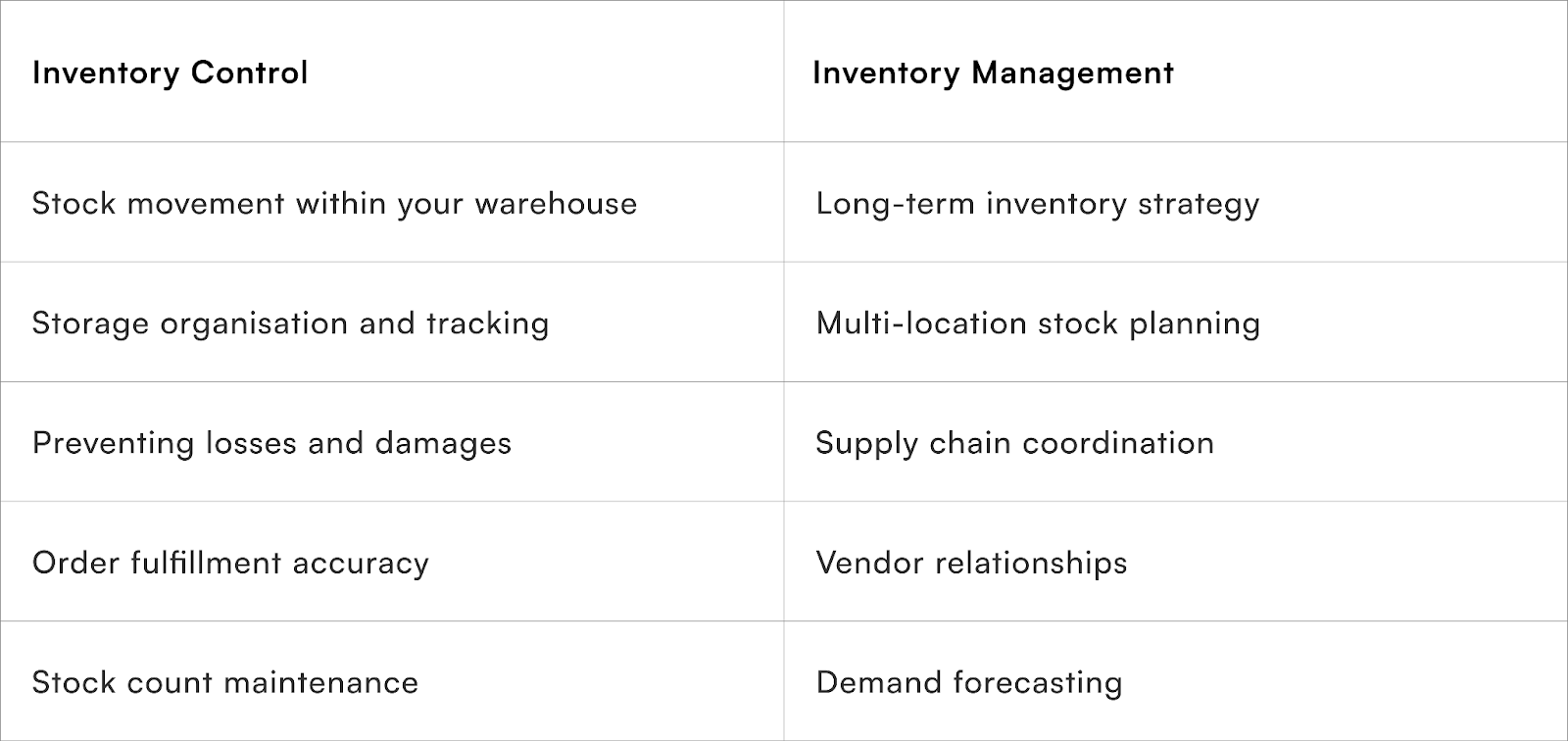
Let's examine a practical example.
Suppose an apparel D2C brand manages three warehouses.
Their inventory control system handles day-to-day operations like
- Recording incoming stock
- Managing warehouse space
- Tracking product movement
- Maintaining stock accuracy
Meanwhile, their inventory management system handles broader decisions like
- Planning seasonal collections
- Coordinating with manufacturers
- Allocating stock across warehouses
- Setting stock levels based on sales data
The distinction becomes clear in daily operations
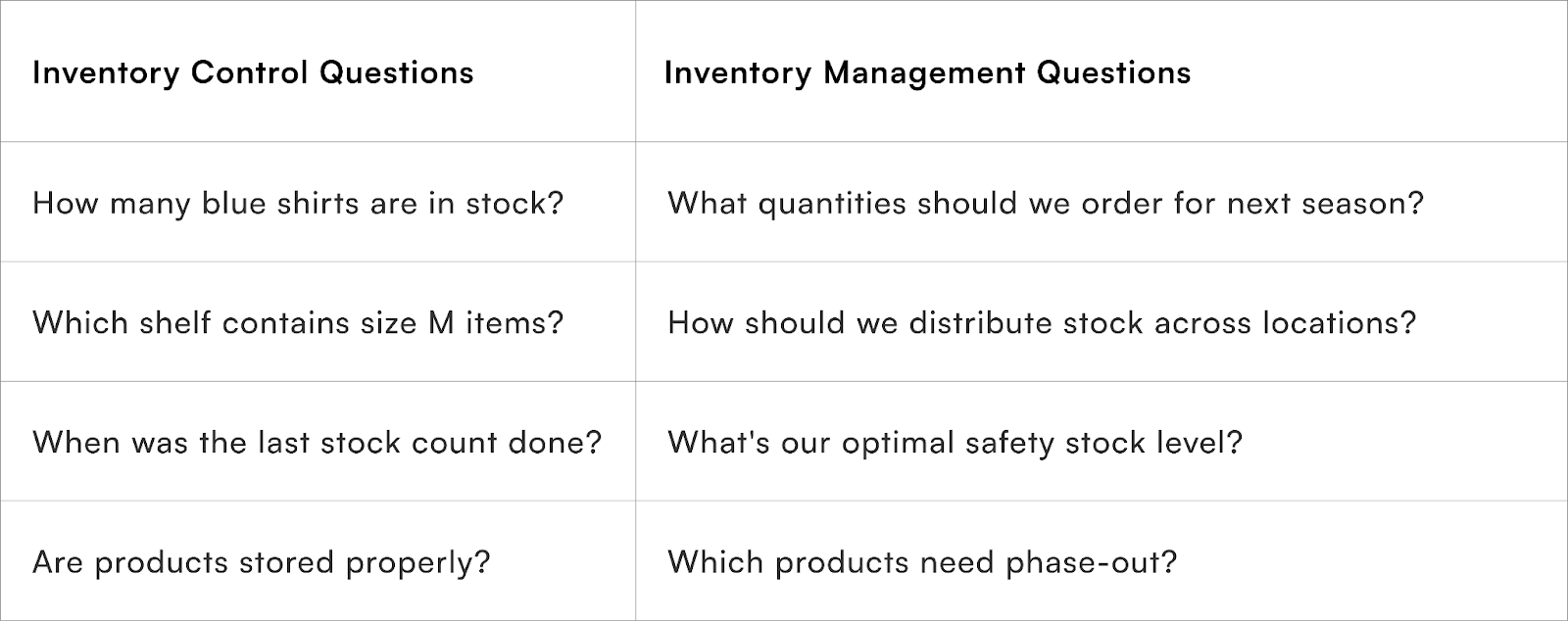
Technological Components
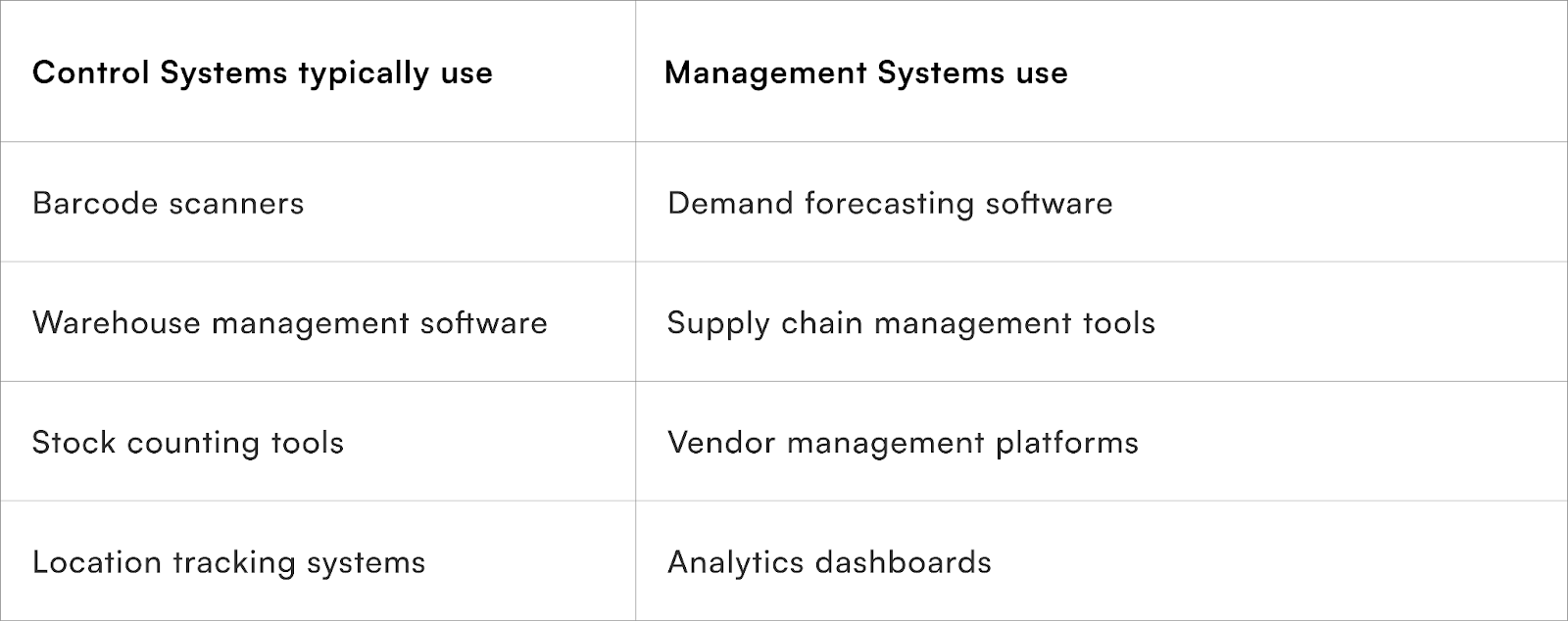
For D2C brands, especially those selling on multiple marketplaces, both systems need to work together in harmony, so you can
- Maintain accurate marketplace listings
- Prevent overselling across platforms
- Optimise storage costs
- Improve cash flow management
Objectives of Inventory Control
Five areas where inventory controls play an important role.
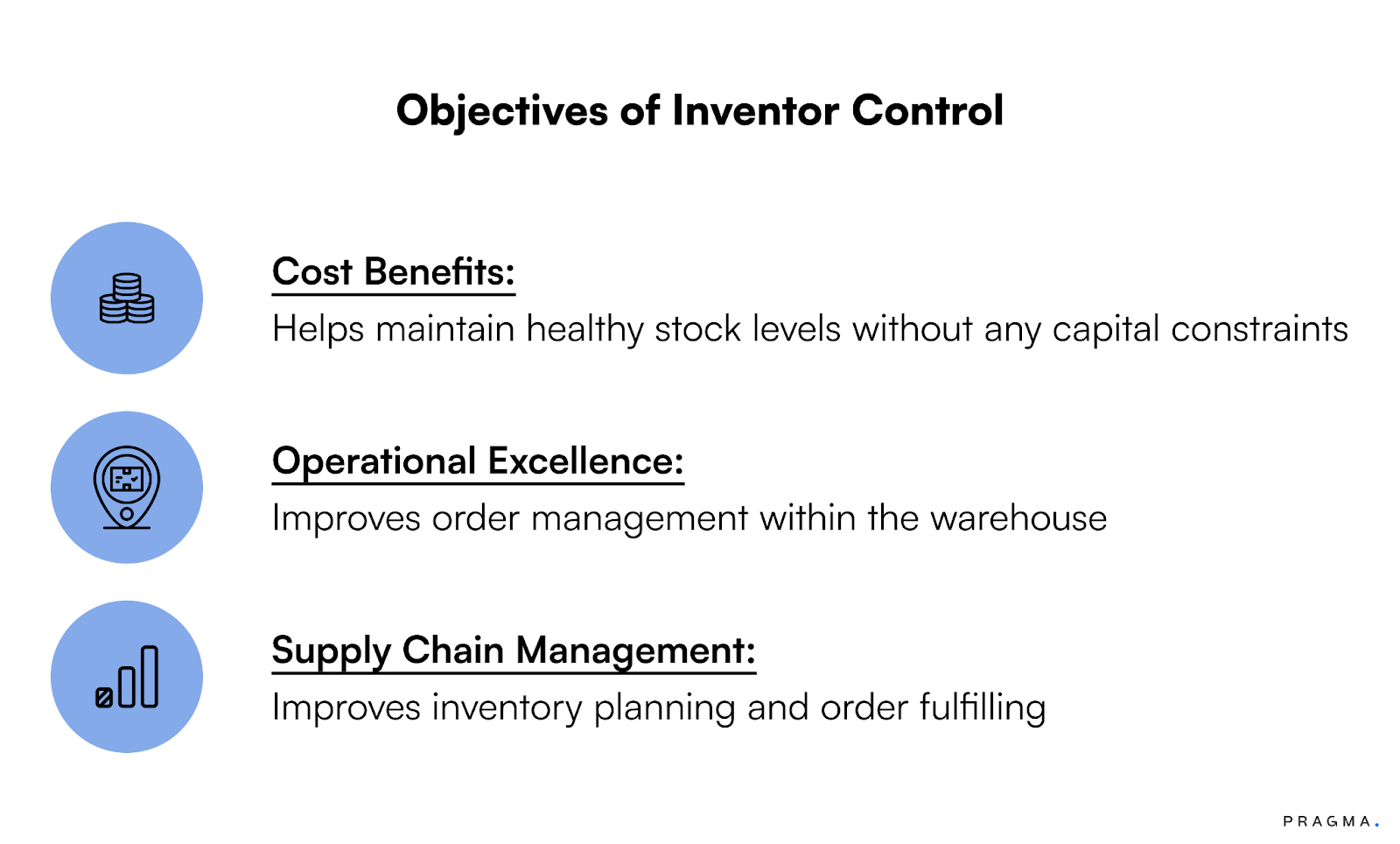
Cost Benefits
When implemented properly, inventory control significantly impacts your bottom line through multiple channels.
Excess inventory ties up working capital that could be better used for business growth, marketing, or product development.
By maintaining optimal stock levels, you free up this capital, ensuring you don't miss sales opportunities.
Storage costs form a substantial part of operational expenses for most D2C brands, such as
- Optimising warehouse space usage
- Reducing insurance costs for stored goods
- Minimising product handling requirements
- Lowering the risk of obsolescence
Operational Excellence
Proper inventory control helps your team know exactly what's in stock and where it's located, so they can process orders faster and more accurately.
With this level of visibility in inventory your
- Staff spend less time searching for products or correcting errors which shortens picking and packing times, more accurate fulfilment, and lower return rates due to wrong item shipments.
- Customers find the products they want consistently available and are more likely to return for future purchases.
- Order processing times go up which helps you achieve consistent delivery schedules, better handling of seasonal demand, and accurate product availability information on your website.
Supply Chain Management
By analysing stock movement patterns, you can
- Make informed decisions about supplier relationships
- Plan deliveries more effectively
- Negotiate better terms based on actual usage data
- Manage seasonal variations proactively
- Offer better prices to customers
- Maintain better profit margins
- Respond faster to market changes
- Scale operations more effectively
- Timely identification of damaged goods
Importance of Inventory Control
Three aspects where inventory control’s importance is the most impactful.
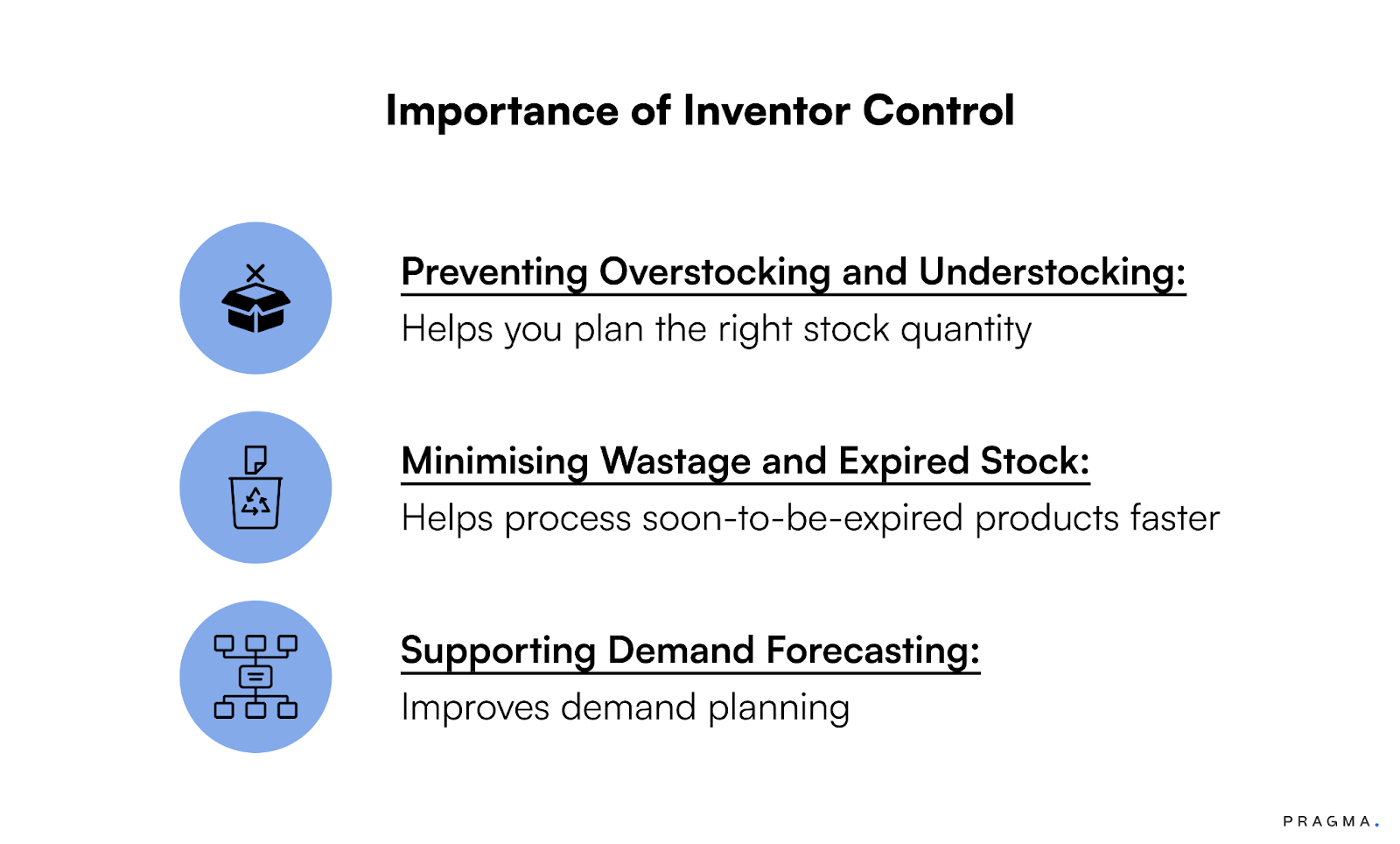
Preventing Overstocking and Understocking
Overstocking locks up working capital and increases holding costs, while understocking leads to missed sales opportunities and disappointed customers.
Start with understanding your demand patterns and supply chain realities.
When you stock too much inventory, you face increased warehousing costs and risk product obsolescence. This especially affects fashion and seasonal items, where trends change quickly.
Excess stock also occupies warehouse space that could store faster-moving products.
Understocking poses different challenges. Beyond lost sales, it can damage your brand reputation when customers find products out of stock repeatedly.
For D2C brands to build customer loyalty, consistent product availability is important for long-term retention. Running out of stock might push customers to try competitor brands, making it harder to win them back.
Proper inventory management helps prevent both scenarios.
- Data-driven order quantities based on sales velocity and seasonality
- Regular monitoring of stock levels against preset thresholds
- Automated reorder triggers when inventory reaches minimum levels
- Buffer stock calculations that account for lead times and demand variations
Minimising Wastage and Expired Stock
Product wastage directly impacts your bottom line, specifically for items with expiration dates or seasonal relevance.
More than just tracking expiry dates—it involves understanding product lifecycles and implementing systems to manage stock rotation effectively.
For perishable goods and beauty products, proper storage conditions and stock rotation prevent spoilage.
First-In-First-Out (FIFO) or First-Expired-First-Out (FEFO) methods ensure older stock moves out before newer inventory, especially when dealing with multiple warehouse locations or fulfilment centres.
Stock obsolescence often occurs due to,
- Poor demand forecasting leading to excess purchases
- Changes in customer preferences or market trends
- Product improvements or new versions making the older stock less desirable
- Seasonal items not sold within their prime selling window
Regular monitoring will help you identify slow-moving items before they become outdated.
So you can take timely action through promotional activities or inventory redistribution across locations with higher demand. For seasonal items, planning markdown schedules will help clear stock and recover some value.
Supporting Demand Forecasting
Accurate demand forecasting requires quality inventory data. Analysing historical sales patterns, seasonal trends, and stock movement will help you predict future demand more accurately.
And this information will guide your purchasing decisions and help optimise stock levels across different product categories.
You need to consider multiple factors when forecasting demand
- Sales history and growth trends
- Seasonal variations in demand
- Marketing campaign impacts
- Product lifecycle stages
- Competition and market changes
- Sales velocity for different products and categories
- Order frequencies and quantities
- Stock turnover rates
- Return rates and reasons
Types of Inventory Control Systems
Four main types of inventory control systems and their applications.
Periodic Inventory System
Involves checking stock levels at fixed intervals—weekly, monthly, or quarterly.
It is simple to implement and works better for smaller businesses with a specific number of SKUs.
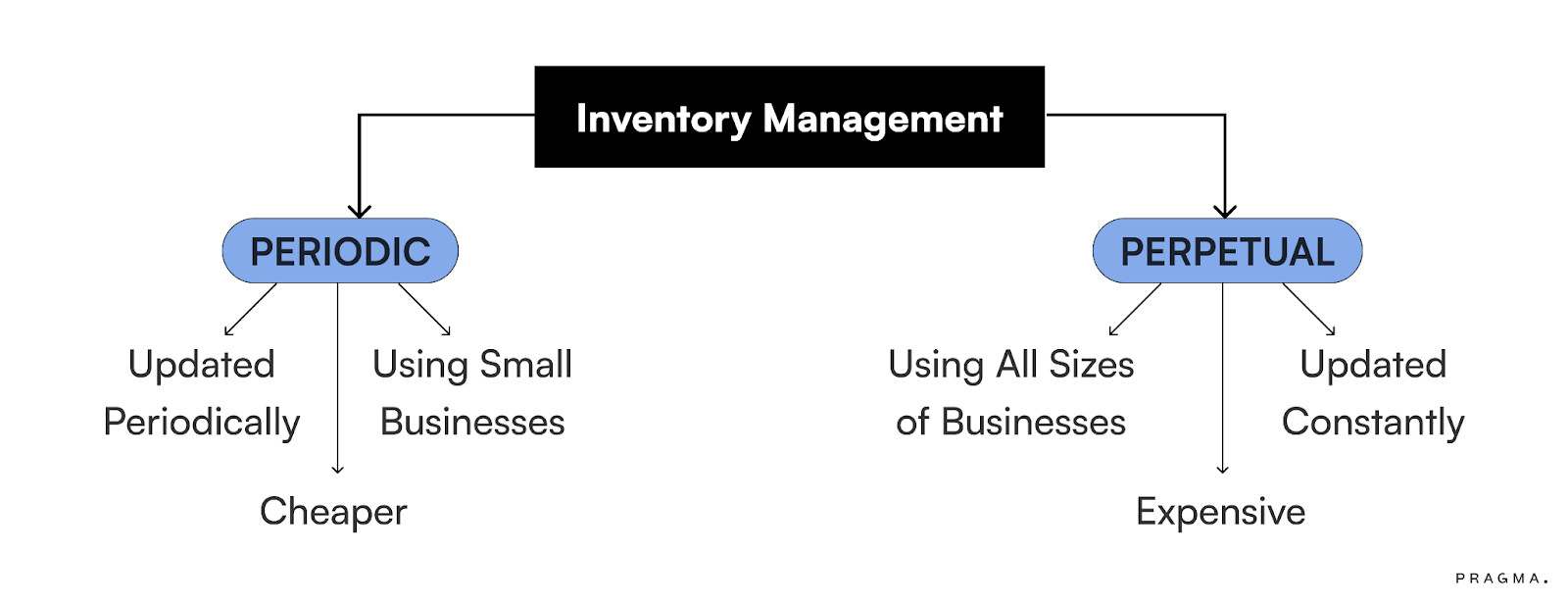
The process involves
- Regular physical counts of available stock
- Comparing actual stock with recorded numbers
- Adjusting records to match physical count
- Placing orders based on the latest count
For example, if you run a small accessories brand with 50-100 SKUs, periodic inventory checks might suffice.
However, as your product range grows, this system becomes less practical due to time constraints and potential errors.
Perpetual Inventory System
Tracks inventory in real-time using software and automation. Each sale, return, or stock movement updates your inventory records automatically.
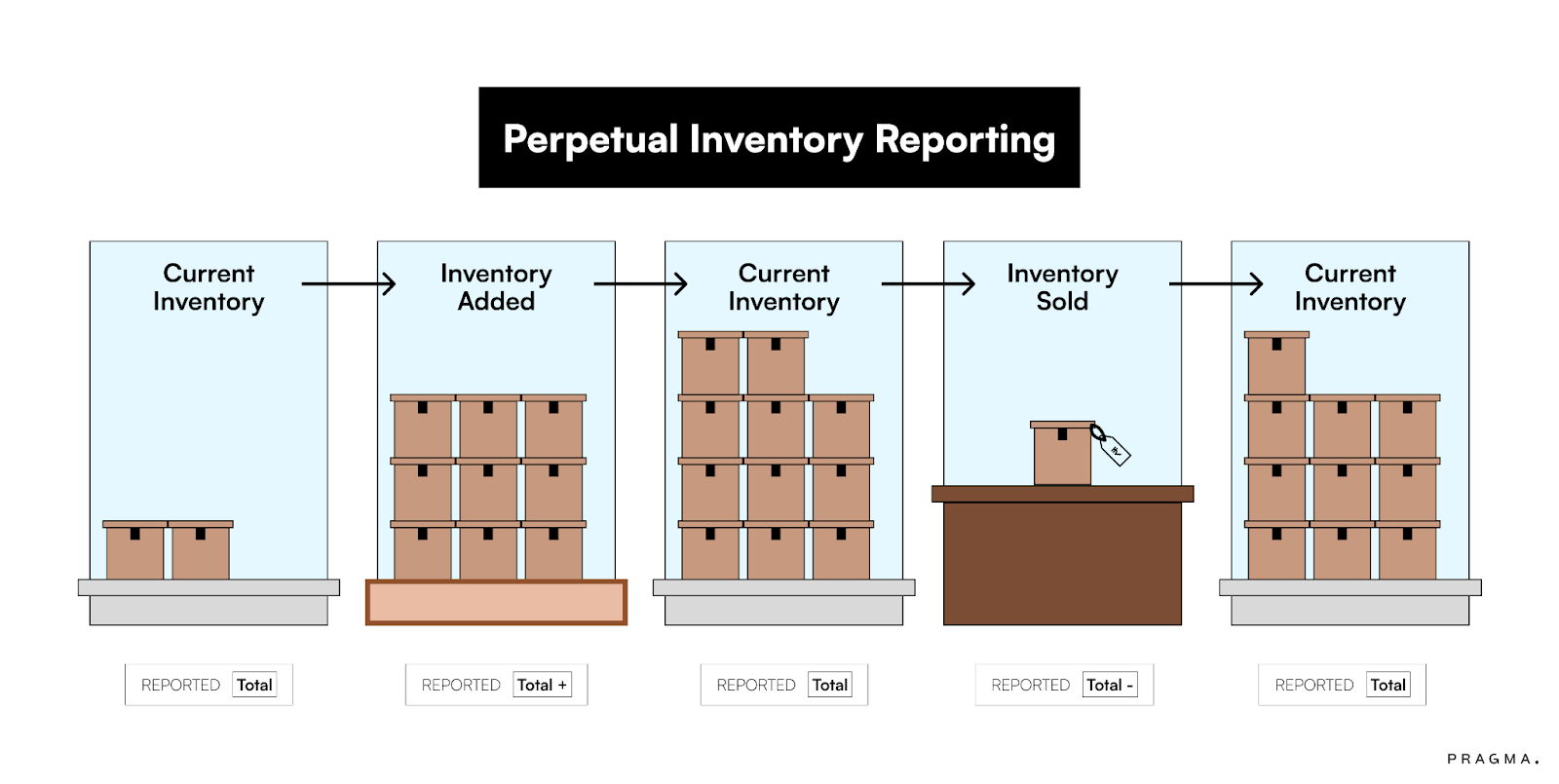
Benefits include
- Accurate stock levels at any time
- Automatic reorder notifications
- Detailed tracking of product movement
- Better prevention of stockouts
The system requires
- Barcode scanners or RFID technology
- Inventory management software
Manual Inventory Control Systems
Manual inventory control uses physical tracking methods and human documentation to monitor stock levels and movements.
It involves hands-on counting, paper-based recording, and spreadsheet management.
Key Components
- Physical documentation through stock cards or ledgers
- Regular visual inspection and counting
- Spreadsheet-based tracking
- Written purchase orders and receiving reports
Manual systems work best for small businesses with limited SKUs, companies dealing primarily in custom orders, organisations with simple supply chains and businesses starting their operations
Benefits
- Lower initial setup costs compared to software systems
- No reliance on technology infrastructure
- Direct physical verification of stock
- Simple implementation and training
- Flexibility in recording special situations or notes
Limitations
- Time-consuming data entry and updates
- Higher risk of human error in counting and recording
- Difficulty in generating quick reports
- Limited ability to analyse trends
- Challenges in maintaining real-time accuracy
Computerised Inventory Control Systems
Computerised systems use digital tools to automate stock tracking, ordering, and analysis. These systems integrate various aspects of inventory management through software solutions.
Advantages
- Automated stock level tracking and real-time visibility across locations
- Integration with business systems (point-of-sale and accounting)
- Automated reordering based on set parameters
- Comprehensive data analysis and reporting capabilities
- Prevents manual processes and data entry errors
- Advanced forecasting abilities
Challenges
- Higher upfront investment
- Dependency on technical infrastructure
- Need for regular system maintenance
- Risk of system failures or data loss
Centralised Inventory Control System
A centralised inventory control system operates through a single primary warehouse that manages all stock-related activities.
It consolidates ordering, storage, and distribution functions under one roof, allowing for streamlined operations and unified control.
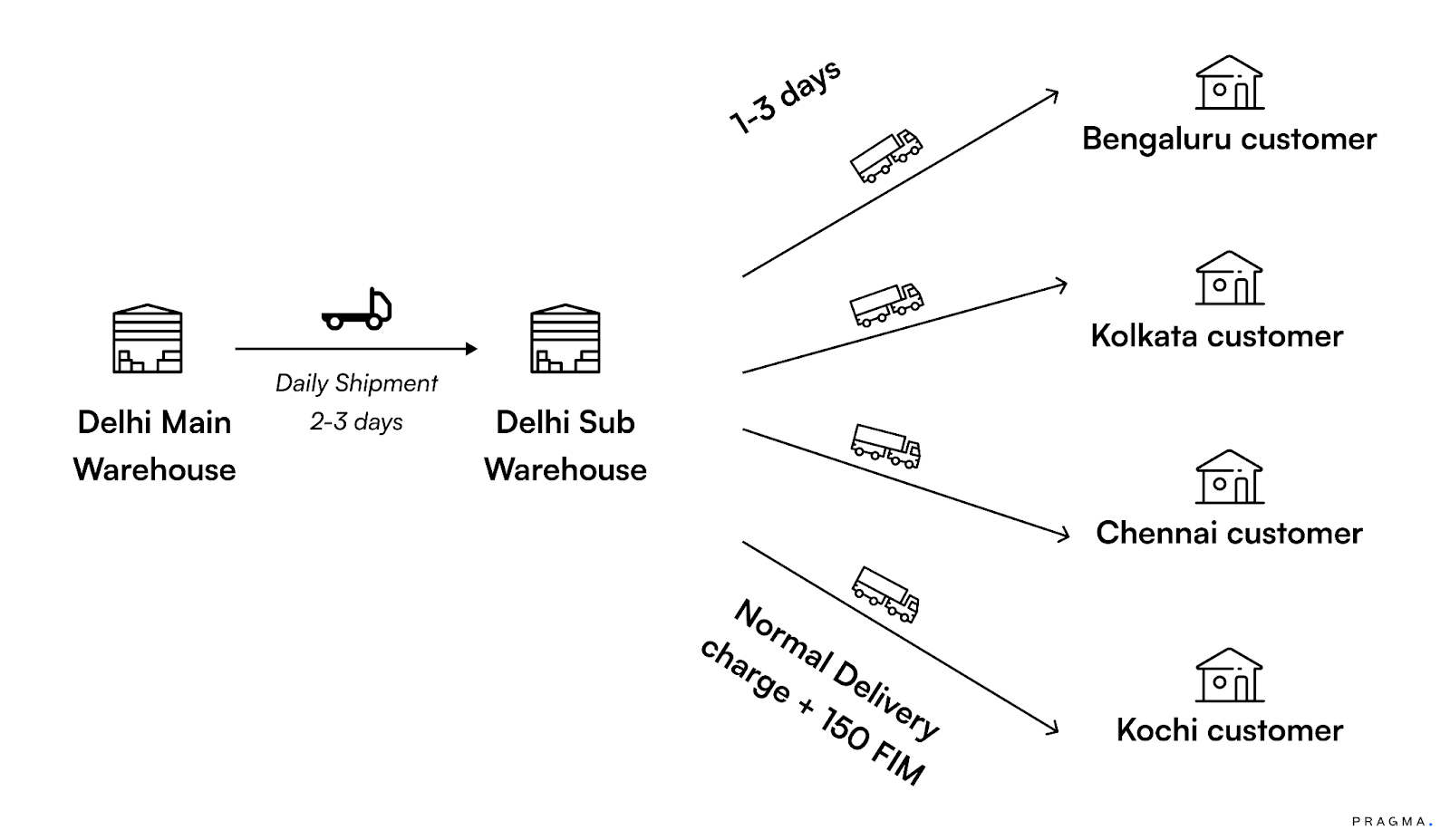
The system works by
- Handling all incoming supplier shipments at one location
- Processing orders from a central point
- Managing quality control through standardised procedures
- Coordinating distribution to all service areas
Benefits: Cost Management
- Limited storage facility requirements
- Lower staffing needs through specialised roles
- Minimised duplicate stock holdings
- Better negotiating position with suppliers due to bulk orders
Quality and Control
- Receiving and inspection procedures
- Consistent storage conditions across all products
- Unified tracking systems
- Simpler audit and inventory count processes
Challenges: Operational Considerations
- Higher transportation costs to remote locations
- Extended delivery times for distant customers
- Increased vulnerability to disruptions
- Less flexibility in meeting local market variations
Decentralised Inventory Control System
A decentralised system spreads inventory management across multiple locations, each operating with relative autonomy. It brings stock closer to customers and allows for localised decision-making.
The system functions through
- Regional warehouses managing their own stock levels
- Local procurement for certain items
- Independent order processing at each location
- Area-specific distribution networks
Benefits
- Shorter delivery times to customers
- Better adaptation to local market needs
- Lower transportation costs for regional deliveries
- Continued operation if one location faces issues
Challenges
- Higher overall inventory investment
- Duplicate resources across locations
- Varied processes between facilities
- More complex coordination requirements
Inventory Control Methods
Seven commonly used Inventory control techniques.
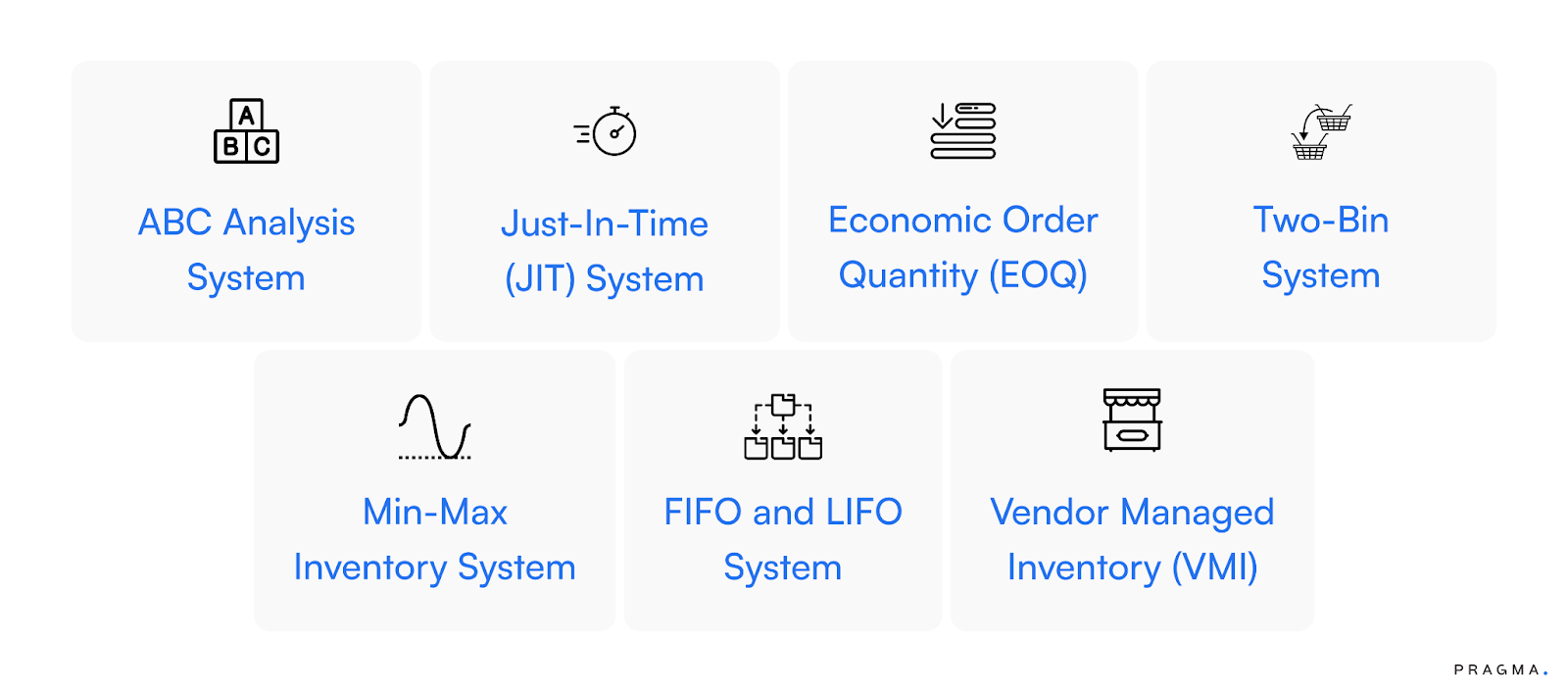
ABC Analysis System
This method categorises inventory based on value and importance:
Category A: High-value items needing strict control. These typically represent 20% of your inventory but account for 80% of your revenue.
They require frequent monitoring and careful stock-level management.
Category B: Moderate value items. These items need regular but less frequent monitoring than Category A products.
Category C: Low-value items. These constitute the bulk of your inventory items but represent a small portion of your revenue.
They need basic monitoring and can have simpler control measures.
Just-In-Time (JIT) System
Minimises inventory holding by ordering stock only when needed.
The method works by
- Maintaining minimal inventory levels
- Ordering based on actual demand
- Working closely with reliable suppliers
- Having efficient delivery systems
Economic Order Quantity (EOQ)
Determines optimal order quantities by balancing ordering costs and holding costs.
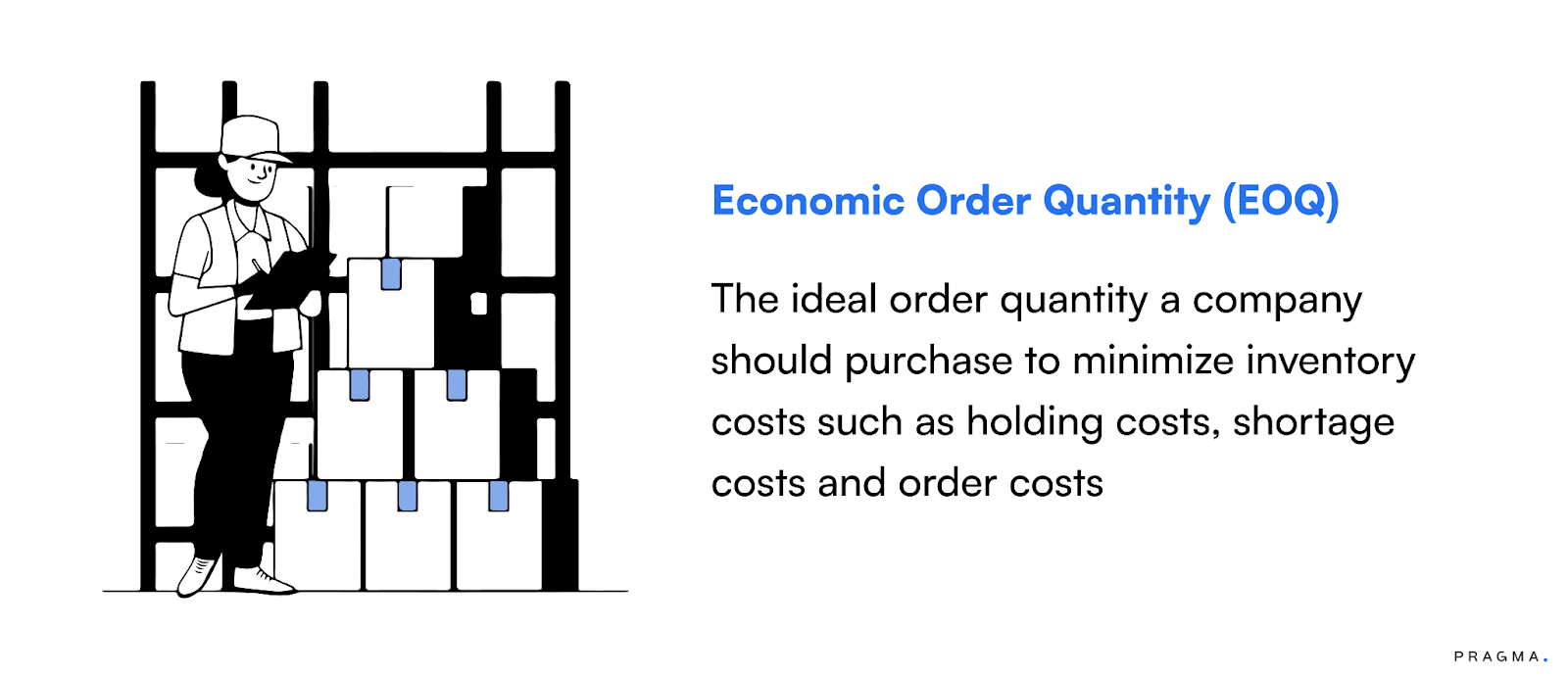
It considers
- Annual demand
- Cost per order
- Annual holding cost per unit
- Purchase cost per unit
Min-Max Inventory System
Sets minimum and maximum stock levels for each product. When inventory falls below the minimum level, you order enough to reach the maximum level.
It works well for D2C brands with predictable demand patterns.
The technique requires setting three levels
- Minimum: The lowest acceptable stock level
- Maximum: The highest stock level you'll maintain
- Reorder Point: The level at which you place new orders
Two-Bin System
A simple yet effective method where inventory is stored in two bins.
When the first bin empties, you start using the second bin and place an order to refill the first one.
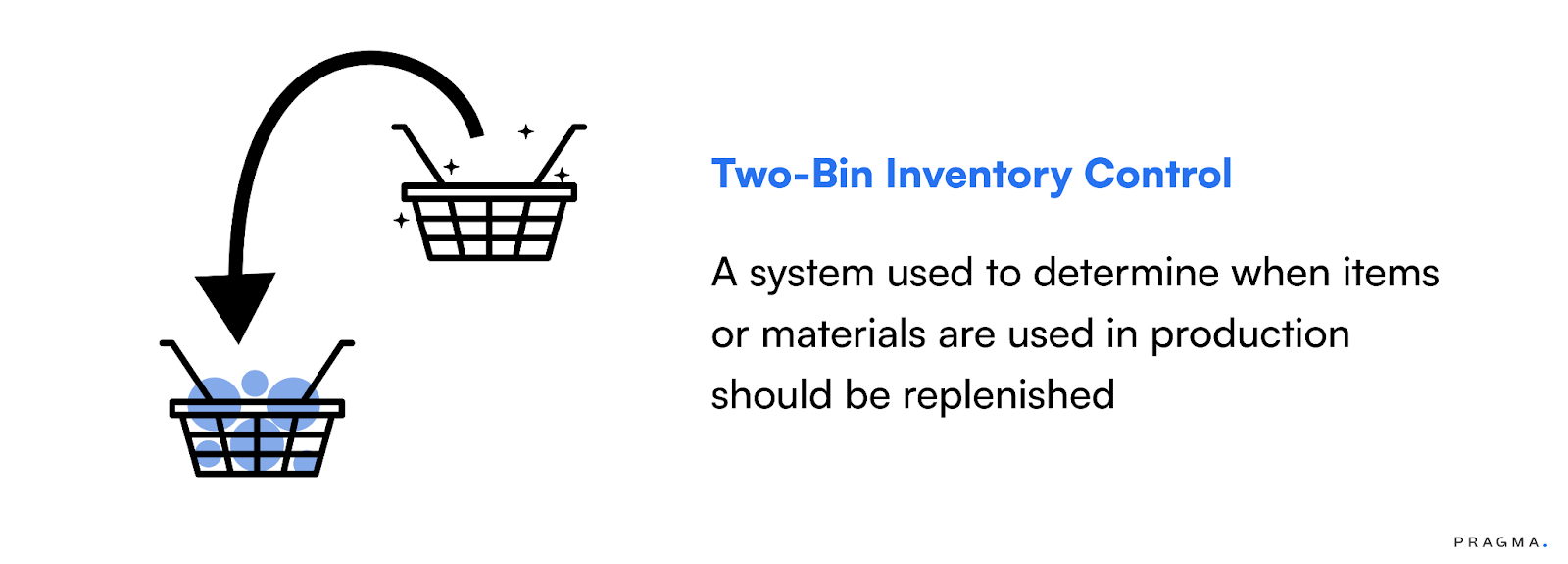
It is best for
- Small components
- Regular-use items
- Products with steady demand
FIFO and LIFO Systems
First In, First Out (FIFO) means selling older stock first, while Last In, First Out (LIFO) means selling newer stock first.
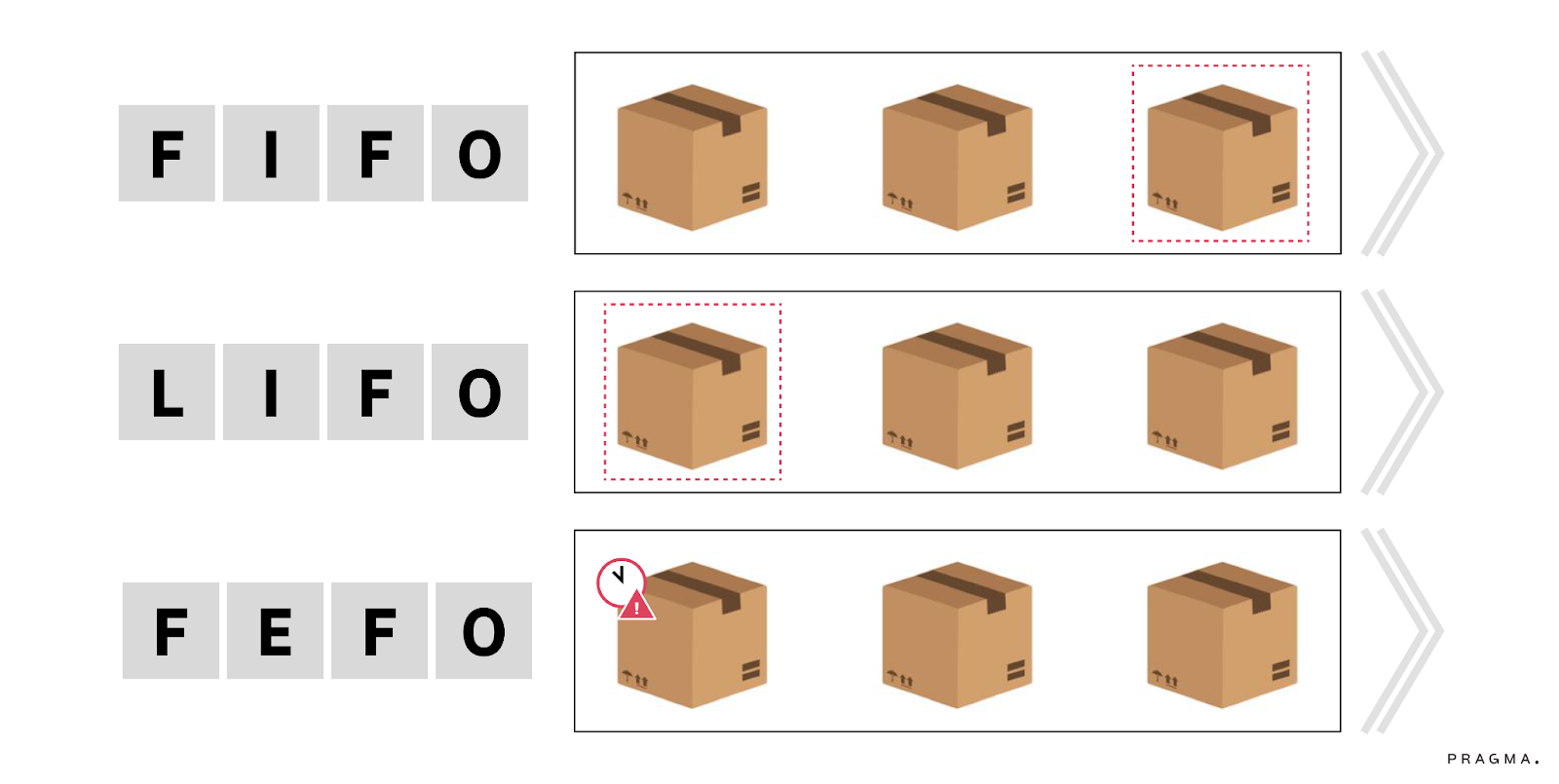
For E-commerce companies, FIFO works best for
- Perishable goods
- Fashion items
- Seasonal products
- Items with expiry dates
LIFO suits
- Non-perishable items
- Products without expiry dates
- Items where freshness isn't a priority
Vendor Managed Inventory (VMI)
In this system, suppliers manage your inventory levels, similar to how e-commerce logistics partners handle your supply chain operations.
They monitor your stock and replenish it as needed and helps
- Eliminate your inventory management burden
- Improves supplier relationships
- Prevent stockouts
- Optimises order quantities
Steps Involved in Inventory Control
The effectiveness of an inventory control system depends on three fundamental components which are:
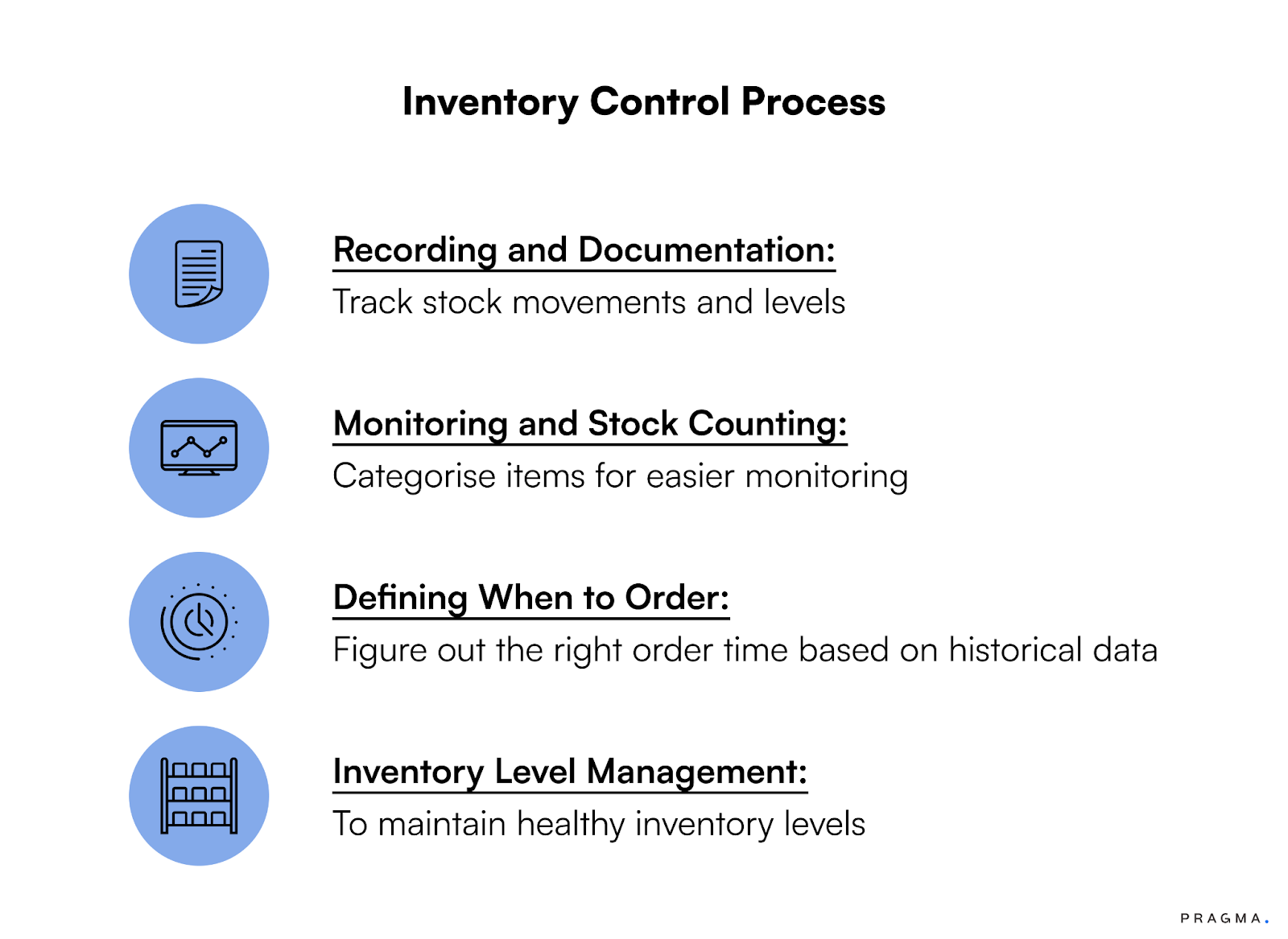
- Recording and Documentation
Inventory control requires two main types of records—those tracking stock movements and those tracking stock levels.
Both are interconnected since each movement affects the inventory level at any location.
These records should be formally cross-referenced to enable tracking items from reception to dispatch.
Key documentation requirements include
- Stock cards and bin cards that record physical quantity movements for each SKU
- Inventory ledger that tracks transactions from a central location
- Waybills or delivery notes for received goods
- Stock release orders for dispatching products
- Loss reports for damaged or spoiled items
The documentation system should be set up when operations begin and warehouse staff must receive proper training to implement it correctly.
And all stock movement records must be updated immediately.
- Monitoring and Stock Counting
Stock levels requiring special attention
- Items reaching defined threshold levels (reorder or safety stock points)
- Products belonging to specific projects/campaigns
- Items with expiration dates
- High-rotation inventory items
- Products core to business operations
- Items with short reorder cycles
Performance Metrics to Monitor
- Inventory rotation frequency, volume and value
- Time taken for dispatch preparation
- Number of stockout incidents
- Stock valuations
- Quantities and values lost
If you are using physical counting procedures consider
- General physical inventory: Covering entire stock periodically
- On-demand counting: For specific items requiring verification
- Sample-based counting: Random spot checks during audits
During physical counts, the stock should remain stationary—no movement should occur for items being counted.
For spot checks, only the selected item’s movement needs to be halted.
- Defining When to Order
Based on pre-established frequency
- Used in long-term programs with steady consumption
- Suitable for push strategy operations
- Effective for internationally sourced items with long transit times
- Works well when ordering multiple product groups simultaneously
Based on Stock Level Thresholds
- Stock levels are monitored continuously
- Orders are placed when inventory reaches the reorder point
- Better suited for locally sourced items
- Useful for independent items with variable demand
For the order quantity calculation consider these points
- Demand during lead time
- Review period requirements
- Safety stock needs
- Current stock levels
- Items already in transit
- Inventory Level Management
To maintain inventory levels
- Calculate buffer stock based on lead time and daily consumption
- Set safety stock levels to prevent stockouts
- Establish reorder points that consider both buffer and safety stock
- Define maximum stock levels based on storage capacity
- Manage seasonal variations in demand
- Monitor stock turnover rates
Advantages of Effective Inventory Control
Here are 10 key advantages of effective inventory control
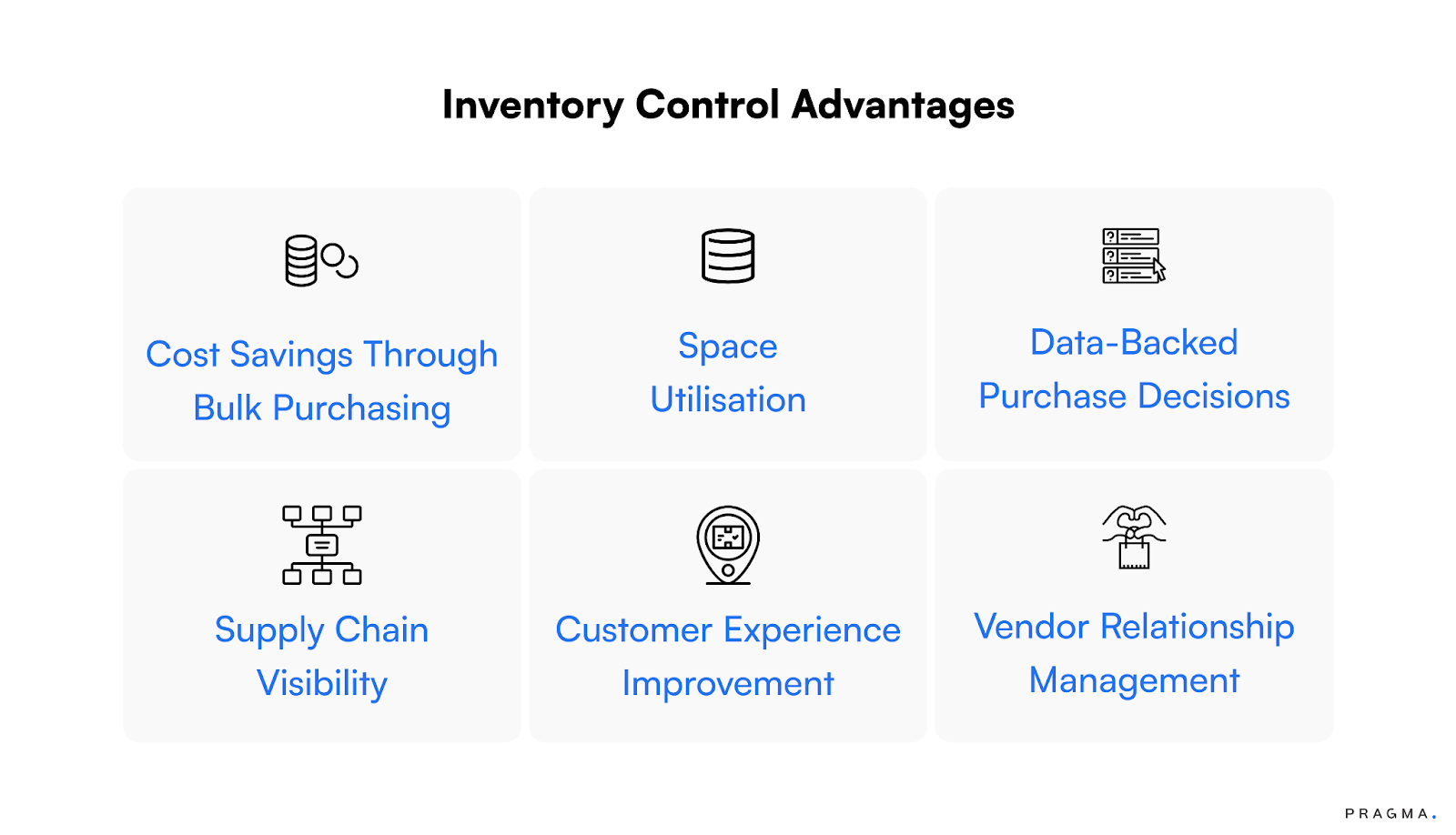
- Cost Savings Through Bulk Purchasing
With accurate stock tracking, you can consolidate orders and negotiate volume discounts without risking overstock situations. It balances bulk purchase savings with storage costs.
- Space Utilisation
Proper inventory control helps organise warehouse space efficiently by identifying fast and slow-moving items, which improves picking efficiency.
- Data-Backed Purchase Decisions
Access to historical sales data and stock movement patterns allows for smarter purchasing. You can predict demand trends and adjust stock levels accordingly.
- Supply Chain Visibility
Real-time inventory tracking across locations provides clear visibility into stock movement. It helps prevent stockouts while optimising transfer shipments between warehouses.
- Customer Experience Improvement
Accurate stock information prevents order cancellations and delays, while proper returns management strengthens customer trust.
When customers receive reliable delivery estimates and complete orders, it builds trust and encourages repeat purchases.
- Vendor Relationship Management
Consistent order patterns and accurate forecasting help build reliable supplier relationships. Leading to better credit terms, priority fulfilment, and improved service levels.
Challenges in Inventory Control
Common inventory control challenges faced by Indian D2C brands include
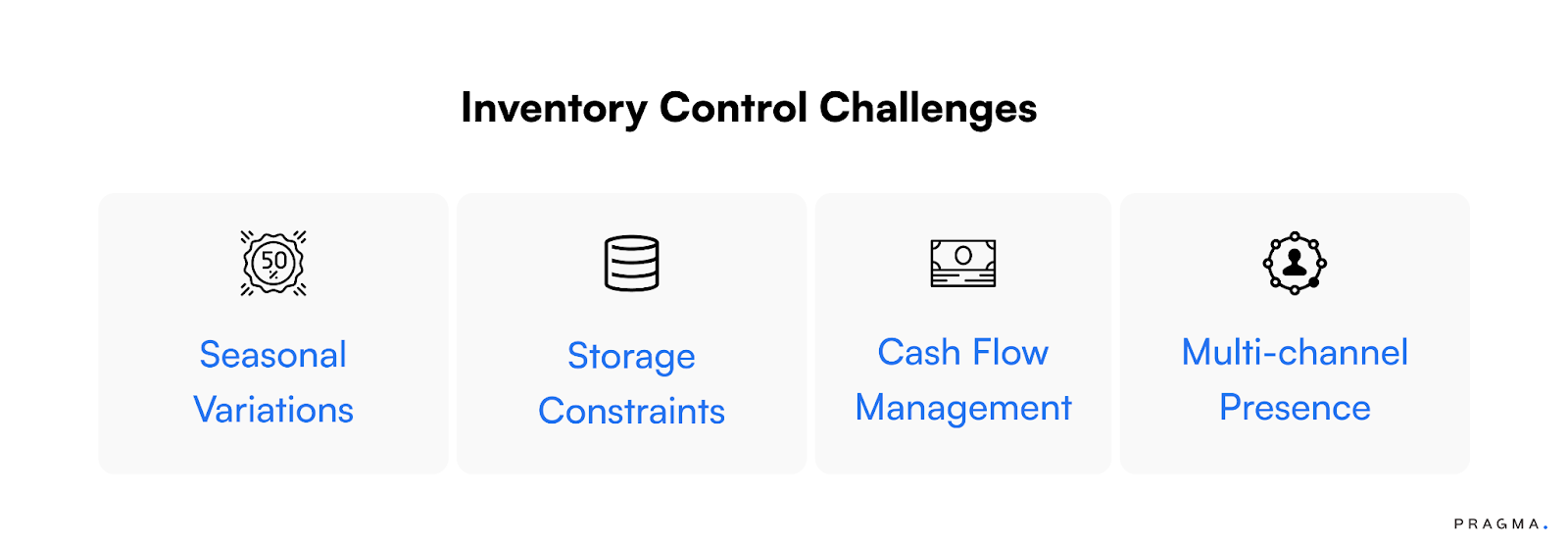
- Seasonal Variations: Managing stock during festivals and sale seasons
- Storage Constraints: Balancing warehouse space with inventory needs
- Cash Flow Management: Optimising stock levels to maintain healthy working capital
- Multi-channel Presence: Coordinating inventory across various sales platforms, including managing returns and RTO challenges that impact stock levels
Whether you're running a small D2C brand or managing multiple warehouses, the principles remain consistent—keep enough stock to meet demand without overextending resources.
Best Practices for Inventory Control
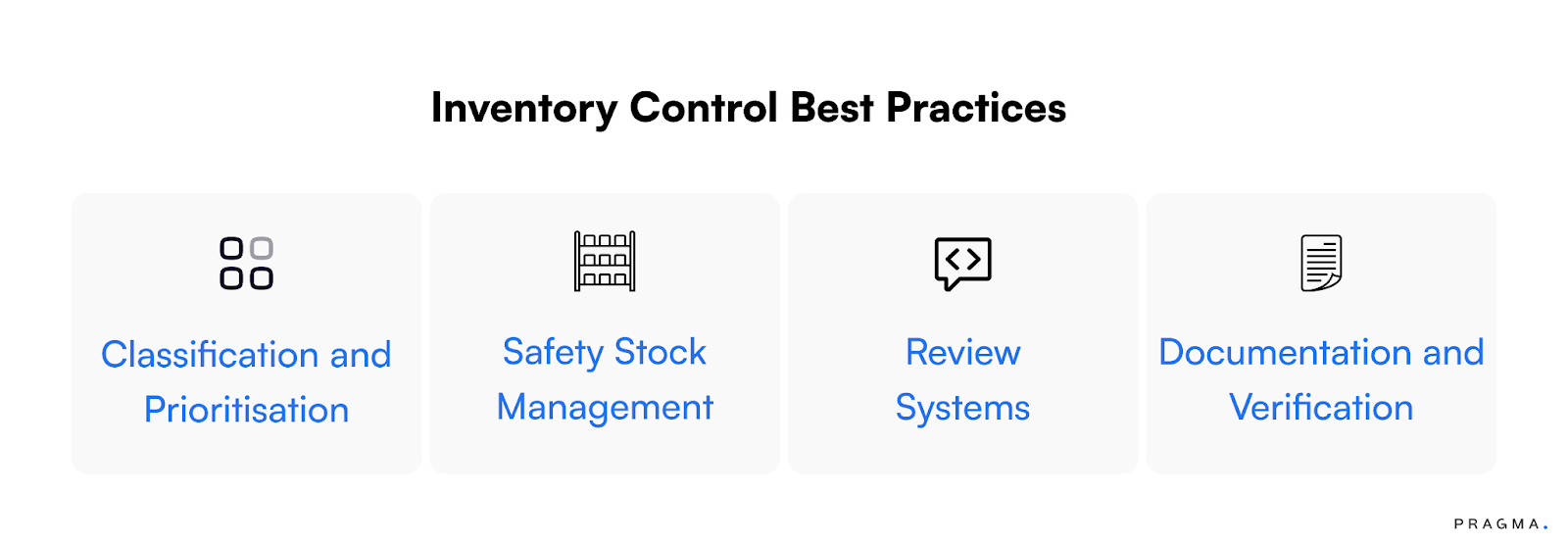
Classification and Prioritisation
The ABC analysis method segments inventory based on value and impact, which allows for better resource prioritisation.
- A-category items, typically comprising 10% of total items but representing 70% of consumption value, require rigorous monitoring and frequent reviews.
- B-category items need moderate controls,
- While C-category items can be managed with basic systems.
Safety Stock Management
Maintain appropriate safety stock levels to protect against supply chain uncertainties and demand fluctuations.
The safety stock calculation should account for both consumption variations and lead time uncertainties.
For consumption-based calculations, analyse the difference between maximum and normal consumption rates multiplied by lead time.
When lead times are variable, multiply the normal consumption rate by the difference between maximum and normal lead times, to ensure an optimal buffer without excessive holding costs.
Review Systems
Two primary approaches dominate inventory review, Continuous Review (ROL) and Periodic Review systems.
The ROL method monitors stock levels continuously, triggering orders when inventory reaches predetermined points. It works best for items with consistent demand patterns and significant value.
Periodic Review systems examine stock levels at fixed intervals, making them suitable for items with seasonal or fluctuating demand. It sheds off administrative burden but requires higher safety stock levels to cover uncertainties between reviews.
Documentation and Verification
A documentation system forms the foundation of effective inventory control. Beyond basic stock records, maintain detailed information about
- Movement patterns and velocity
- Supplier performance metrics
- Quality inspection outcomes
- Stock reconciliation reports
Regular physical verification through cycle counts will help you maintain accuracy between full inventory audits. Set clear procedures for investigating and resolving discrepancies promptly.
Role of Technology in Inventory Control
Modern inventory management systems combine software, hardware, and automation to improve accuracy and efficiency.
Here are four technologies that make inventory control better.
Inventory Management Software
A well-implemented software system serves as the central hub for inventory operations.
These systems track stock movement in real time, automate reordering processes, and provide insights through analytics.
Barcode and RFID Integration
Identification technologies like barcodes and RFID tags enable quick, accurate stock tracking.
While barcodes require line-of-sight scanning, RFID allows contactless reading of multiple items simultaneously.
It speeds up receiving, picking, and counting processes while reducing human error.
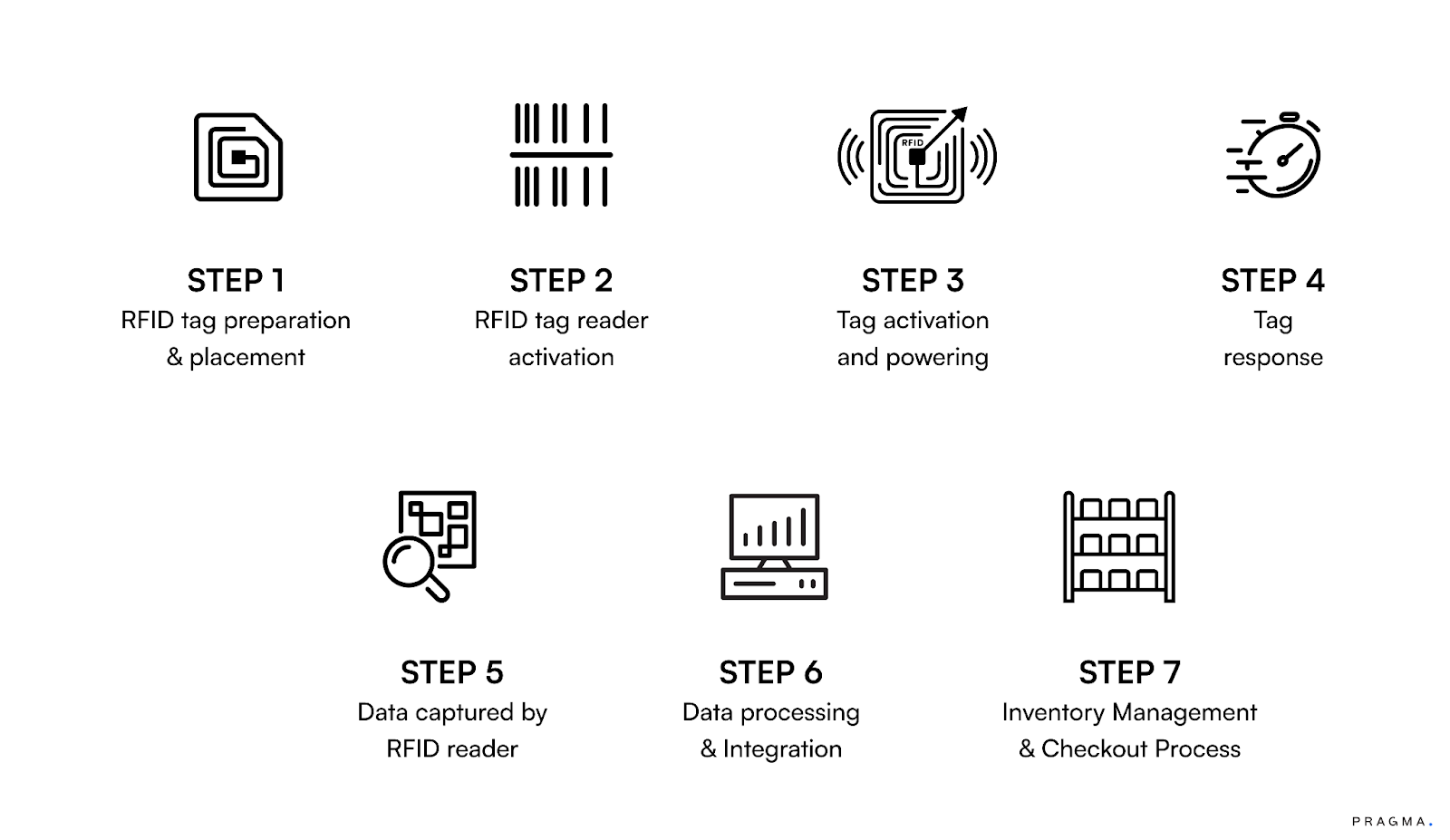
You can choose between:
- Simple barcode systems for basic tracking
- Advanced RFID setups for complex operations
- Hybrid solutions combining both technologies
The choice depends on factors like
- Stock volume and variety
- Speed requirements
- Budget constraints
- Integration needs
Warehouse Management Systems
WMS software optimises the storage and movement of inventory within warehouses, including returns processing.
These tools map warehouse layouts, track item locations, and guide efficient picking routes.
“Modern warehouse management system (WMS) technologies go beyond conventional warehouse functions to cover every stage of the product lifecycle. This includes accurate tracking in the warehouse to stock input, and manages every other step. In the current high-tech era, these solutions are very critical to inventory control —an important component of a successful business.” Vikas Wadhwa, Chief Operating Officer, Bar Code India
A WMS helps resolve picking errors and improves space utilisation through features like.
- Location tracking and optimisation
- Batch and lot control
- Cross-docking capabilities
- Labour management Quality control integration
Choosing the Right Inventory Control System for Your Business
Here's a detailed breakdown guide to help you make this decision.

To Wrap It Up
Running an e-commerce or D2C brand in India means you're constantly balancing inventory decisions that affect your cash flow, operations, and customer demands.
As online sales channels multiply and customer expectations evolve, simple stock tracking no longer suffices.
And for brands selling through marketplaces, social commerce, and their websites, poor inventory control might lead to problems like overselling, delayed shipments, and wasted warehouse space.
But now that you know what inventory control is, its methods and its process, begin with the basics and gradually upgrade your inventory control practices as your business expands.
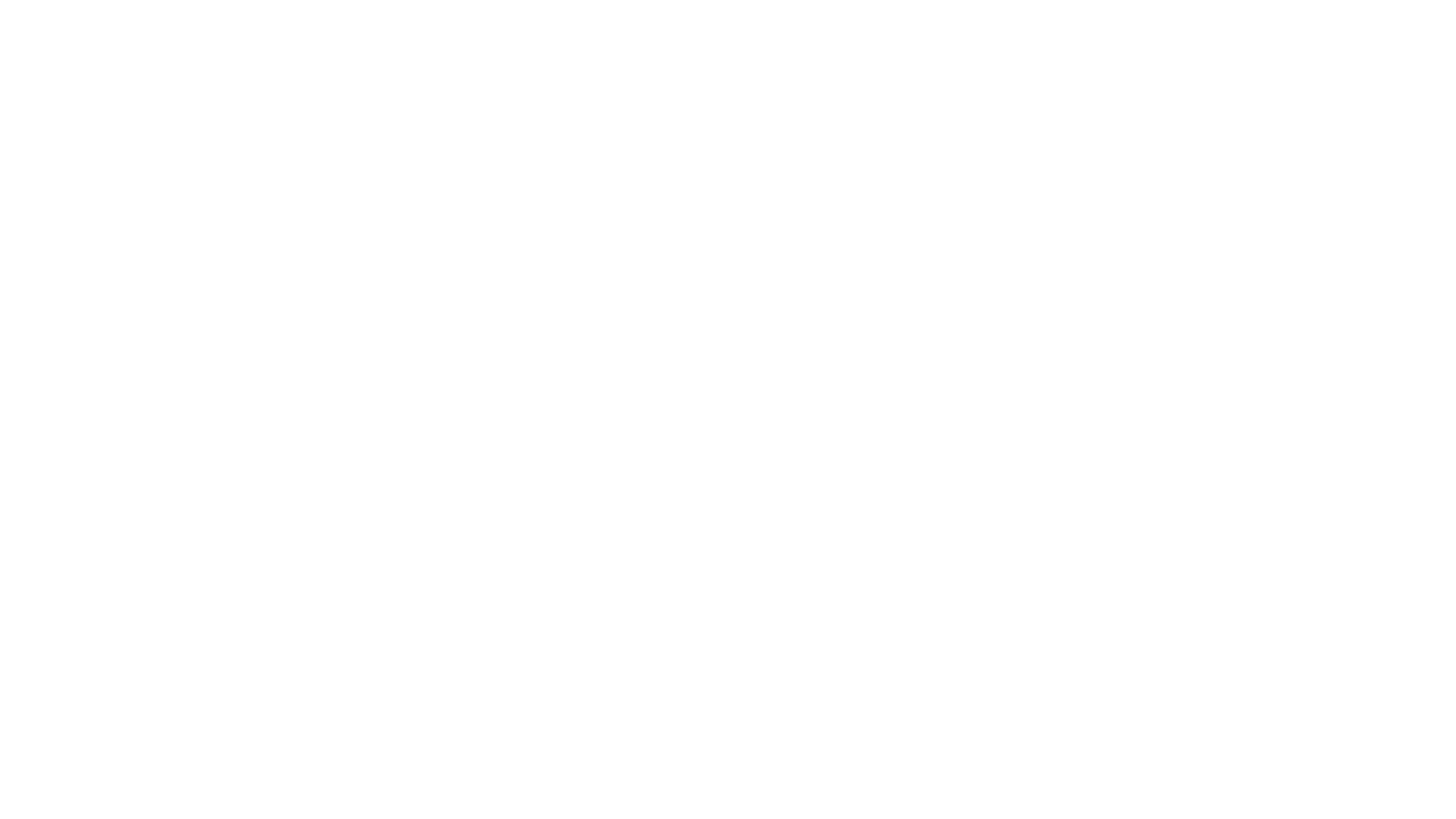
FAQs (Frequently Asked Questions On What Is Inventory Control)
Why need inventory control?
Inventory control helps e-commerce brands maintain optimal stock levels, avoid working capital blockage, and ensure timely order fulfilment. It prevents common issues like stockouts and excess inventory that directly impact profitability.
How to calculate inventory?
Calculate inventory by tracking stock receipts, sales, returns, and adjustments. Start with opening stock, add new purchases, subtract sales and damages, and then validate through physical counts to maintain accuracy.
What is inventory control in the supply chain?
It's the process of managing stock from receiving to delivery, ensuring smooth flow between suppliers, warehouses, and customers while minimizing costs and maintaining service levels.
Talk to our experts for a customised solution that can maximise your sales funnel
Book a demo