Shipping delays damage customer trust, storage costs eat into margins, and supply shortages halt production.
These problems multiply when you confuse logistics with supply chain management.
What is the difference between logistics and supply chain management? repeatedly surfaces as e-commerce brands struggle with
- Misaligned inventory levels
- Rising transportation costs
- Fulfilment bottlenecks
- Communication gaps with suppliers
The distinction between logistics and supply chain management impacts every operational decision.
From manufacturing scheduling to last-mile delivery, understanding SCM vs logistics will help you prevent costly mistakes and operational roadblocks.
This guide breaks down the key distinctions, explained through practical examples to help you optimise your business operations.
What Is Logistics? A Detailed Explanation
Logistics is the systematic management of storing, moving, and delivering goods from the origin to the final destination.
For e-commerce brands, it functions as the operational backbone that ensures successful product delivery to customers
At its core, logistics consists of two main operational streams
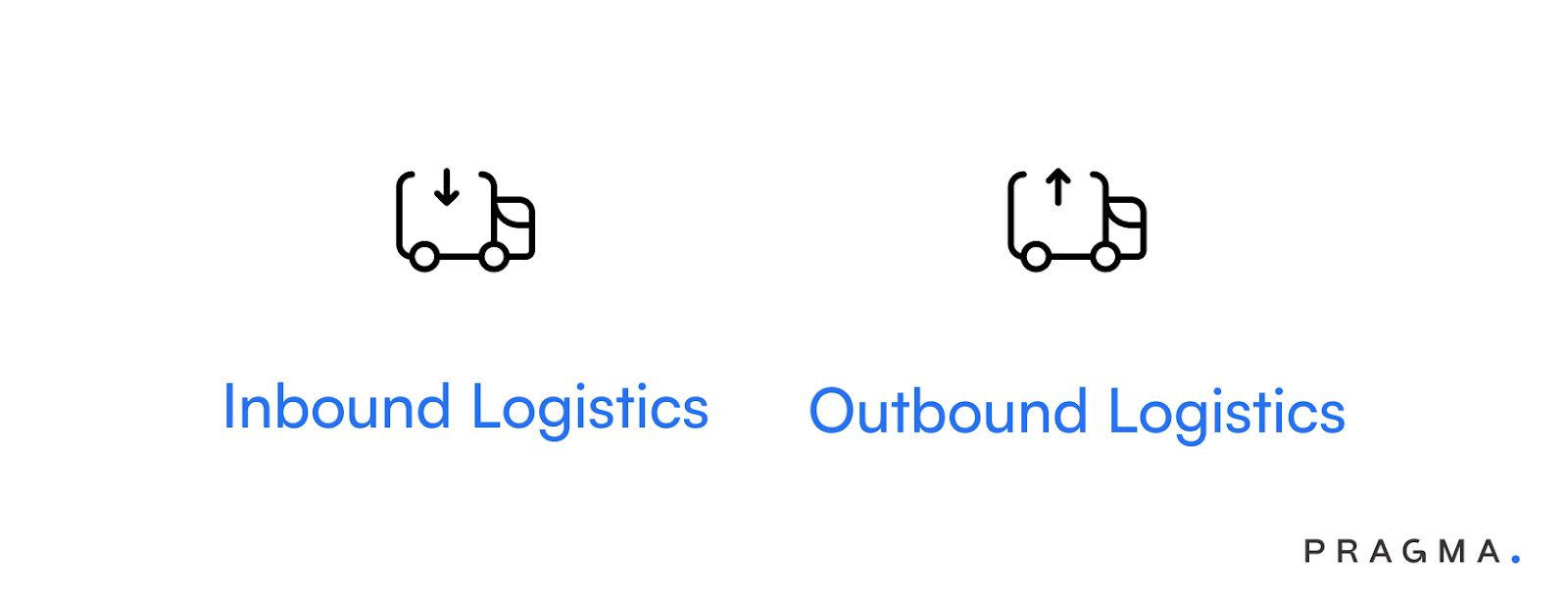
Inbound Logistics:
Manages incoming inventory, supplier relationships, and warehouse operations
Outbound Logistics:
Handles order fulfilment, shipping, and customer delivery
However it becomes even more complex when brands expand their operations, leading many to consider third-party logistics partners who can manage these intricate fulfilment networks while maintaining service quality.
The process begins with planning and organisation, it includes developing storage strategies, establishing materials handling protocols, and creating inventory management systems.
Each element must work in harmony to maintain efficient operations while controlling costs.
Transportation management also directly impacts your operational costs. It involves selecting carriers, optimising delivery routes, and coordinating shipments across different regions.
Modern e-commerce logistics also incorporates several key operational functions
Inventory Control: Managing stock levels and storage efficiency
Order Processing: Converting customer orders into fulfilled deliveries
Returns Management: Handling product returns and exchanges
Quality Assurance: Ensuring product integrity throughout transit
What Is Supply Chain Management? Key Concepts to Know
Supply Chain Management (SCM) is the end-to-end coordination of all activities involved in producing and delivering products to customers.
Fundamental Components of Supply Chain Management
Supply Chain Management comprises five distinct but interconnected aspects that work together to create an efficient product delivery system.
Strategic Planning
The foundation of SCM begins with comprehensive planning that includes demand forecasting, resource allocation, and network design.
It requires analysing market trends, predicting future demand, and establishing metrics for success.
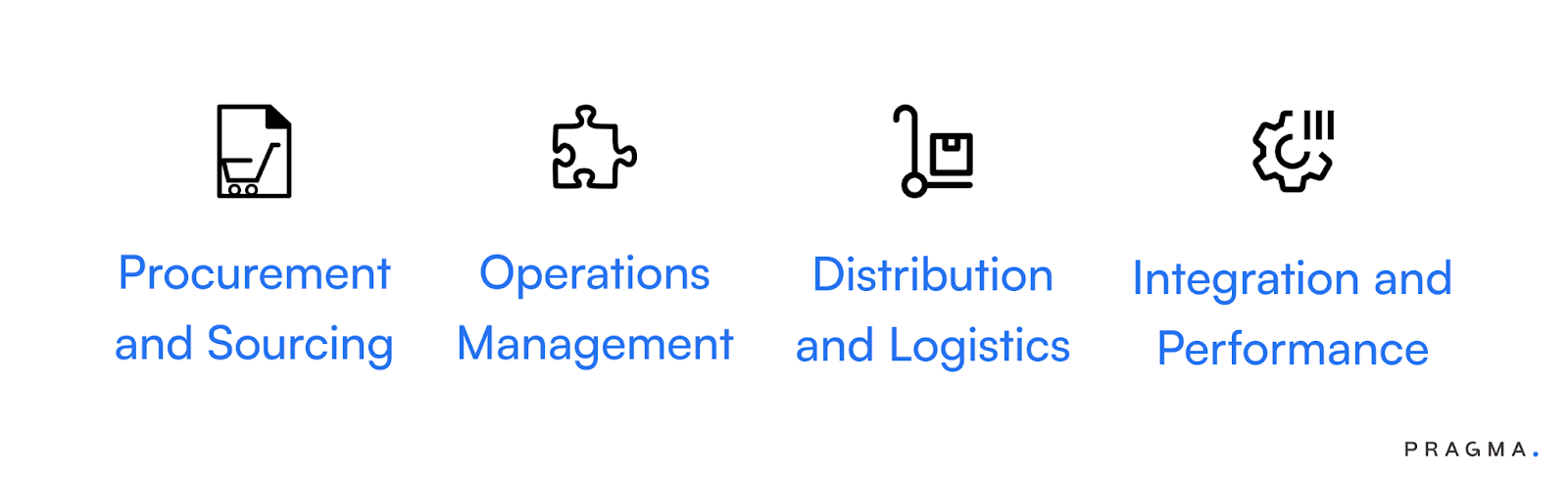
Procurement and Sourcing
Handling supplier relationships and material acquisition. It includes
- Evaluating and selecting suppliers
- Negotiating contracts and pricing
- Managing supplier performance
- Ensuring quality control of materials
- Coordinating cross-border sourcing when needed
Operations Management
Overseeing the processing of raw materials into finished products. For D2C brands, this involves
- Production scheduling and quality control
- Capacity planning and workload management
- Equipment maintenance and efficiency optimisation
- Inventory tracking and stock-level management
- Process improvement and cost reduction initiatives
Distribution and Logistics
While logistics is one area, the distribution network constitutes
- Warehouse location and management
- Transportation strategy and carrier selection
- Inventory deployment across locations
- Last-mile delivery coordination
- Returns processing systems
Integration and Performance
The final aspect focuses on bringing all elements together through
- Technology implementation and data sharing
- Partner collaboration and communication
- Performance measurement and analytics
- Risk management and contingency planning
- Continuous improvement initiatives
Supply chain management's key responsibilities include developing supplier relationships, production scheduling, quality control, and optimising the distribution network.
Each element requires careful attention and coordination to create an efficient flow of goods that meets customer demands while minimising costs.
SCM focuses on several critical business objectives -
Cost Reduction: Optimising operations across the entire supply chain
Quality Improvement: Maintaining standards from production to delivery
Risk Management: Identifying and mitigating potential disruptions
Performance Monitoring: Tracking and improving supply chain metrics
Key Differences Between Logistics and Supply Chain Management
Understanding the key differences between logistics and supply chain management helps you run operations effectively.
Supply chain management operates on a broader scale than logistics alone.
While logistics focuses on movement and storage, SCM oversees the entire journey from raw material procurement to final customer delivery.
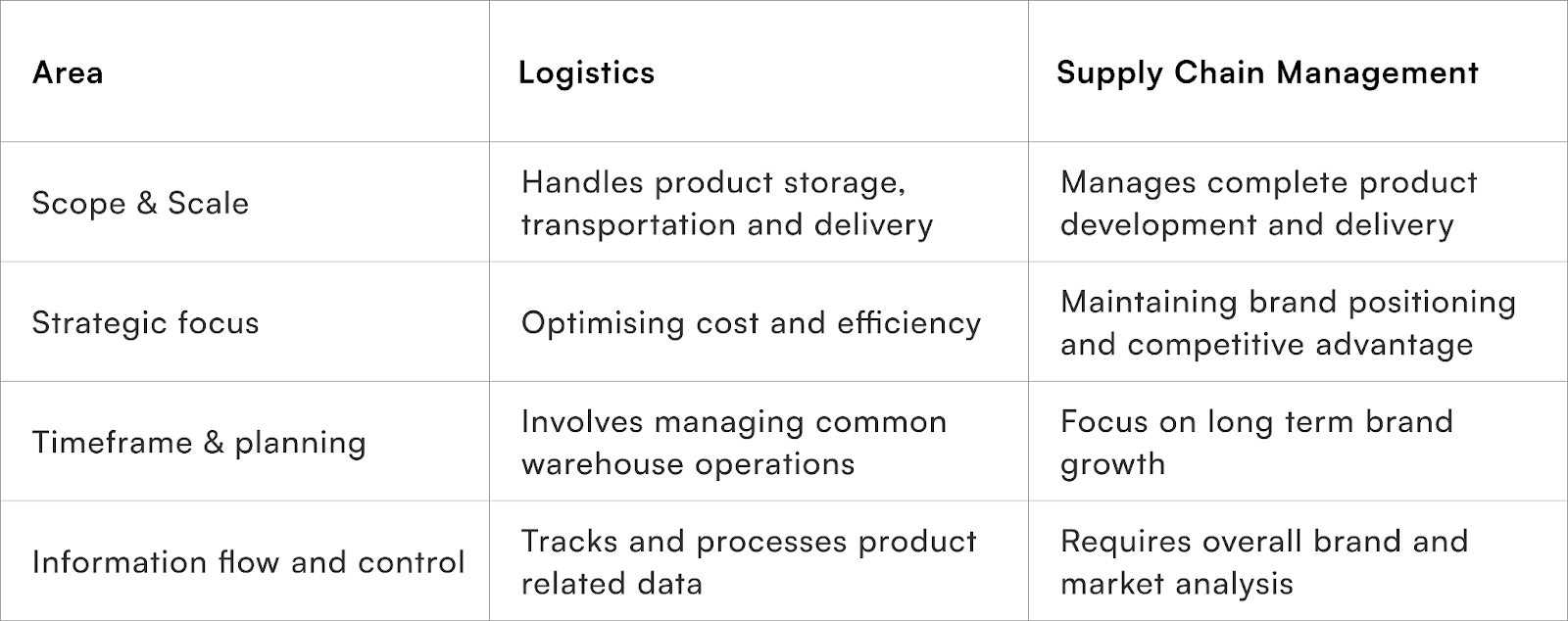
Scope and Scale
Logistics manages specific operational functions within your organisation, primarily focusing on product storage, transportation, and delivery.
It handles the physical movement of goods from warehouses to customers, including inventory management and order fulfilment.
Supply chain management, however, oversees the complete network of partners and processes involved in product creation and delivery.
From supplier relationships, manufacturing, and distribution networks to customer service.
SCM coordinates everything from raw material sourcing to final item delivery.
Strategic Focus
Logistics focuses on optimising individual operations to reduce costs and improve efficiency.
The primary goals include minimising storage expenses, optimising transportation routes, and ensuring accurate order fulfilment.
Supply chain management, on the other hand, helps build competitive advantages through integrated processes.
It aims to create value through better supplier relationships, improved product quality, and efficient resource utilisation, to help you maintain market position and adapt to changing customer demands on the go.
Timeframe and Planning
Logistics typically operates on shorter time horizons, managing day-to-day activities like order processing, shipment coordination, and inventory control.
Success metrics often focus on immediate results such as delivery times and order accuracy.
Supply chain management combines both short-term execution and long-term planning.
It involves forecasting market trends, building partner networks, and planning for future growth, to help you build sustainable and long-term competitive advantages.
Information Flow and Control
Logistics primarily tracks operational data related to the movement and storage of goods, such as inventory levels, shipping status, delivery times, and warehouse capacity.
These metrics help optimise daily operations and maintain service levels.
Supply chain management requires comprehensive data across the entire network, including market trends, supplier performance, production schedules, and customer demand patterns.
How Logistics Fits Into the Supply Chain
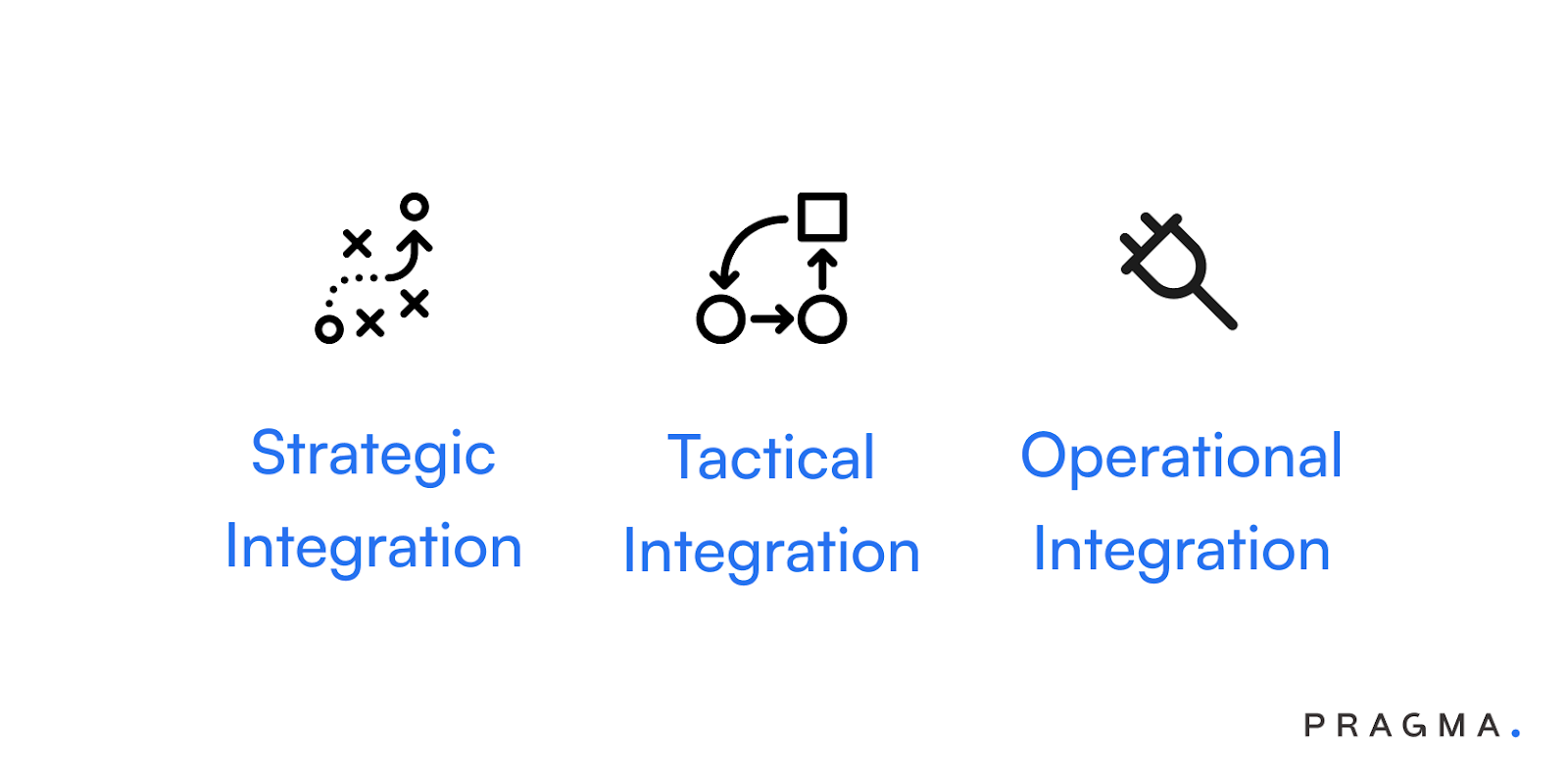
Logistics functions as the practical system that converts supply chain strategies into measurable results through movement and storage operations.
The difference between logistics and supply chain management becomes clear when you look at how logistics integrates within the broader supply chain framework.
Strategic Integration
Supply chain decisions rely on logistics capabilities, such as selecting supplier locations, production facilities, or distribution networks.
For D2C brands, shipping expenses and delivery timeframes influence fulfilment centre placement decisions.
Tactical Integration
At this level, logistics merges with multiple supply chain elements
Stock placement: Setting optimal inventory positions
Manufacturing timing: Coordinating production with transport availability
Space utilisation: Managing warehouse and delivery resources
Service provider selection: Evaluating carriers and fulfilment partners
Operational Integration
Here, logistics executes daily activities while feeding valuable data back into the supply chain.
- Current inventory levels inform purchasing decisions
- Shipping performance affects customer communications
- Transport costs guide product pricing
- Storage space impacts production quantities
Examples of Logistics and Supply Chain Management in Action
Logistics Example: A D2C Athletic Apparel Brand
Let's say you manage daily delivery operations for your D2C athletic wear brand. Your logistics will focus primarily on the fulfilment activities.
You receive bulk inventory at your warehouse, where their logistics team
- Records incoming stock in their inventory management system
- Stores products in designated warehouse locations
- Processes incoming online orders
- Picks and packs items for shipping
- Arranges courier pickups
- Manages tracking updates to customers
- Handles returns from customers
When a customer orders a pair of running shorts, the logistics process involves checking inventory, locating the item in the warehouse, packing it properly, and selecting the most efficient shipping method for timely delivery.
If the customer needs to return the item, the logistics team manages the reverse process, including return label generation and refund processing.
Supply Chain Management Example: A D2C Skincare Brand
Imagine you run a D2C skincare brand launching a new face, supply chain management in action will look like the following.
The process begins with formula development and involves coordinating multiple partners
- Working with laboratories to finalise the serum formula
- Sourcing raw ingredients from multiple suppliers
- Coordinating with packaging manufacturers for bottles and boxes
- Managing production schedules with manufacturing partners
- Arranging storage and distribution networks
- Setting up fulfilment processes
- Planning marketing launches with inventory availability
Your SCM team must ensure that all components (ingredients, packaging, labels) arrive at the manufacturer at the right time.
They need to forecast demand accurately to determine initial production quantities, conduct quality testing, manage inventory across warehouses, and ensure proper delivery to customers.
Challenges in Logistics and Supply Chain Management
E-commerce and D2C brands face complex challenges in managing both logistics operations and broader supply chain networks.
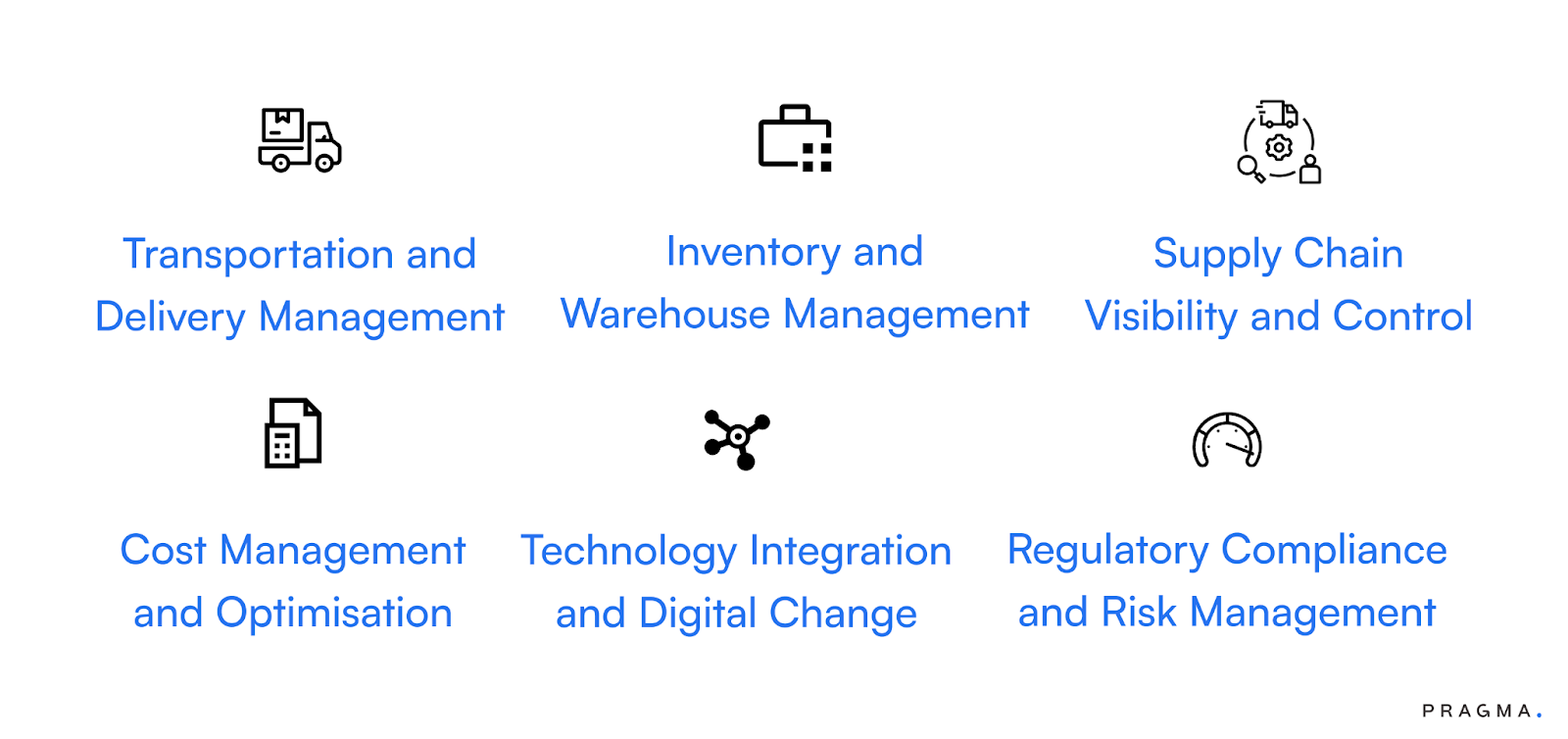
For example,
Transportation and Delivery Management
As e-commerce volumes grow, transportation networks face increasing strain.
And this strain becomes particularly evident during peak seasons when holiday shopping surges require precise coordination of inventory, warehousing, and delivery networks
The challenges include managing rising fuel costs, handling carrier capacity limitations, and meeting customer expectations for faster delivery.
Last-mile delivery presents specific difficulties, especially in diverse geographical regions where delivery infrastructure is not yet developed.
For e-commerce brands, managing international shipping adds another layer of complexity.
Cross-border logistics involve navigating customs regulations, managing documentation, and handling longer transit times. These factors directly impact delivery costs.
Inventory and Warehouse Management
Modern inventory management requires sophisticated approaches to
- Accurately predicting product needs across multiple channels
- Maintain optimal inventory levels while minimising carrying costs
- Manage space utilisation and labour efficiency
- Sync inventory across different storage facilities
- Handle reverse logistics efficiently
Warehouse operations also depend on systems to handle both incoming inventory and returns efficiently.
This connection between warehouse management and returns processing systems often determines how successfully a brand can manage its reverse logistics
Supply Chain Visibility and Control
Limited visibility across supply partners often creates operational blind spots. Brands struggle with
- Monitoring product movement from source to delivery
- Maintaining effective information flow between stakeholders
- Gathering accurate data for decision-making
- Identifying potential disruptions before they impact operations
- Ensuring consistent standards across the supply chain
Cost Management and Optimisation
Rising operational costs also pressure companies to find new efficiency opportunities while maintaining service quality.
Key financial challenges include
- Warehouse operational expenses
- Transportation and fuel costs
- Labour and training investments
- Technology infrastructure expenses
- Inventory carrying costs
Technology Integration and Digital Change
While digital solutions offer significant benefits, implementation presents several challenges, such as
- Selecting appropriate technology platforms
- Ensuring system compatibility
- Managing data security
- Training staff effectively
- Maintaining continuous operations during transitions
Regulatory Compliance and Risk Management
Global supply chains face increasing regulatory complexity and various operational risks, for example
Compliance Requirements
- International trade regulations
- Environmental standards
- Safety requirements
- Documentation management
- Quality certifications
Risk Factors
- Supplier reliability issues
- Market demand fluctuations
- Natural disasters or unexpected events
- Geopolitical changes
- Cybersecurity threats
To Wrap It Up
The difference between logistics and supply chain management continues to evolve as technology and customer expectations reshape e-commerce.
While logistics focuses on optimising product movement and storage, supply chain management coordinates the entire network of partners and processes.
Success requires balancing both operational excellence and strategic planning, to reduce costs, improve customer satisfaction, and achieve sustainable growth for your e-commerce brand.
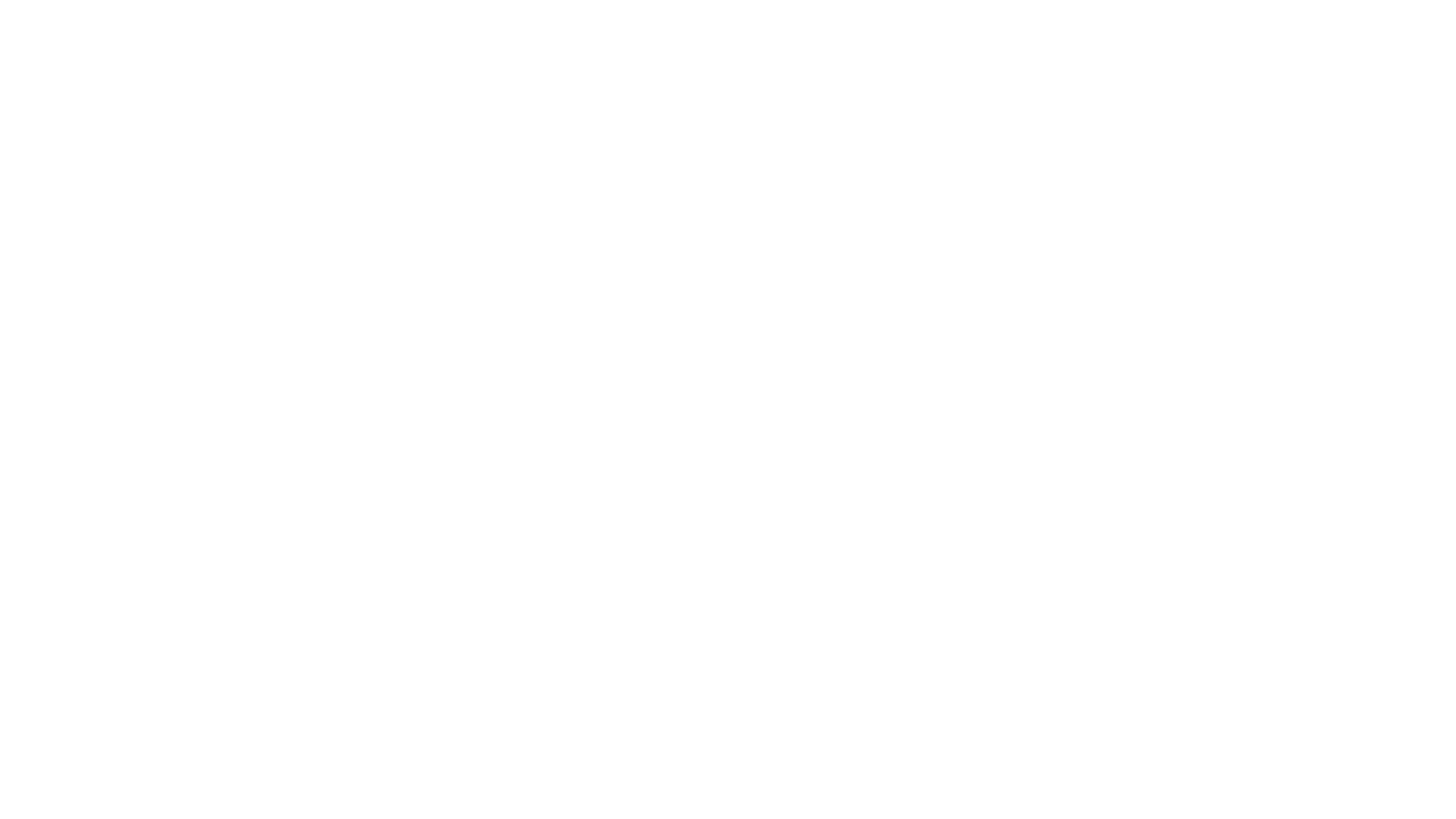
FAQ’s (Frequently Asked Questions on the Difference Between Logistics and Supply Chain Management)
- Is logistics management part of supply chain management?
Yes, logistics serves as an essential component of supply chain management (SCM), as it focuses on moving and storing goods.
- What is the primary difference between logistics and SCM?
Logistics handles specific functions within an organisation such as storage, transport, and product delivery. Supply chain management, however, directs the complete network of organisations, suppliers, manufacturers, and processes required to create and deliver products to customers.
- What comes under supply chain management?
Supply chain management involves
- Strategic network planning
- Materials procurement
- Manufacturing oversight
- Stock management
- Logistics operations
- Distribution systems
- Information technology
- Quality standards
- Continuity planning
- What category does logistics management come under?
Logistics management operates as a core function within supply chain management. The difference between logistics and supply chain management structures shows that logistics typically reports through the supply chain organisation, working alongside procurement and production teams to execute the broader SCM strategy.
Talk to our experts for a customised solution that can maximise your sales funnel
Book a demo